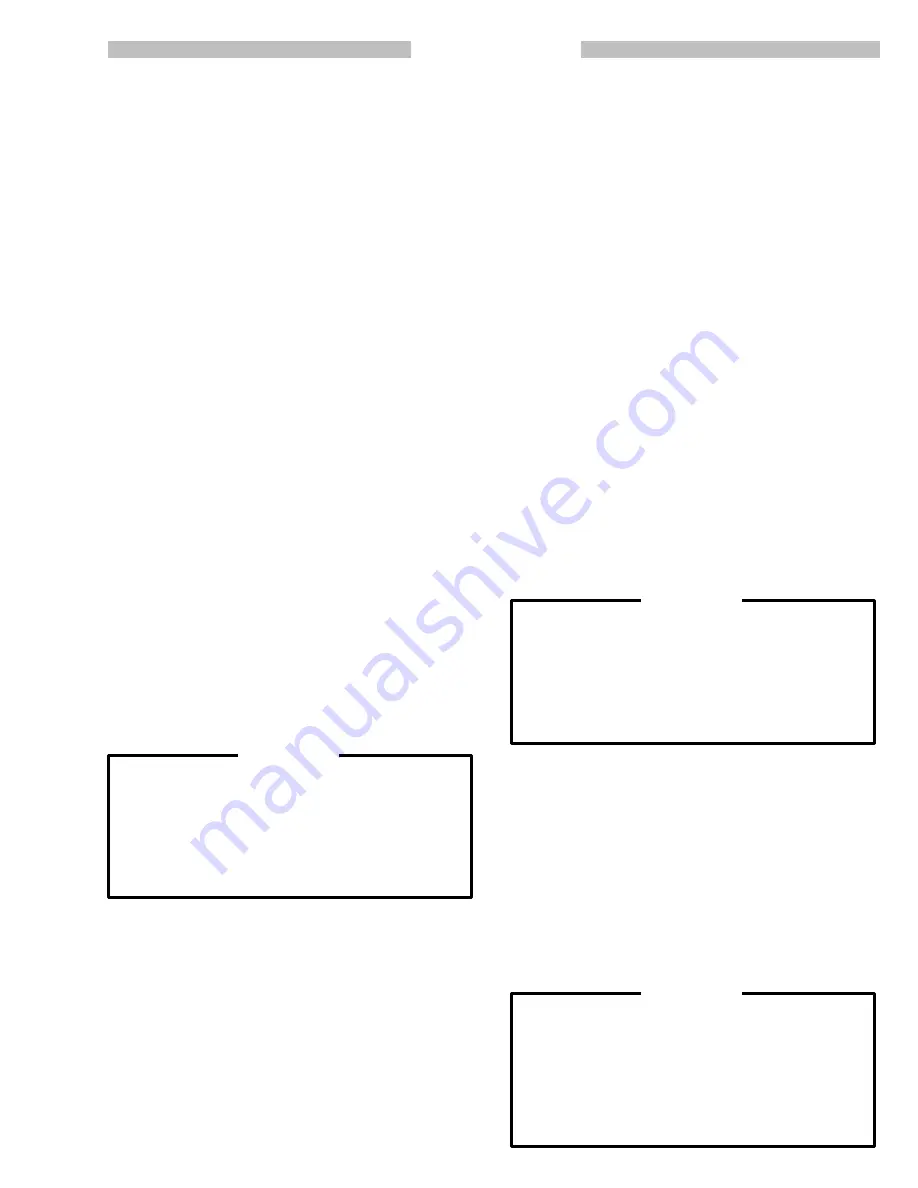
5
INSTALLATION
NOTE:
The Typical Installation on page 4 is only a guide
to selecting and installing system components.
Your installation will depend on the type of fluid
being pumped and your application needs. Con-
tact your Graco distributor for system design as-
sistance.
The accessories mentioned in the text are avail-
able from Graco. See page 20.
Reference numbers and letters in parentheses
in the text refer to the callouts on the drawings.
Mount the pump to suit the type of installation planned.
Be sure the pump is securely bolted to its mounting.
If mounting the pump on a wall, you must reposition the
legs so the pump will be upright. Remove the long bolts
(3, or 55 on
models), nuts (15) and washers (16)
holding the legs (12, 13) in place. Remove two short bolts
(14, or 3 on
models), nuts (15) and washers (16)
from each diaphragm cover (11).
Align the legs with these vacant holes and reinstall using
the long bolts, washers, and nuts. Reinstall the short
bolts in the holes vacated by the legs. T orque the bolts
oppositely and evenly, to 13.5–16 N.m (9.8–12 ft–lb). On
models, torque the long bolts (55) to 13.5–16 N.m
(9.8–12 ft–lb); torque the short bolts (3) to 27 N.m (20 ft–
lb). See Detail C in Fig. 2 and the Mounting Diagram on
page 21.
Screw an air control valve (P) and adapter into the pump
air inlet (G). Working upstream from the air control valve
(P), first install an air line lubricator (E), for automatic lu-
brication of the air director valve assembly. Next, install a
bleed–type master air valve (A), an air regulator (D) to
control pump speed and fluid pressure, and an air line fil-
ter (B) to remove harmful dirt and moisture from the com-
pressed air supply. Install another bleed–type air valve
(A) to isolate the accessories for servicing.
WARNING
A bleed–type master air valve (A) is required in your
system to relieve air trapped between this valve and
the pump after the air regulator is closed. Trapped
air can cause the pump to cycle
unexpectedly,
which could result in serious bodily injury, including
splashing in the eyes, injury from moving parts, or
contamination from toxic fluids.
Connect a
grounded air supply hose (F) to the air control
valve (P). The hose must be at least 6 mm (1/4 in.) ID.
The fluid connections are 1 in. npt(f). Connect a
grounded transfer hose (J) to the pump fluid outlet (K).
Connect a fluid suction hose (L) to the pump fluid inlet
(M). Be sure the fluid connections are tight to avoid leaks.
NOTE:
Do not pressure feed the pump. The ball checks
will not function and the pump will not operate.
NOTE:
The inlet and outlet manifolds can be removed
and turned 180
_
to change the direction the
ports face. Refer to
Repairing the Check
Valves
on page 11 for the procedure.
Dual Inlet Conversion Kit 220–986
Order Conversion Kit 220–986 to convert Pump Model
218–940 to a dual inlet design, allowing you to pump and
mix two fluids in a 1:1 ratio. Each of the two diaphragm
chambers pumps one of the fluids, and the common out-
let aids the mixing process. However since the two dia-
phragms pump alternately, additional plumbing is neces-
sary to ensure complete mixing.
The outlet line should be at least 1 in. diameter tubing or
3/4 in. pipe. Runs shorter than 45 m (150 ft) should use a
100 mm (4 in.) diameter x 0.9 m (36 in.) mixing chamber
fabricated of schedule 40 pipe.
The inlet plumbing and suction lift to the dual inlet pump
must meet certain specifications so the volume of the two
fluids supplied to the pump remains equal, to ensure
proper 1:1 proportioning. The inlet lines must be the
same diameter and length, with the same number of
bends or elbows. The lift requirements of the two inlets
can vary within a range of 0.45 m (18 in.). Use a float
valve set at the 0.45 m (18 in.) level of one of the fluid sup-
ply tanks to ensure that the lift requirement is maintained.
Stainless Steel Ball Conversion Kit 220–987
High density fluids may keep the check balls from seating
and the pump will not operate. The heavier stainless steel
balls supplied in Conversion Kit 220–987 will seat when
you are pumping these fluids.
Air Exhaust Ventilation
WARNING
Be sure to read and follow the warnings and precau-
tions regarding
TOXIC FLUID HAZARD
and
FIRE
OR EXPLOSION HAZARD
on page 2, before oper-
ating this pump.
Be sure the system is properly ventilated for your
type of installation.
If you are pumping
flammable, hazardous or toxic flu-
ids,
operating the
pump submersed,
or operating the
pump in an
enclosed area,
position the pump so as to
avoid exhausting air toward people; the exhaust air must
be vented to a safe area, away from all people. Y
ou
MUST
use a grounded air hose (see “
Grounding
” be-
low). The exhaust line should end in a container which
can catch any fluid that would be exhausted if a dia-
phragm ruptured. See Detail A, Fig. 2, and the
ACCES-
SORIES
section on page 20 to order the
necessary
plumbing.
Grounding
WARNING
This pump must be grounded. Be sure to read and
follow the warnings and precautions regarding
FIRE
OR EXPLOSION HAZARD
on page 2 before oper-
ating this pump.
To reduce the risk of static charge build–up on the
muffler which can cause static sparking, the ex-
haust line
MUST
be a grounded air hose.
PTFE
PTFE
PTFE