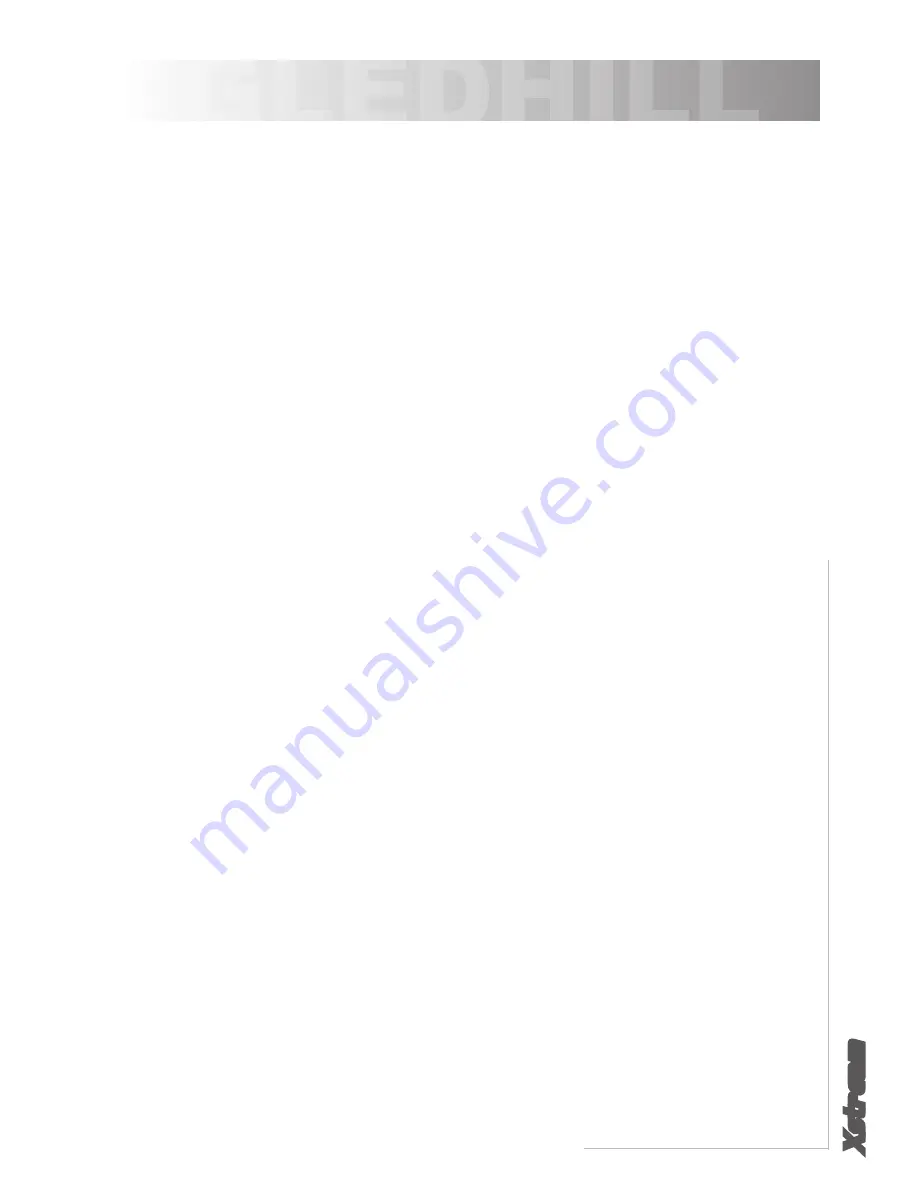
COMMISSIONING
Connections can come loose in transit, and all should be checked before installation.
Ensure that the immersion heater setting is 60ºC and that the wiring is in accordance
with the diagram on page 11.
Check the pressure on the air side of the expansion vessel. This must be done when
the volume in the cylinders is cold.
Check that the drain cock is closed, and open all the cold and hot water taps and other
terminal fittings. Allow the system to fill with water, and to run until there is no air left
in the system. Close the taps and inspect the system closely for leaks.
Manually open the Relief Valves one by one and check that water is discharged and
run freely through the tundish and out at the discharge point. The pipework should
accept full bore discharge without overflowing at the tundish, and the valve should
seat satisfactorily.
Allow the cylinder to heat to normal working temperature, then thoroughly flush the
domestic hot and cold water pipework through each tap.
If it is necessary to drain the cylinder switch off the boiler/immersion heater, open
the nearest hot tap and run all hot water until cold. Then close the stop tap and
open all hot taps in the system. AT THE SAME TIME HOLD OPEN THE PRESSURE
AND TEMPERATURE RELIEF VALVE UNTIL WATER STOPS DISCHARGING INTO
THE TUNDISH. OPEN THE DRAIN COCK AND IMMEDIATELY HOLD OPEN THE
P & T RELIEF VALVE AGAIN. THIS MUST BE HELD OPEN UNTIL THE CYLINDER IS
COMPLETELY DRAINED.
Remove the filter from the combination inlet group clean and replace refill the system
and open all hot taps until there is no air in the pipe work. ENSURE CYLINDER IS
DRAINED PRIOR TO CHECKING OR REMOVING FILTER FROM THE COMBINATION INLET
GROUP.
Allow the cylinder to heat to normal working temperature with whatever heat source
is to be used, and check again for leaks. The Pressure Relief Valve should not operate
during the heating cycle.
The boiler/heating systems should be filled and commissioned in accordance with good
practice following the guidance in BS 5449/the boiler manufacturers instructions.
NOTE: This appliance is covered by BENCHMARK and the log book must be completed
after commissioning and after every maintenance/service visit.
DON’T place any clothing or other combustible materials against or on top of this
appliance..
MAINTENANCE
The Registered Installer is responsible for the
safe installation and operation of the system.
The installer must also make his customer
aware that periodic checks of the equipment
are essential for safety.
Maintenance and inspection periods will vary
for many reasons. Gledhill Building Products
Ltd recommend a maximum of 12 months
between inspections to coincide with boiler
maintenance. Experience of local water
conditions may indicate that more frequent
inspection is desirable, eg, when water is
particularly hard, scale-forming or where the
water supply contains a high proportion of
solids, eg, sand. Maintenance will include the
following:
1. Check and clean filter
2. Manually check the operation of the
temperature relief valve.
3. Manually check the operation of the
expansion relief valve.
4. Check discharge pipes from temperature
and expansion relief valves are free from
obstruction and blockage and are not
passing any water.
5. Descale heat exchangers in hard water
areas (if required).
6. Check that water pressure downstream
of pressure reducing valve is within the
manufacturers limits.
7. Check operation of motorised valve.
8. Check the pressure on the air side of the
expansion vessel. This must be done when
the volume in the cylinders is cold.
Page 15
COMMISSIONING
Xs
tr
eam