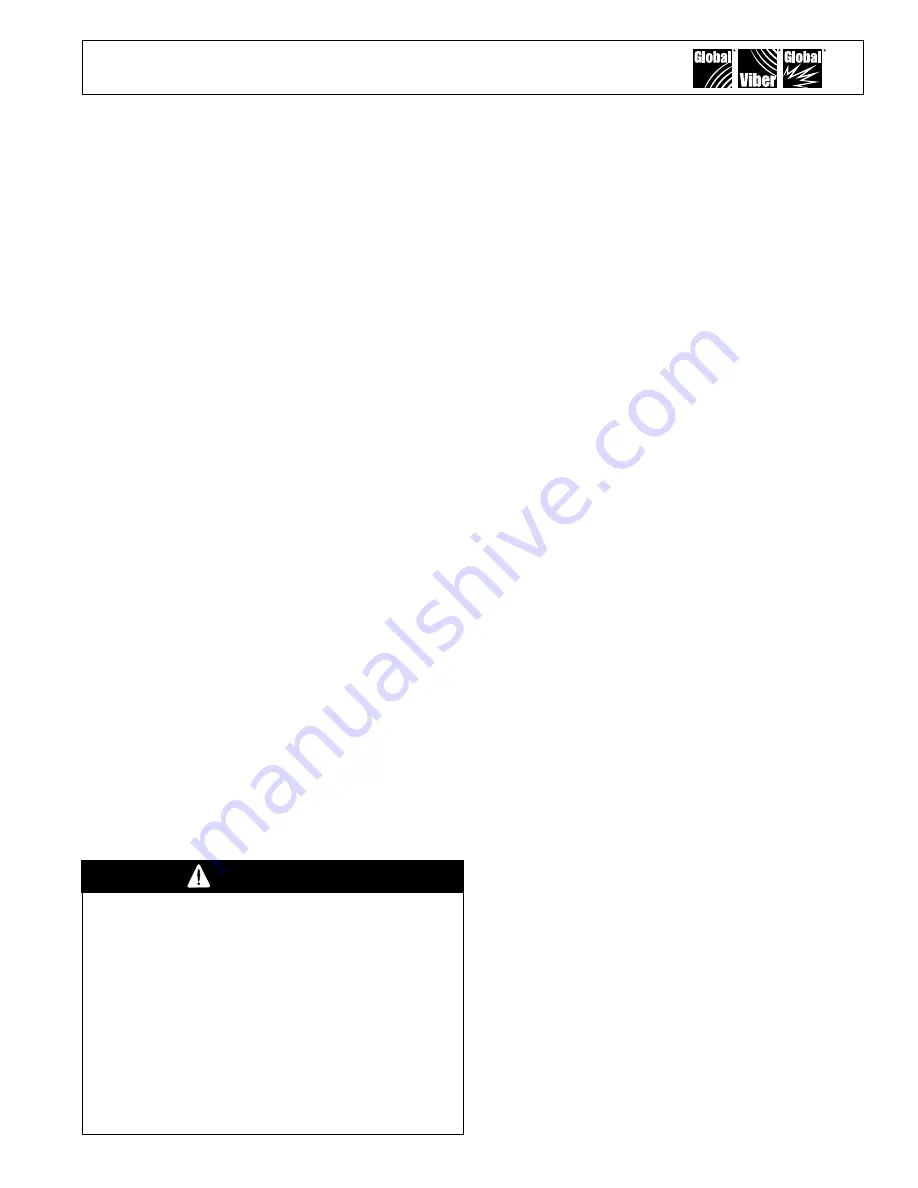
7
Global Manufacturing, Inc
®
800.551.3569
TOLL FREE USA & CANADA
1801 East 22nd Street
501.374.7416
TEL
501.376.7147
FAX
Little Rock, AR 72206 USA
w w w. G l o b a l M a n u f a c t u r i n g . c o m
3.
Airline Check Valve:
The airline check valve
prevents accidental firing of the Air Blaster due to
pressure loss in the main supply line. If the main
airline loses pressure, the check valve maintains
pressure to the Air Blaster by preventing backward
air flow. Use one check valve for every Air Blaster,
and install it between the FRG and the 3-way control
valve. A ½" or larger check valve is recommended
for all Air Blaster models.
4.
3-Way Control Valve:
The 3-way control
valve controls the firing of the Air Blaster. When in
the open position, the Air Blaster is filled with air
and maintained in the standby, ready-to-fire mode.
When closed, the Air Blaster is discharged. A ¾"
valve can be used and located up to 100 feet from
any GWE series Air Blaster since these models come
with the recommended quick exhaust valve installed
at the factory. For manual firing only, use a manual
valve. For automatic firing, use a solenoid valve.
5.
Quick Exhaust Valve:
GWE series Air
Blasters have optimum performance because they
have a quick exhaust valve (QEV) mounted at the
Air Blaster pressure vessel air inlet port. This valve
ensures the rapid depressurization of the Air Blaster
valve necessary to fire the Air Blaster and produce
maximum blast force. This QEV allows the 3-way
normally open valve (manual or solenoid) to be
placed up to 100 feet from the Air Blaster without
any substantial loss of blast performance.
Test Firing the Air Blaster:
Before mounting the Air Blaster to the discharge
pipe for the first time (or before remounting after
servicing the Air Blaster valve), do a test firing.
During tests, place the Air Blaster on its side with
the end opposite the discharge opening adequately
supported to withstand the recoil that occurs when
the Air Blaster is fired. The pressure relief valve
must be in place. See page 23.
Because of the hazards associated with the
force of the blast and the recoil, do not fill the
Air Blaster pressure vessel beyond 60 psi (4.1
bar) for testing purposes. Minimum pressure for
testing is 45 psi (3.1 bar).
Warn Personnel in the testing area to stay way
from the Air Blaster discharge outlet. The air
blast can cause serious injury.
Wear eye and ear protection. Air Blasters
produce a very loud noise when discharged
in open space.
III. Installation
Preparation and Background:
Air Blaster Placement:
To be sure Air Blasters
provide the greatest effect, it is important to properly
locate them on the storage structure. The placement
and quantity of Air Blasters depends on several
factors.
6.
Shape of the storage structure:
In
general, square structures require more Air Blasters
than round structures because materials tend to
hang up in the corners. Be sure the Air Blasters
will reach all major problem areas such as corners
and the base of any known or suspected areas of
bridging, arching, rat holing, or clinging.
7.
The degree of material flow desired:
If
Air Blasters are used to constantly move or aerate
the material, or if the sides of the storage structure
must be kept very clean, more Air Blasters will be
needed than if they are only used to restore material
flow after a stoppage.
8.
Properties of the bulk material:
Each
Air Blaster has an approximate "area of influence"
which varies with the properties of the bulk material.
As a rule of thumb, for Air Blaster applications,
bulk materials are grouped into the two categories
described as Type I or Type II Material. See table
on next page.
9.
Additional Guidelines:
If the discharge pipe
will be longer than 6 feet (1.8 meters) in length, it
is recommended that the next larger size Air Blaster
be used.
WARNING!