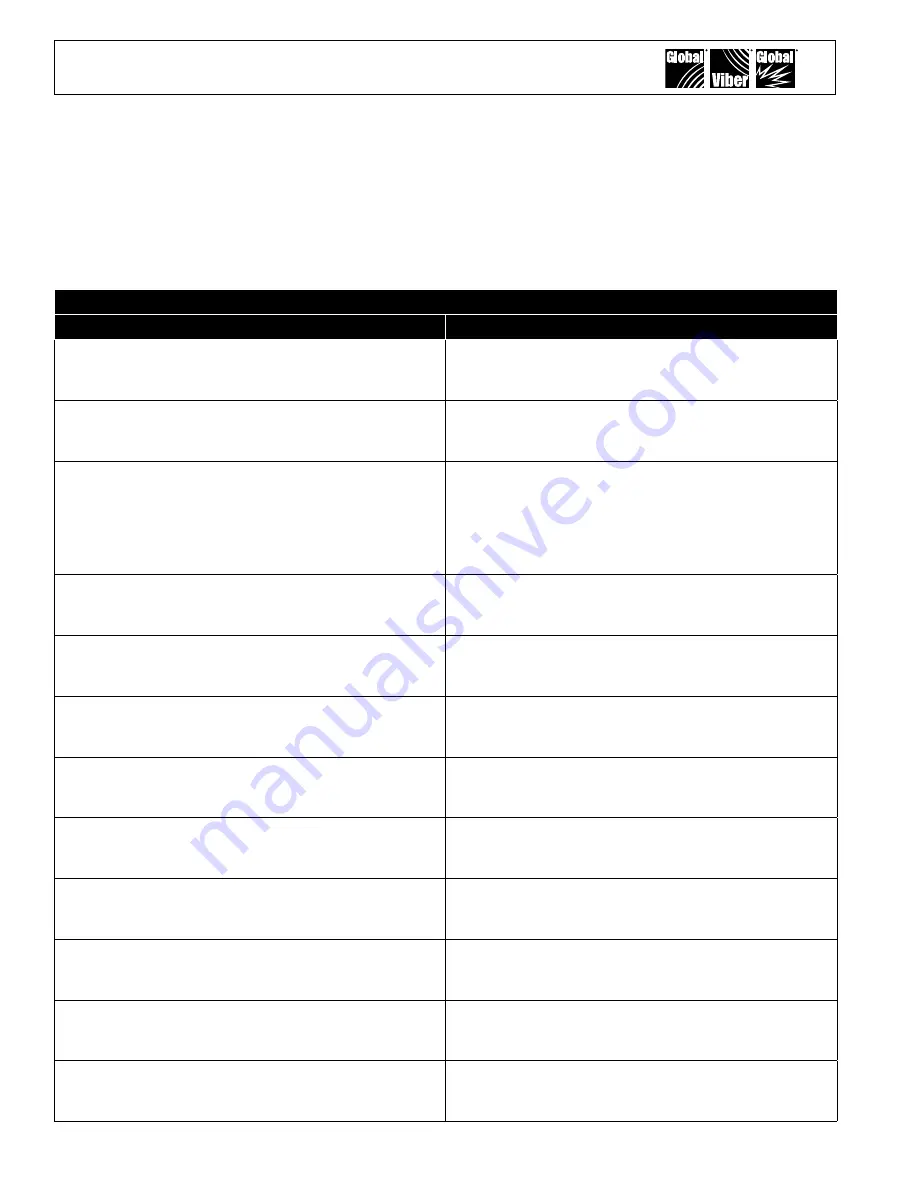
26
Global Manufacturing, Inc
®
800.551.3569
TOLL FREE USA & CANADA
1801 East 22nd Street
501.374.7416
TEL
501.376.7147
FAX
Little Rock, AR 72206 USA
w w w. G l o b a l M a n u f a c t u r i n g . c o m
Appendix A - Troubleshooting
Prior to shipment, all Global Air Blasters are tested for pressure and function according to corresponding
pressure vessel regulations and quality manufacturing specifications. Despite the simple and sturdy
construction, malfunctions can occur due to the kind of application, installation, and/or operation. The
following list should help identify the causes of some problems that occur and gives possible solutions
to eliminate those problems.
Control Valve
= 3-Way Normally Open Manual or Solenoid Valve.
Operating Valve = Quick Exhaust Valve.
PROBLEM: Air Blaster discharges with weak or no blast.
PROBABLE CAUSE
SOLUTION
Air leakage in control valve or operating valve.
Check control valve and operating valve for
wear, damage, contamination. Check for system
leaks.
Control or operating valve is malfunctioning.
Check air filtering system. Clean or repair
valves as needed.
Control valve is too far from the Air Blaster, or
the size of the valve is too small.
Control valve must be within 100 feet of the
Air Blaster. If distance is greater than 100 feet
move it closer to the Blaster. Be sure valves are
the recommended size. A ¾" control valve must
be used and connected by a ¾" airline to the
Air Blaster.
Piston lodged in operating valve due to
contamination.
Disassemble and clean operating valve
assembly. Check filter element in filter
regulator.
Low air pressure.
Air Blaster not completely filled before it is
discharged.
With manual firing give the Air Blaster more
time to fill. Increase the between blast time on
the timer. Use a larger diameter fill line.
Sharp bends in the discharge pipe reduce force
output.
Use long radius elbows.
Discharge pipe is blocked with material.
Clean pipe and reposition it to prevent material
from entering.
Discharge pipe is too long.
Air Blaster should be as close as possible to
discharge opening.
Piston is not sealing.
Clean or replace piston and o-ring. Check valve
seat for dents, nicks, etc. The piston and valve
seat must seal.
Pressure vessel (tank) is punctured or cracked.
Replace pressure vessel.
Air Blaster is firing into an area void of material.
Air Blaster discharge should be above the
blockage of material to blast through the
blockage.