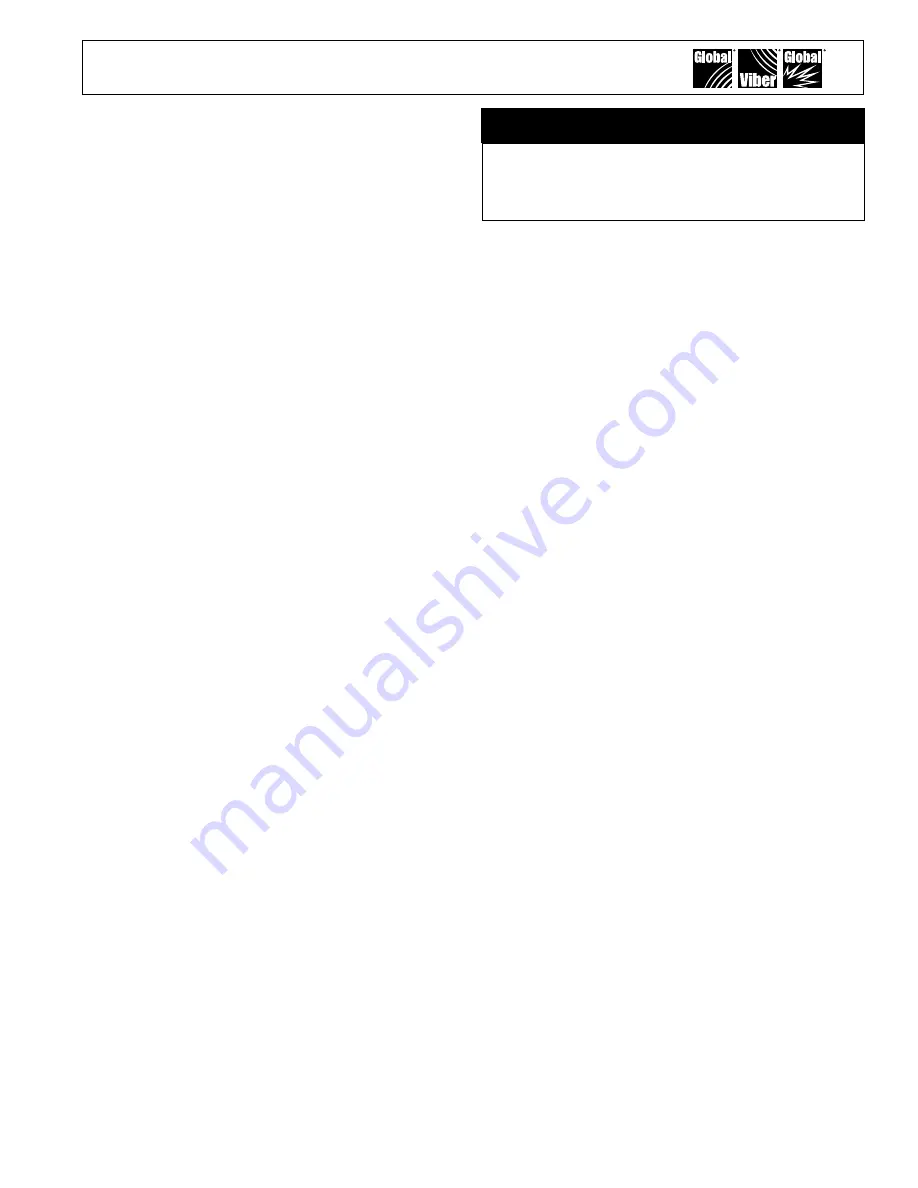
19
Global Manufacturing, Inc
®
800.551.3569
TOLL FREE USA & CANADA
1801 East 22nd Street
501.374.7416
TEL
501.376.7147
FAX
Little Rock, AR 72206 USA
w w w. G l o b a l M a n u f a c t u r i n g . c o m
IV.
Air Blaster Start - Up Procedures
1. Make sure all connections for Air Blasters,
discharge assemblies, and air and electrical
components are secure.
2. Check all 3-Way Control Valves to ensure they
are in the open position.
3. Set Filter-Regulator-Gauge (FRG) to minimum
pressure position.
4. Open the Shut-off Ball Valve to allow plant air to
enter the system.
5. Set the FRG to the pressure desired for charging
the Air Blasters: Minimum pressure = 40 psi (2.7
bar). Solenoid valves might not operate consistently
at lower pressures. Maximum pressure = 125
psi (8.6 bar). The Air Blaster tank is rated for
125 psi. Its safety relief valve will release and
depressurize the tank if the pressure exceeds 125 psi.
Pressure between 80 and 100 psi will give excellent
performance for most applications.
6. Check all airline pipe connections for leaks. Mark
all leaks found and de-pressurize the system by
closing the 2-Way Shut-off Ball Valve, and fire Air
Blaster or use pressure relief valve to depressurize
system.
7. Repair any leaks found in Step 6 and return to
Step 3. If no leaks were found, continue with Step 8.
8. Test each Air Blaster separately. For manual
control valves, simply move the lever to the closed
position to fire the Air Blaster. Return the lever to
the open position to refill the Air Blaster. If solenoid
control valves are used, activate the solenoid by
pressing the remote switch or by pressing the
appropriate timer switch while the timer is in
manual mode. Refer to the Troubleshooting Guide,
in Appendix A, if the Air Blaster does not fire or has
inadequate force.
9. If the Air Blaster System is to be controlled by
a micro-controller based sequencing timer, such as
the Global Blaster Master Timer, refer to the timer
instruction manual to configure the timer for Air
Blaster firing sequence, time between blasts, and
time between cycles. Test the timer configuration and
adjust as necessary to obtain the desired results.
10. After satisfactory completion of the above Steps,
your Global Manufacturing Air Blaster system is
ready for use.
To keep contaminants from entering the valve, Air
Blasters must be pressurized prior to operating
any material flow system.
V. Maintenance
Preventive maintenance is important to ensure
effective and safe performance of the Air Blaster
system.
Lubrication:
No lubrication required.
Air Control Accessories:
Check periodically to
make sure all valves are clean and functional. The
reservoir on the Filter-Regulator-Gauge should be
drained daily. Clean unit and filter with warm water
and mild soap as needed. Blow with compressed
air to dry. Use a 40 micron filter when the filter
element needs replacing.
Air Blaster Mounting:
All mounts must remain
rigid. Check periodically and retighten as necessary.
Replace any damaged or rusted parts.
Air Blaster Internal Valve:
The Air Blaster valve
is designed to provide many years of maintenance
free operation. Should the Air Blaster malfunction
or performance appear to decrease, inspect the
internal valve for wear or contamination. If the Air
Blaster is used in a harsh environment, inspect Air
Blasters in the system periodically - semi-annually
or annually - during routine plant maintenance
periods. This rotating inspection schedule should
indicate if the Air Blasters are showing any signs
of wear or contamination that will need attention.
Follow the instructions in section VI Disassembly
and Assembly of the Air Blaster.
Spare Parts Recommendations:
See System
Spare Parts Recommendations in Appendix C. If the
Air Blaster is not used in a harsh environment, an
inventory of spare parts may not be needed.
Important!