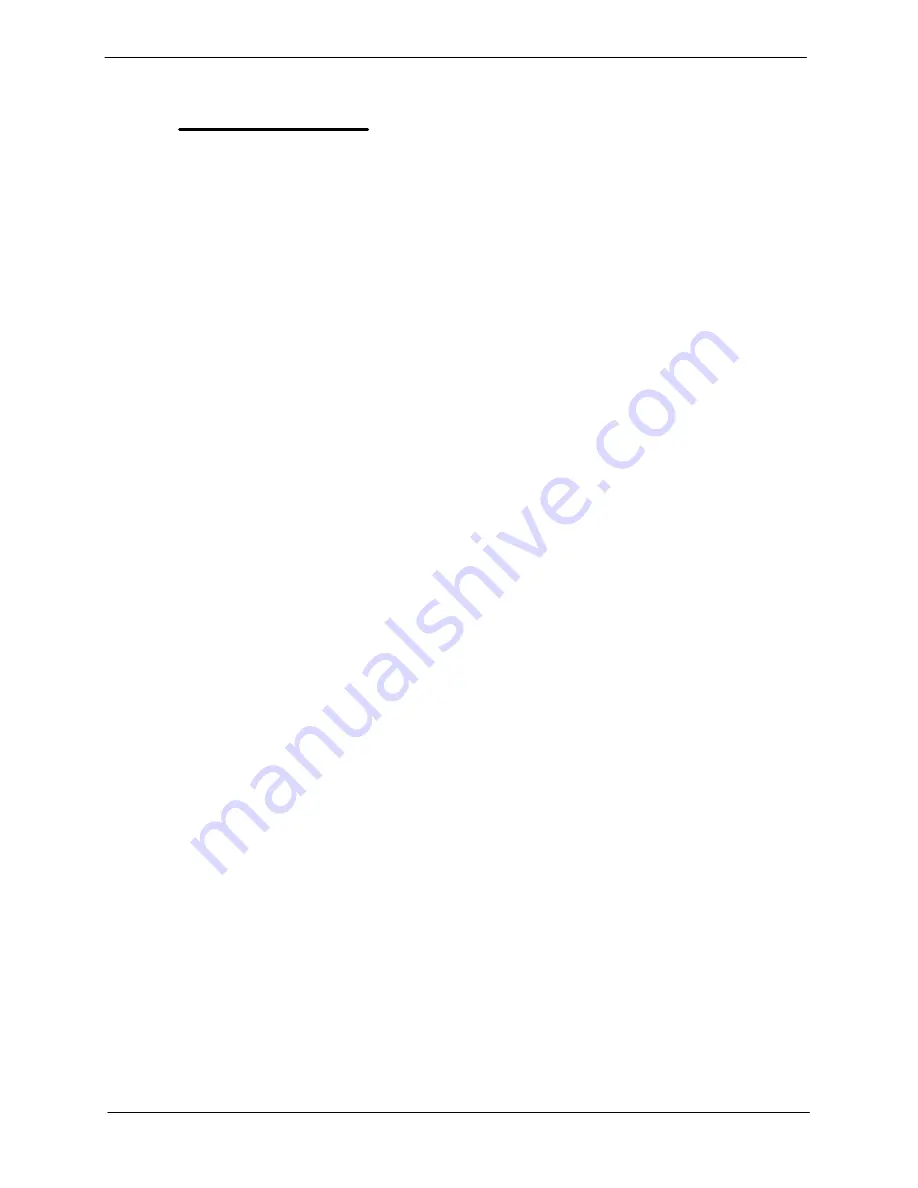
SUPER T SERIES
OM-07174
PAGE B - 5
INSTALLATION
with the pumping unit has a range of 8 psi to 12 psi
(0,5 to 0,8 bar).
The secondary regulator output pressure of 10
inches of water column is used to illustrate a typical
system. Actual pressure may be higher or lower
depending on code requirements. The secondary
regulator supplied with the pumping unit has a
range of 4 inches to 12 inches (102mm to 305mm)
of water column.
CONNECTING FUEL SUPPLY LINE TO
THE UNIT
There is a 1‐inch pipe connection on the outside of
the enclosure for connecting the incoming gas
supply line. Inside the enclosure, there is a 1‐inch
pipe tee in the engine fuel line. The tee is equipped
with a reducer and a 1/4‐inch pipe plug. Remove
the pipe plug and install a pressure gauge rated in
inches of water column.
Open the fuel supply to the regulator and observe
the pressure gauge. If the reading is less or greater
than 10 inches of water column, remove the cap on
the regulator to expose the adjusting screw plug
beneath it. Turn the adjusting plug clockwise to in
crease the fuel supply or counter‐clockwise to de
crease the fuel supply.
When the supply is properly adjusted to 10 inches
of water column, reinstall the protective cap over
the adjusting screw on the regulator. Remove the
pressure gauge from the fuel line and reinstall the
1/4‐inch pipe plug to avoid vibration damage to the
gauge.
CHANGING FUEL TYPE
If it is necessary to change the type of fuel from nat
ural gas to LP gas or vice‐versa, the fuel line inside
the enclosure to the engine must first be switched
to the correct regulator on the engine for the de
sired fuel. After switching the fuel line, set the tog
gle switch on the engine control to the desired fuel.
This tells the engine control module the fuel has
been changed so the engine can compensate for
the change in fuel supply. After these changes are
complete, check the fuel pressure as described in
CONNECTING FUEL SUPPLY LINE TO THE
UNIT
.
SUCTION AND DISCHARGE PIPING
Pump performance is adversely effected by in
creased suction lift, discharge elevation, and fric
tion losses. See the performance curve and notes
on Page E‐1 to be sure your overall application al
lows pump to operate within the safe operation
range.
Materials
Either pipe or hose maybe used for suction and
discharge lines; however, the materials must be
compatible with the liquid being pumped. If hose is
used in suction lines, it must be the rigid‐wall, rein
forced type to prevent collapse under suction. Us
ing piping couplings in suction lines is not recom
mended.
Line Configuration
Keep suction and discharge lines as straight as
possible to minimize friction losses. Make mini
mum use of elbows and fittings, which substantial
ly increase friction loss. If elbows are necessary,
use the long‐radius type to minimize friction loss.
Connections to Pump
Before tightening a connecting flange, align it ex
actly with the pump port. Never pull a pipe line into
place by tightening the flange bolts and/or cou
plings.
Lines near the pump must be independently sup
ported to avoid strain on the pump which could
cause excessive vibration, decreased bearing life,
and increased shaft and seal wear. If hose‐type
lines are used, they should have adequate support
to secure them when filled with liquid and under
pressure.
Gauges
Most pumps are drilled and tapped for installing
discharge pressure and vacuum suction gauges.
If these gauges are desired for pumps that are not
tapped, drill and tap the suction and discharge
lines not less than 18 inches (457,2 mm) from the
suction and discharge ports and install the lines.
Installation closer to the pump may result in erratic
readings.