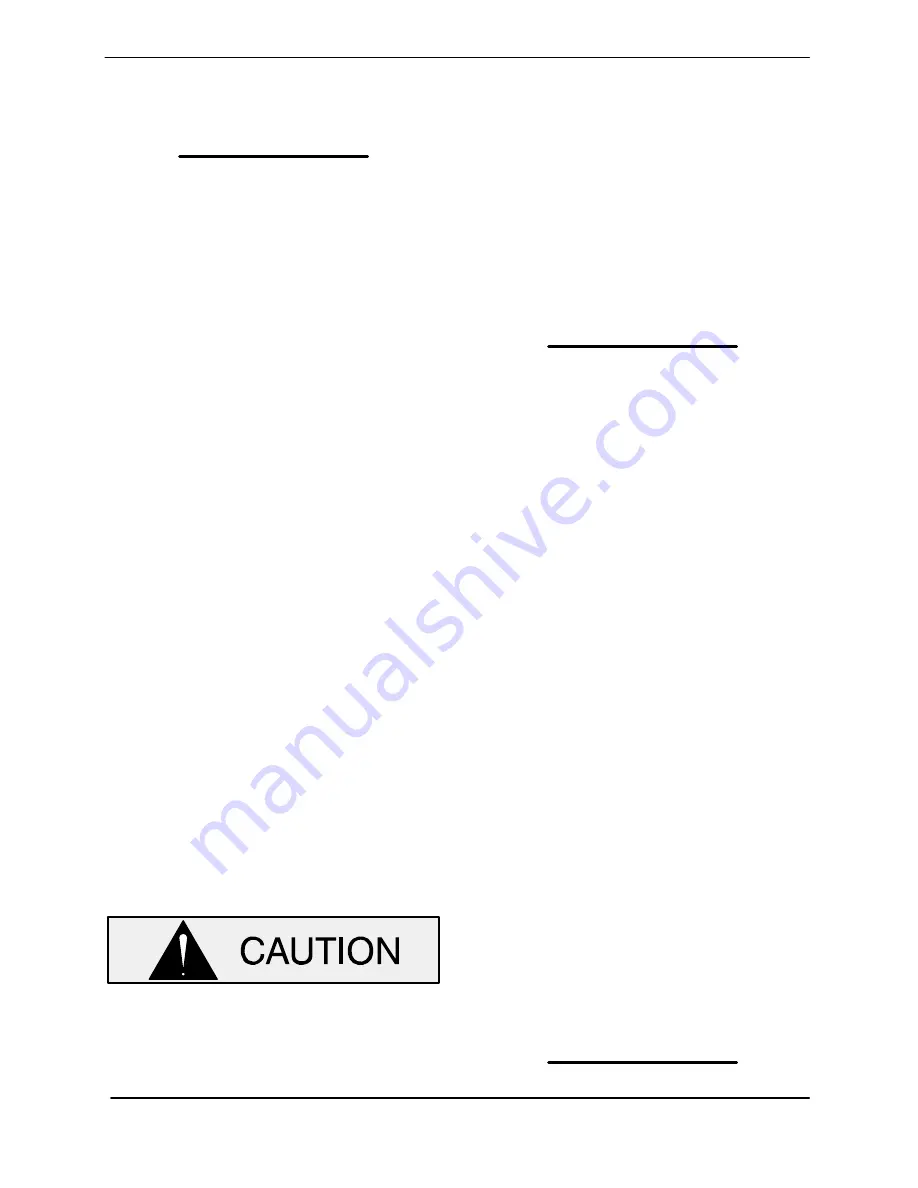
OM-05724
JD Series
PAGE E - 15
MAINTENANCE AND REPAIR
(213) may be heated to ease installation of the roller
bearing outer racer and rollers.
7. Position the lower bearing housing (213) on a
flat surface with the impeller side up. Slide or
press the roller bearing outer race and rollers
into the bearing housing until fully seated.
8. Place a spot of grease in each of the holes in the
lower bearing housing for the springs (425) and
install the springs in the holes. Slide the bearing
housing and bearing onto the shaft until the roll
ers in the outer race are seated over the inner
race previously installed on the shaft. Align the
holes, and secure the lower bearing housing to
the bearing cover (206) with the screws (216).
9. Install the angle ring (424) against the roller
bearing. Install a new tabbed lockwasher (415),
and screw the nut (416) onto the shaft until the
bearings are securely seated. Back the nut off
to align the nearest slot with a corresponding
tab on the washer, and bend the tab over to se
cure in place.
10.Lubricate a new O‐ring (219), and install it in the
groove in the lower bearing housing (213).
11.Slide the lower bearing bracket cover (217)
over the shaft, and secure it to the lower bearing
housing with the screws (221).
12.Guide the assembled shaft and bearings
through the stator/motor housing (246) until the
upper bearing (203) seats squarely in the motor
cover (230) and lower the bearing bracket (213)
is fully seated in the motor housing (302).
Upper Seal Installation
All references are to FIGURES E-2 and E-3.
If a new seal is being installed, do not un
wrap it until ready to install; seal compo
nents
must
be kept clean. Handle seal
parts with extreme caution to prevent dam
age. Use care not to contaminate the preci
sion‐finished faces; even fingerprints on
the faces can shorten seal life.
NOTE
Use hand pressure only to install seal components.
A push tube cut from plastic pipe approximately the
same O.D. as the stationary seat is a useful aid
when installing these components. It is recom
mended that the pump be inverted during seal as
sembly.
1. Lubricate the motor shaft and the seal cavity of
the lower bearing housing (213).
2. Unwrap the seal components. Check that the
seal faces are clean and undamaged. If neces
sary to clean, use a clean tissue and wipe in a
concentric pattern.
3. Lightly oil the seal stationary seat O‐ring. Place
a clean tissue over the seal face, and install the
stationary seat and O‐ring in the lower bearing
housing (213) with the seal face toward the im
peller end of the shaft.
4. Lightly oil the seal rotating element O‐ring, and
slide the rotating element and O‐ring onto the
shaft until the sealing faces contact.
5. Place a drop of grease in the spring cups of the
seal retainer, and install the springs. Install the
retainer and springs in the rotating element,
and align the bottom of the retainer with the bot
tom of the rotating element. Secure the retainer
with the retaining setscrews.
6. Lubricate the O‐rings (251, 252 and 403) and in
stall them in the grooves in the seal housing
(257). Press the seal housing into the motor
housing (302) until fully seated, and secure with
the screws (254).
NOTE
Test the upper seal as described in
SEAL TESTING
before installing and testing the lower seal assem
bly, and installing the pump end components (see
PUMP END REASSEMBLY
).