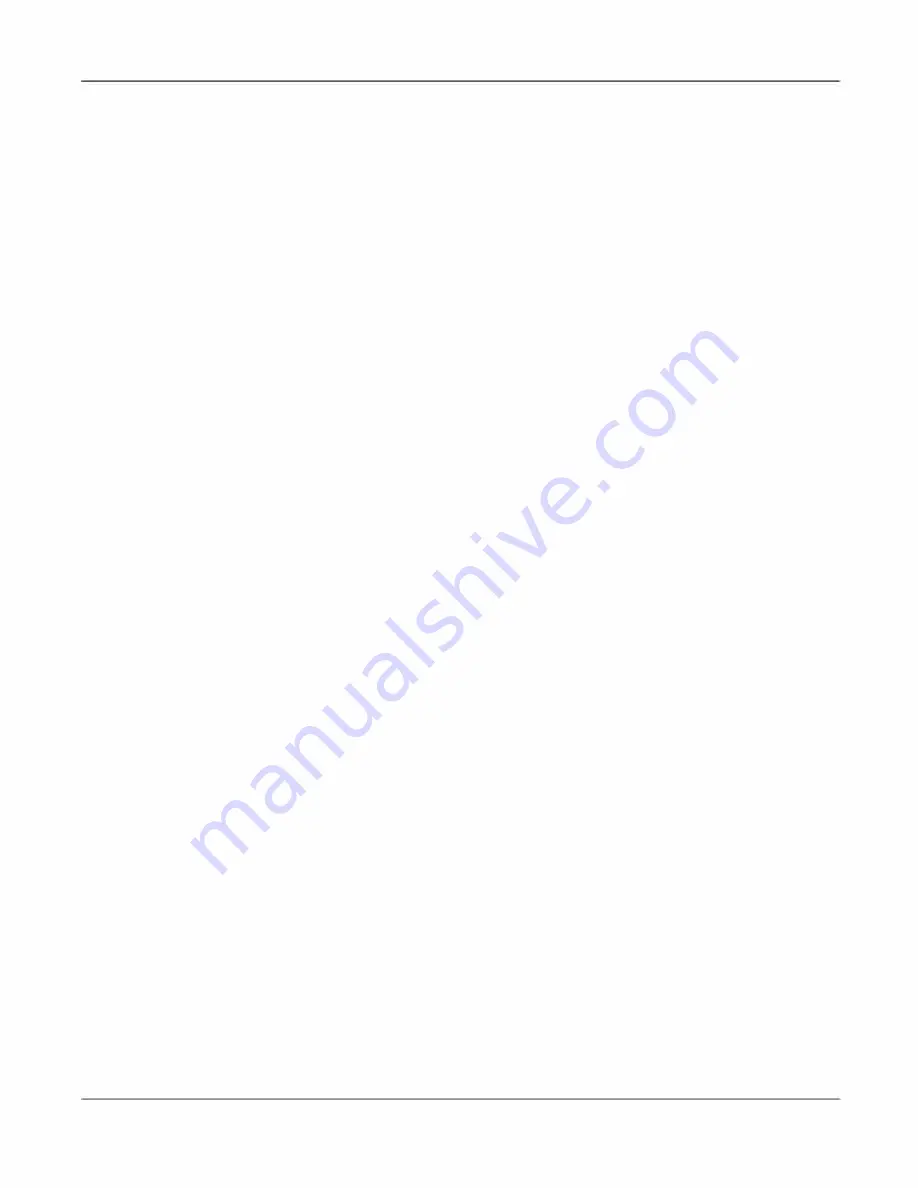
TS200
5.3-4 Calibrate Level Procedure
The integral tilt sensor of the TS200 control module
must be calibrated when the machine is perfectly
level; an EZcal hand-held device is required to carry
out this procedure:
1. Ensure the MEWP is level front to back and side
to side. Use a digital level and a jack to level as
required.
2. Connect EZcal and enter the ·�cCESS LEVEL'.' 2
code (3939) to enable calibrations
3. Select the 'TILT SETUPS" menu (available from
the "SETUPS" menu) and select the
"CALIBRATE LEVEL'.' option
4. The display will show "YES: ENTER, NO: ESC",
asking for confirmation that the vehicle is level
5. Press the ENTER button to confirm
6. The display will now show the current tilt
measurements; if the leveling procedure was
successful then
7. Both the "X" and "Y" tilts should be about zero
8. Press the ESC button to exit the "CALIBRATE
LEVEL'.' option
9. If the tilt measurements are not zero in step 6, try
the procedure again - press the ESC button then
the ENTER button and repeat from step 4
10. If the tilt measurements still cannot be zeroed,
check that the vehicle is properly parked on level
ground, and check that the TS200 control
module is correctly and securely installed
on a vertical surface of the vehicle, with the
connectors at the bottom.
Section 5 - Procedures
5.3-5 Calibrate Load Procedure
The TS200 control module requires calibration before
it can estimate platform load; calibration records the
lift cylinder pressure at various platform heights, both
fully loaded and empty. Use a known accurate weight
of 240Kg (530lbs.) centered on the platform with the
extension deck fully retracted. After the calibration
procedure is enabled using an EZcal hand-held
device, the MEWP platform is fully raised and lowered
three times:
A. DYNAMIC
calibration - fully loaded
platform raised & lowered in one continuous
movement
B. LOADED
calibration - fully loaded platform
raised & lowered with stops to take
measurements
C.
EMPTY
calibration - unloaded platform
raised & lowered with stops to take
measurements
IMPORTANT
Any changes to the machine mechanics,
hydraulics, etc. may require re-calibration!
The following procedure must be followed
COMPLETELY to calibrate the TS200; throughout the
procedure various checks are made - if any problem
is detected the procedure stops and displays a
FLASHING failure message. Explanations of each
message and suggested corrections can be found in
the document at the end of this procedur
@J
NOTE
If the calibration procedure is interrupted, completed
phases need not be repeated. A "REDO" prompt will
appear - answer "NO" if there is no reason to repeat
the phase, or "YES" if the phase must be repeated (for
example, a significant mechanical or hydraulic change
has been made).
63
1330ED
&
1530ED micro
GMG
Summary of Contents for 1330-ED
Page 4: ...Notes 4 1330ED 1530ED micro GMG...
Page 24: ......
Page 25: ...Section 2 Maintenance Tables and Diagrams 25 1330ED 1530ED micro GMG...
Page 31: ...Section 3 System Component Identification and Schematics 31 1330ED 1530ED micro GMG...
Page 38: ...Notes 1330ED 1530ED micro GMG...