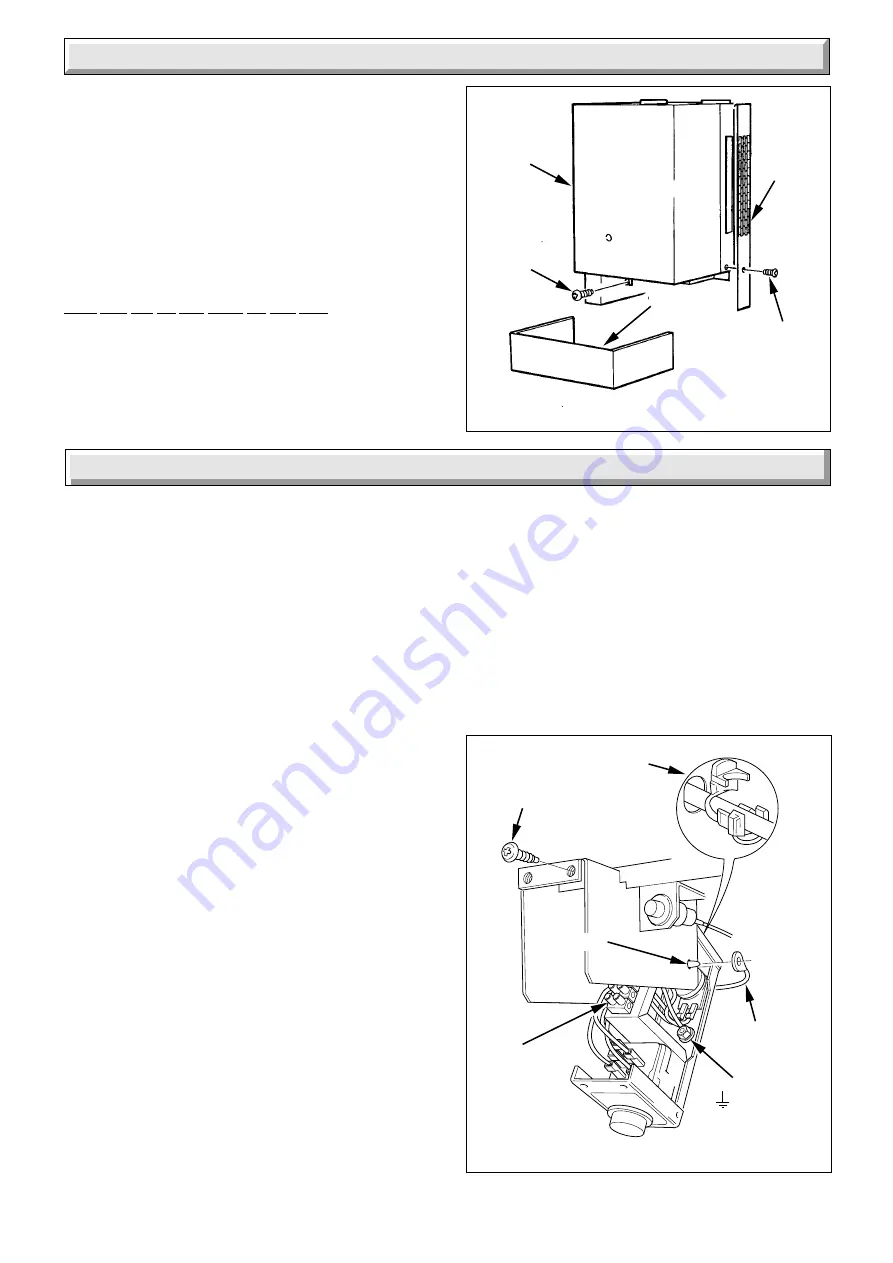
11
221460C
4 Installation
4.3 Gas and Water Connection
Connect the gas supply to the Rc
1
/
2
in gas cock.
The whole of the gas installation, including the meter, should be
inspected, tested for soundness and purged in accordance with
the current issue of BS6891.
Connect the water to the boiler, using nuts and olives supplied,
to BS2871 copper tube.
4.4 Casing
Refit the outer casing by hooking on at the top and securing with
the screws previously removed, see diagram 4.1.
Make sure that the side grilles are kept clear.
Diagram 4.1
APPLIANCE PREPARATION
CONTROL
COVER
SECURING
SCREW
SIDE
GRILLE
OUTER
CASE
2410
SECURING
SCREW
5.1 Electrical Connection
WARNING. The boiler must be earthed and have a permanent
mains supply.
To remove the control box release the two screws at the front,
see diagram 5.1, lower the box until it is clear then push
backwards to disengage the hinge at the rear, see diagram 5.1.
Take care not to damage the thermostat and capillaries.
Thread the mains lead through the clamp in the rear of the
control box cover and connect to the terminal strip.
The mains cable outer insulation must not be cut back external
to the cable clamp.
When making connections, make sure that the earth conductor
is made of a greater length than the current carrying conductors,
so that if the cable is strained the earth conductor would be the
last to become disconnected.
5.2 Pump and External Controls Connections
The pump must be wired into the boiler control box as shown in
diagram 5.2.
Any external controls must only be wired to interrupt the Red link
between terminals 9 and SL.
Take the strain relief grommets from the loose items pack.
Place around the external controls and pump connection cables
respectively.
Squeeze the sides of the grommets when pushing them into the
obround holes in the rear of the control box, see diagram 5.1.
Make sure the supply cable and all external cables are secured.
Diagram 5.1
CONTROL BOX
SECURING
SCREWS
EARTH
POST
TERMINAL
STRIP
RETAINING
STRAP
FASTENER
5352
STRAIN
RELIEF
GROMMET
5.3 Testing - Electrical
Checks to ensure electrical safety should be carried out by a
competent person.
After installation of the system, preliminary electrical system
checks as below should be carried out.
1. Test insulation resistance to earth of mains cables.
2. Test the earth continuity and short circuit of all cables.
3. Test the polarity of the mains.
The installer is requested to advise and give guidance to the
user of the controls scheme used with the boiler.
5 Electrical Wiring