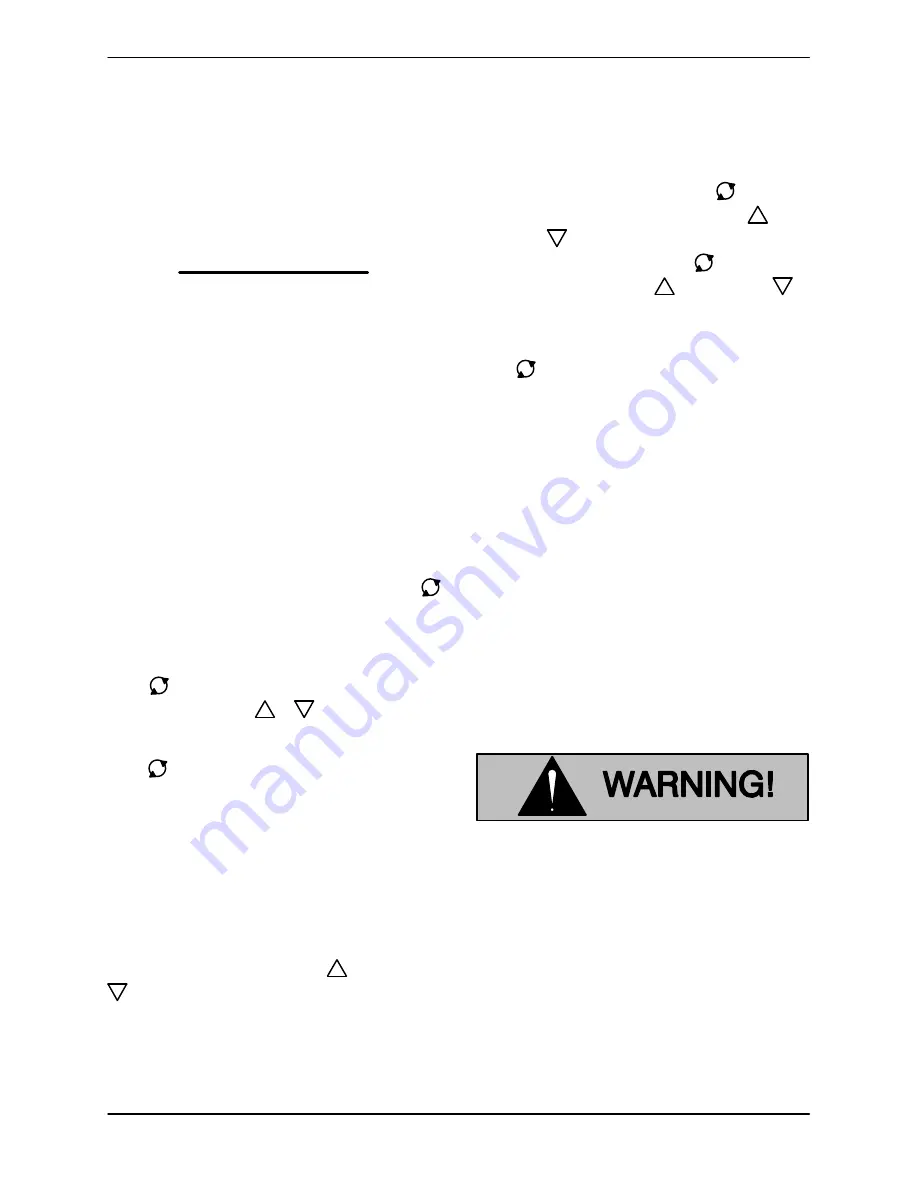
OM-07174
SUPER T SERIES
OPERATION
PAGE C - 4
EPS Calibration
NOTE
Zero offset and span adjustments are only neces
sary to calibrate a new unit, or when replacing the
transducer. Once calibrated, “ON” and “OFF” set
points will be stored in the unit's memory. Liquid
level adjustments will be used whenever “ON” and
“OFF” liquid levels must be reset.
There are two reasons for the user to calibrate the
unit. When power is applied, the unit confirms set
points and other calibration information for validity.
If the setpoints are not valid, the LCD screen shows
“EEP bAd” and the unit must be recalibrated. Also,
if the unit is moved, or some other external change
takes place, the unit must be recalibrated.
Zero Adjustment
Zero adjustment tells the unit when the transducer
is exposed to zero water (atmospheric) pressure.
When recalibration is desired, hold the transducer
in hand and apply power to the unit. The LCD
screen will display “Level ABC”. Press and hold
for 5 seconds. The LCD screen displays “Input?
External XDUCR”. Perform the following calibration
procedures.
Press
3 times and the LCD screen will display
“Calibrate Zro”. Press
or
until a character or
number on the display changes.
Press
to accept the entry and advance to “Cali
brate Span”.
Span Adjustment
Span adjustment calibrates the unit to a known wa
ter pressure (depth). To set:
Submerge the transducer to an exact known
depth. At “Calibrate Span”, the span setting in the
unit's memory will display. Press
to increase or
to decrease the value unitl the LCD screen dis
play equals the actual known depth of the trans
ducer.
Level Adjustment
Level adjustment tells the unit when to turn the
pump on and off. To set:
From “Level ABC” display, press
once and
“Pump Setpt A On” will display. Press
to in
crease or
to decrease to the desired level at
which the pump turns on. Press
to advance to
“Pump Setpt A Off”. Press
to increase or
to
decrease to the desired level at which the pump
turns off.
Press
again to advance to “Pump Setpt B On”. If
“B” is to be used, repeat the procedure described
above for adjusting level “A”.
Horn Delay
The horn delay is pre‐set from the factory through
the engine control panel, therefore this function is
not utilized through the EPS.
ROUTINE OPERATION
Adjust the engine speed to achieve the desired
output. Do not exceed the factory set engine speed
and system operating pressure. Do not operate
below the recommended operating speed (if appli
cable).
Never tamper with the governor to gain
more power. The governor establishes
safe operating limits that should not be
exceeded. Refer to the Performance
Curve in Section E for the maximum
continuous operating speed for this
pump.
A Gorman‐Rupp automatic air release valve may
be installed in a bypass line, or the bypass line may
be left open.