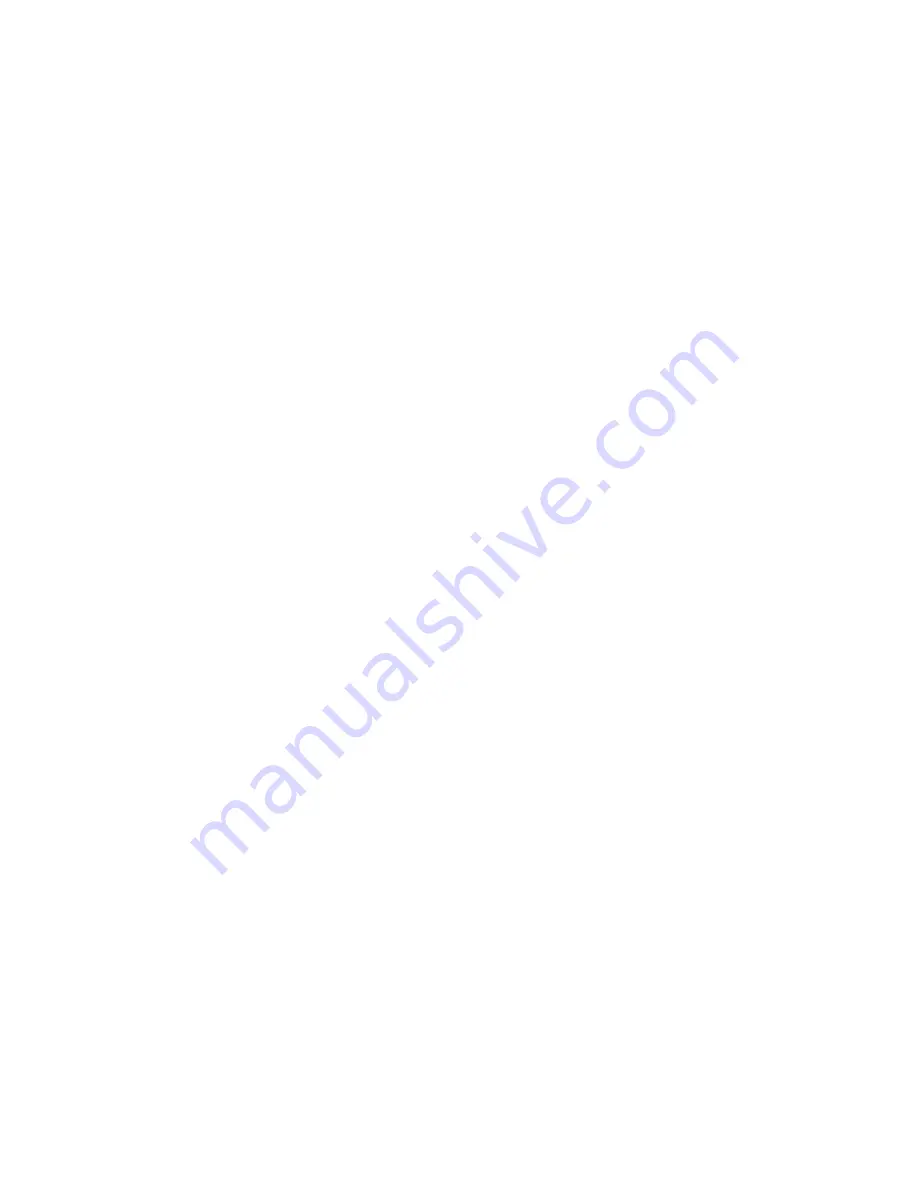
308981 17
6.
Put grease on the diaphragm shaft (15), and
carefully (do not damage the shaft u-cups) run the
diaphragm shaft (15) through the center housing
(11) bore.
7.
Repeat step 5 for the other end of the diaphragm
shaft (15), and torque the fluid-side diaphragm
plates (105) to 80 to 90 in-lb (9 to 10 N-m) at 100
rpm maximum.
Overmolded Diaphragms
: The air cover bolts may
make it difficult to assemble the overmolded
diaphragms on the 515 pump. Two people are
needed. Use a flat surface that fits within the bolt
pattern to apply pressure on the diaphragm that has
already been assembled. Apply pressure until the
diaphragm shaft sticks out of the other end of the
center housing far enough to attach the second
diaphragm assembly. Screw the assembly into the
shaft (15) hand tight.
8.
Install the muffler (3).
9.
Make sure all the check valve parts are in place.
10. See
Fig. 7
.
11. Reinstall the fluid covers (101) and manifolds (102
and 103), and torque the fluid cover and manifold
nuts (109) to 80 to 90 in-lb (9 to 10 N-m). See
Torque Sequence
, page 29.