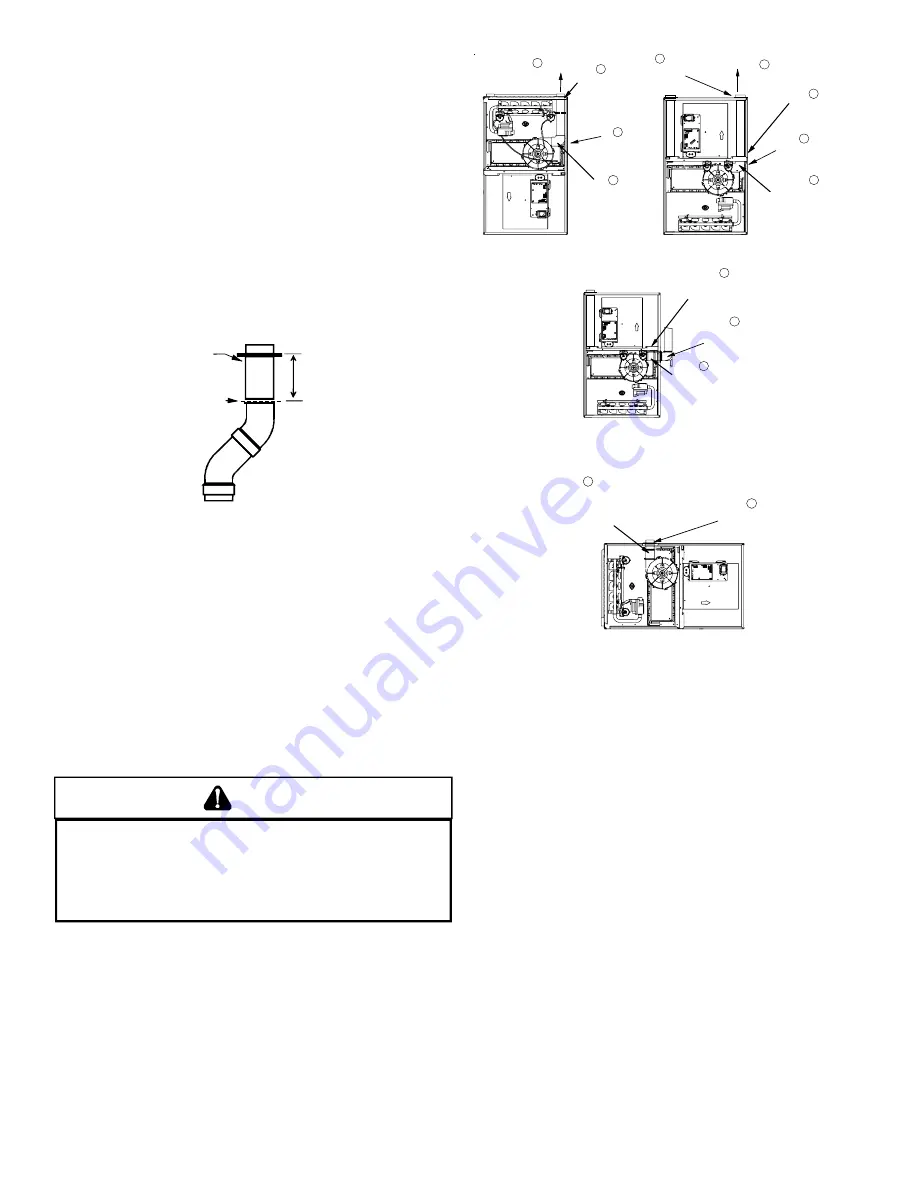
15
2.
Upflow
and
Counterflow
units
.
Loosen the worm gear hose clamps on the rubber elbow
and detach it from both the induced draft blower and the
vent/flue pipe.
3.
Upflow
and
Counterflow
units
.
Remove the vent/flue pipe from the furnace.
4.
Cut the vent/flue pipe 3.75 inches from the flanged end of
the pipe.
See Vent/Flue Pipe Cuts figure.
The section of
pipe attached to the coupling will reach through the side
panel to the induced draft blower. Discard remaining pipe
and elbows.
Counterflow
units.
Cut the vent/flue pipe 3.75 inches from the blower deck
coupling.
See Vent/Flue Pipe Cuts figure.
Save vent/flue pipe
attached to blower deck coupling for use in the alternate
location. Discard remaining pipe and elbows.
FLANGE
CUT
HERE
3.75"
5.
Remove plastic plug from alternate vent/flue location.
Relocate and install plug in standard vent/flue location (top
cover).
Counterflow
units.
Remove plastic plug from alternate vent/flue location.
Relocate and install plug in standard vent/flue location
(basepan). Plug remaining hole in blower deck with plastic
plug included in the drain kit bag.
6.
Upflow
and
Counterflow
units
.
Insert cut section of vent/flue pipe and coupling into alternate
vent/flue location. Using a rubber coupling and worm gear
hose clamps from the drain kit bag, attach the vent/flue pipe
and coupling to the induced draft blower. Secure the
coupling to the cabinet using the screws removed in step 1
or with field-supplied 3/8” #8 self drilling screws.
WARNING
T
HE RUBBER ELBOW IS NOT DESIGNED TO SUPPORAT A LOAD.
W
HEN THE
RUBBER ELBOW IS MOUNTED EXTERNALLY TO THE FURNACE CABINET,
EXTREME CARE MUST BE TAKEN TO ADEQUATELY SUPPORT FIELD-SUPPLIED
VENT/FLUE PIPING, AS DAMAGE CAN RESULT IN LEAKS CAUSING BODILY
INJURY OR DEATH DUE TO EXPOSURE TO FLUE GASES, INCLUDING CARBON
MONOXIDE.
7.
Upflow
and
Counterflow
units
.
For
upright installations
, externally mount the rubber elbow
to the vent/flue coupling using a worm gear hose clamp.
Secure field supplied vent/flue piping to the rubber elbow
using a worm gear hose clamp.
NOTE:
Use of the alternate
vent/flue location for upright installations, requires the drain
trap be installed on the same side of the unit as the flue
pipe.
8.
Upflow
and
Counterflow
units
.
For
horizontal installations
, externally secure the field-
supplied vent/flue pipe directly to the vent/flue coupling using
a PVC or ABS coupling or elbow.
5
ADDITIONAL PLUG
FROM DRAIN KIT
7
EXTERNALLY
MOUNT
RUBBER ELBOW
6
SECURE TO
ID BLOWER WITH
RUBBER COUPLING
AND HOSE
CLAMPS
COUNTERFLOW/UPRIGHT
(UPFLOW SIMILAR)
UPFLOW
REMOVE
4 SCREWS
3
REMOVE
PIPE
2
DETACH RUBBER
ELBOW FROM
ID BLOWER AND
VENT/FLUE
PIPE
1.
REMOVE
4 SCREWS
2
DETATCH RUBBER
ELBOW FROM
ID BLOWER AND
VENT/FLUE
PIPE
COUNTERFLOW
3
REMOVE
PIPE
5
REMOVE
AND RELOCATE
5
REMOVE
AND RELOCATE
1
REMOVE
3 SCREWS
1
UPFLOW/HORIZONTAL
(COUNTERFLOW SIMILAR)
6
SECURE TO
ID BLOWER WITH
RUBBER COUPLING
AND HOSE
CLAMPS
6
SECURE TO
CABINET WITH
SCREWS
Alternate Vent/Flue Location
A
LTERNATE
C
OMBUSTION
A
IR
I
NTAKE
L
OCATION
The alternate combustion air intake location consists of a large,
unobstructed hole (alternate vent connection is aligned with the
Induced Draft Blower). To use the alternate combustion air intake
location, refer to the following steps, and the “Alternate Combus-
tion Air Intake Location” figure.
NOTE:
Counterflow unit instructions follow the upflow instructions.
1.
Remove and save the four screws securing the combustion
air intake coupling to the furnace’s top panel (upflow).
Counterflow
units.
Remove and save the four screws securing the combustion
air intake coupling to the basepan. Remove an additional
three screws securing the furnace’s internal combustion
air intake pipe to the blower deck.
2.
Remove the combustion air intake coupling and gasket from
the top panel.
Counterflow
units.
Remove the combustion air intake pipe from the furnace
and cut the pipe at the basepan coupling. Save the basepan
coupling and gasket from the blower deck coupling for use
in the alternate location. Discard the remaining pipe.
3.
Remove plastic plug from alternate combustion air intake
location. Relocate and install plug in standard air intake
location (top cover).
Summary of Contents for GMS95
Page 34: ...34...