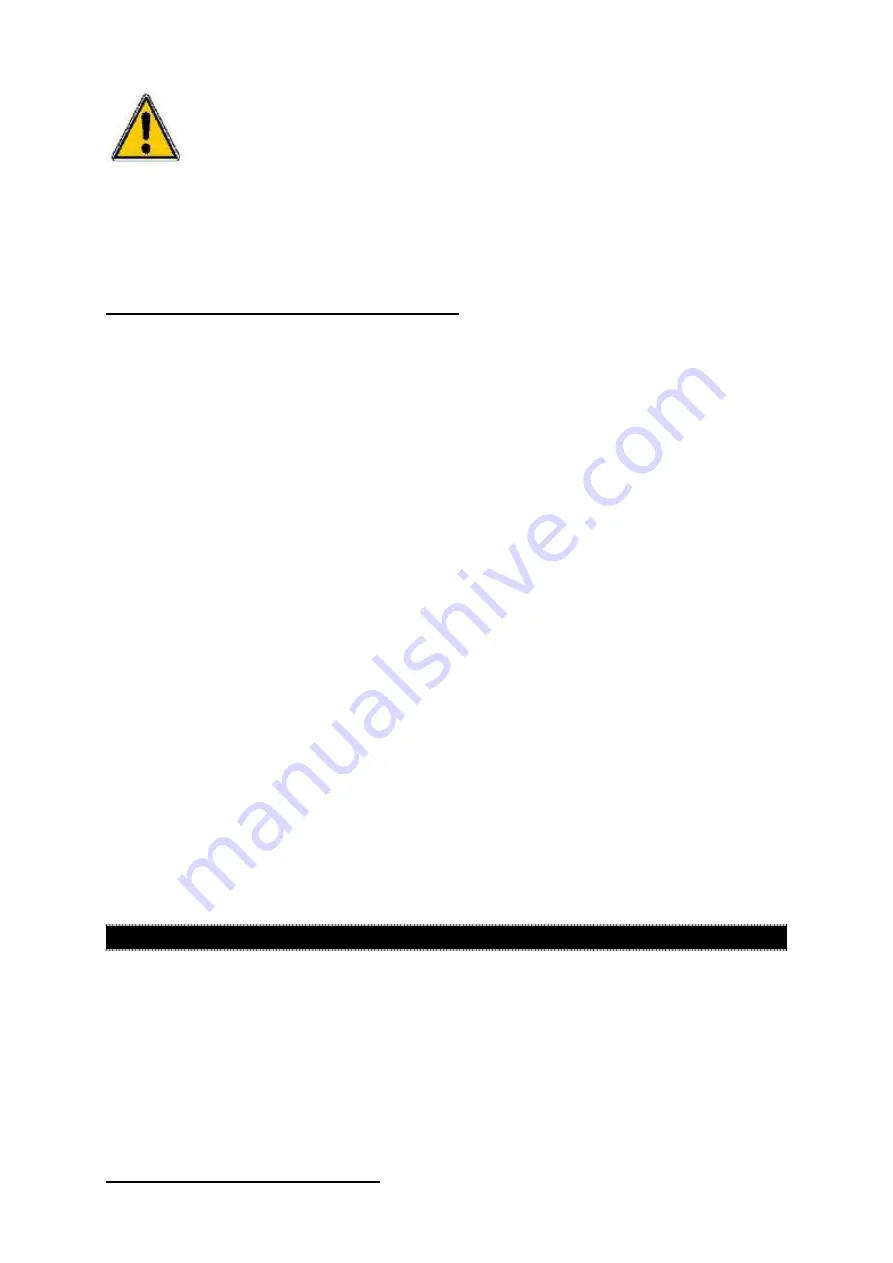
Original Instruction Manual
En
11
10/2016
WARNING
Don’t apply big pressure to the machine.
Best results can be obtained by only a slight pressure on the tool; Forcing and
excessive pressure will damage the disk and cause serious personal injury.
Instruction for abrasive wheels and discs
Abrasive wheels should not be mounted on makeshift apparatus. They should be
mounted on the type of machine for which they are intended. These appear to be
obvious precautions, but accidents still occur because wheels are mounted on
home-made or improvised apparatus quite unsuitable for the work. Likewise, accidents
are caused by heavy wheels being fitted to spindles designed to take only the lightest
of wheels. As a result, vibration is excessive and breakages occur. On no account
should an abrasive wheel be screwed on to the tapered spindle of a buffing machine.
This dangerous method of mounting is likely to result in the breaking of the wheel
owing to the wedging action of the tapered spindle.
The new wheels should be carefully unpacked, cleaned with a brush and examined for
possible damage in transit. In unpacking, the careless use of a tool may cause damage
to the wheel. The soundness of wheels can be further checked by tapping them with a
light, non-metallic implement. This is known as the ‘ring’ test. Wheels must be dry and
free from sawdust for the ring test otherwise the sound will be deadened. It should also
be noted that organic bonded wheels do not emit the same clear metallic ring as
inorganic bonded wheels. Heavy wheels should be supported on a clean hard floor for
the ring test while light wheels should be suspended from their hole on a finger or small
pin. If the wheel sounds dead, for example due to cracking, it should not be used.
All abrasive wheels are relatively fragile. It should not be assumed that organic bonded
wheels (resin, shellac, rubber) will stand rough handling.
As the wheel wears down in use, the effective peripheral surface speed will reduce if
the rotational speed remains constant and may result in a reduced grinding efficiency.
To make sure the machine work smoothly, the wheel should be replace with the
maximum diameter less than 125 mm.
MAINTENANCE
Keep the ventilation openings clear and clean the product regularly.
If something unusual occurs during use, switch off the supply and disconnect the plug.
Inspect and repair the tool before using it again.
Repair of the tool must only be carried out by a qualified repair technician.
Repair or maintenance by unqualified personnel can lead to a risk of injury.
Use only identical spare parts for repairing a tool.
Clean the housing only with a damp cloth-do not uses any solvents! Dry thoroughly
afterwards.
Replacement of carbon brushes
The carbon brushes are expendable. It is keeping abrasion during use.