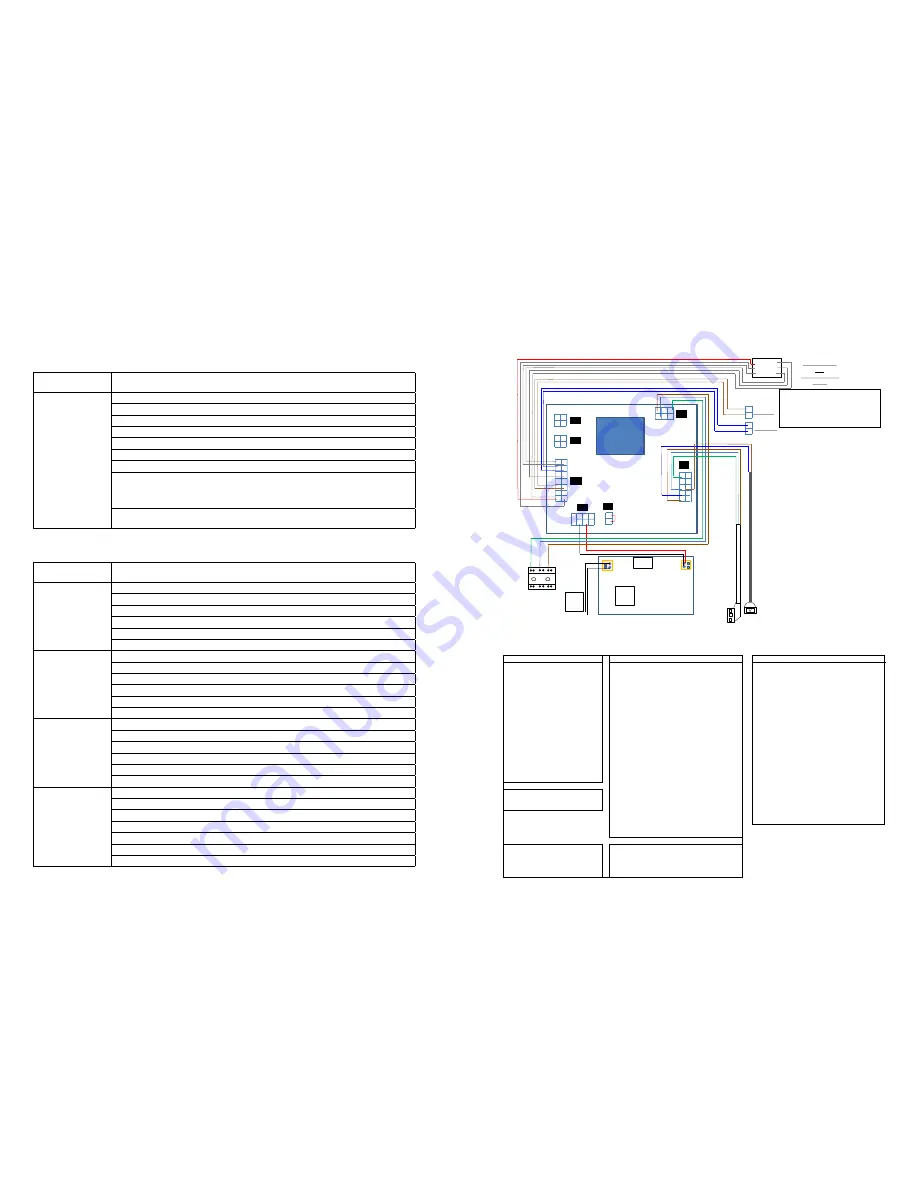
Page 34
Page 35
SERVICING AND MAINTENANCE
SERVICING AND MAINTENANCE
FAULT FINDING
FAULT FINDING
Electrical power connections
Check inputs to the PWM Controller PCB
Reference schematic
opposite
Check procedure
Power supply to PWM
Controller PCB
Electrically isolate power supply at fused spur switch and remove fuse.
Earth continuity test (dead test) – to ensure that the appliance is earthed
Mains voltage test (dead test) - to ensure that the appliance is isolated
Resistance to earth (dead test) – to ensure that the wiring insulation to the product is intact
Short circuit test (dead test) – to ensure that no components in the products circuit have a short circuit
Visually inspect wiring is correct as per fig 4.3
Connect supply
Polarity test (live test) - to ensure that the live is connecter to the live etc
• Check 230V ac across L1 to Earth
• Check 230V ac across L1 to N
• Check for 0 to 15V ac N to earth
Reference to “Boilerfault finder.com” gives clear instructions to on how to perform these tests. (Menu
options 1st. Boiler Fault finder 2nd. Electrical safety checks).
Reference schematic
opposite
Check procedure
CW temperature sensor
Power off
Disconnect J18
Measure and record the resistance across terminals 6 and 13
Measure the cold water inlet temperature
Compare the resistance measured with chart “Tasseron NTC 12k thermistor”
The reading should make sense taking measurement conditions into consideration
TS temperature sensor
Power off
Disconnect J18
Measure and record the resistance across terminals 3 and 10
Measure the thermal store temperature
Compare the resistance measured with chart “Tasseron NTC 12k thermistor”
The reading should make sense taking measurement conditions into consideration
HW temperature sensor
Power off
Disconnect J18
Measure and record the resistance across terminals 7 and 14
Measure the Hot water temperature
Compare the resistance measured with chart “HUBA combined flow sensor and NTC 10k thermistor”
The reading should make sense taking measurement conditions into consideration
Flow sensor
Power off
Disconnect J18
Power on Sensor required a power supply 5 VDC
Open a HW tap and set to a flow rate.
Measure and record the frequency across terminals 1 and 12
Compare the frequency measured with chart “flow rate determination”
The reading should make sense taking measurement conditions into consideration
1
2
3
4
5
6
7
8
9
10
11
12
13
14
1
2
3
4
1
2
3
4
1
2
3
4
5
6
7
8
1
2
1
2
3
4
5
6
7
8
9
1
10
2 3
4 5 6
J18
J20
J19
J3
J7
J8
J1
TS sensor
GND GND
IN OUT
T1 T2
1
2
CW sensor
1
2
Combined flow
and
HW temperature
sensor
L - Brown
PR61
E – G/Y
N - Blue
PW
M
-
PW
M
+
SP
ARE
Fuse
Dip
Sw
itc
h
1 2 3 4
To
DHW
pipe
All the these sensor inputs carry a
Voltage of 5V.
The max cable length is 1 meter.
The sensors connected to the control
Should be free from the appliance earth
Resistance
Resistance
Ohm
°C
±°C
Ohm
°C
±°C
309396
-40
1.7
334275
-36
0.9
171840
-30
1.7
47369
-6
0.1
98932
-20
1.6
26023
5
0.1
58879
-10
1.5
11000
23
0.6
36129
0
1.4
10500
24
0.6
22804
10
1.4
10000
25
0.6
14773
20
1.3
9500
26
0.7
12000
25
1.2
9000
27
0.7
9804
30
1.2
8500
29
1.4
6652
40
1.1
8000
30
1.5
4607
50
1
7500
31
1.6
3252
60
0.9
7000
33
1.7
2337
70
1.1
6500
35
1.7
1707
80
1.3
6000
37
1.8
1266
90
1.5
5500
39
1.9
952
100
1.8
5000
41
2.1
4500
44
2.2
4000
47
2.3
3500
50
2.5
3000
54
2.7
2500
59
2.9
2000
65
3.3
1500
73
3.7
1000
86
4.3
R-nominal
R-nominal
B-value
B-value
R-Tolerance
R-Tolerance
Tmin
Tmin
Tmax
Tmax
125°C
under 25°C±0.025*T °C over 25°C±0.05*T °C
Huba combined flow sensor and NTC 10k thermistor
Tasseron NTC 12k thermistor
12Kohm @25°C
B3740K
3%@60°C
150°C
Temperature
Temperature
-40°C
-40°C
Used on the store temperature sensors and the
cold water inlet temperature sensors
12Kohm @25°C
B4050K
Flow volume determination
(Full range 1.8 to 32.0 l/min, restricted to 26. 5 l/min)
HZ
L/min HZ
L/min HZ L/min
25 1.9 125 10.4 225 18.8
30 2.3 130 10.8 230 19.2
35 2.8 135 11.2 235 19.7
40 3.2 140 11.6 240 20.1
45 3.6 145 12.1 245 20.5
50 4.0 150 12.5 250 20.9
55 4.4 155 12.9 255 21.3
60 4.9 160 13.3 260 21.8
65 5.3 165 13.7 265 22.2
70 5.7 170 14.2 270 22.6
75 6.1 175 14.6 275 23.0
80 6.6 180 15.0 280 23.5
85 7.0 185 15.4 285 23.9
90 7.4 190 15.9 290 24.3
95 7.8 195 16.3 295 24.7
100 8.3 200 16.7 300 25.2
105 8.7 205 17.1 305 25.6
110 9.1 210 17.5 310 26.0
115 9.5 215 18.0 315 26.4
120 9.9 220 18.4 320 26.8
Summary of Contents for Torrent Stainless OV
Page 22: ...Page 42 Page 43 NOTES NOTES ...