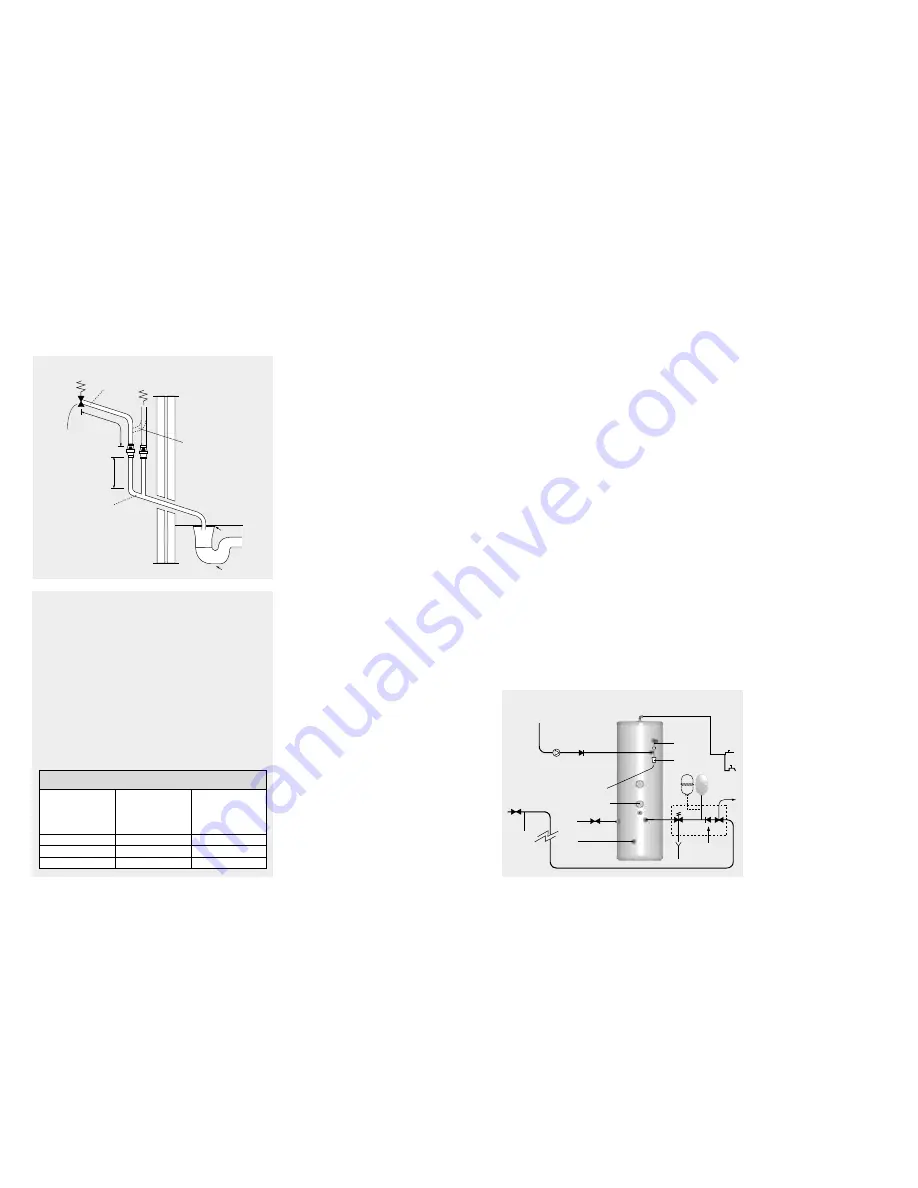
Page 14
Page 15
15 mm
discharge
pipe
Expansion
relief valve
Typical Discharge Pipe Arrangement
Dotted line showing
alternative route with
single tundish being used
600 mm max.
P & T
Relief
Valve
300 mm
min.
22 mm metal pipe with continuous
fall up to 9m equivalent length (D2).
NOTES:
The discharge will consist of scalding
water and steam. Asphalt, roofing felt
and non-metallic rainwater goods may
be damaged by such discharges.
It is not acceptable to discharge straight
into a soil pipe.
Discharge below
fixed grating
Fixed Grating
Trapped gully
Pressure & Temperature/expansion Relief
Valve Pipework
The relief valve should be installed to discharge
in accordance with G3 of the Approved
Document of the Building Regulations and
should be piped to where it is visible, but will
not cause danger to persons or damage to
materials.
The following information is taken from
Approved Document G3 of the Building
Regulations and is provided to assist with
the design and installation of the discharge
pipework. However, the information is not
exhaustive and reference should always be
made to Approved Document G3 of the Building
Regulations. The final decision regarding any
arrangements rests with Building Control and
it is recommended that their advice is sought
if you have any concerns regarding this aspect
of the installation.
The two safety valves will only discharge
water under fault conditions. When operating
normally water will not be discharged.
The tundish should be vertical, located in the
same space as the unvented hot water storage
system and be fitted as close as possible and
within 600mm of the safety device e.g. the
temperature relief valve.
The discharge pipe (D2) from the tundish should
terminate in a safe place where there is no risk
to persons in the vicinity of the discharge, be
of metal and:
a) Be at least one pipe size larger than the
nominal outlet size of the safety device unless
its total equivalent hydraulic resistance
exceeds that of a straight pipe 9m long
i.e. discharge pipes between 9m and 18m
equivalent resistance length should be at
least two sizes larger than the nominal outlet
size of the safety device, between 18 and
27m at least 3 sizes larger, and so on. Bends
must be taken into account in calculating
the flow resistance. Refer to the table and
the worked example.
An alternative approach for sizing discharge
pipes would be to follow BS EN 806-2:2005
Specification for design installation, testing
and maintenance of services supplying water
for domestic use within buildings and their
curtilages.
b) Have a vertical section of pipe at least
300mm long, below the tundish before any
elbows or bends in the pipe work.
c) Be installed with a continuous fall.
d) It is preferable for the discharge to be visible at both the tundish and the final point
of discharge but where this is not possible or practically difficult there should be
clear visibility at one or other of these locations. Examples of acceptable discharge
arrangements are:
1. Ideally below the fixed grating and above the water seal in a trapped gulley.
2. Downward discharges at a low level; i.e. up to 100mm above external surfaces
such as car parks, hard standings, grassed areas etc are acceptable providing that
where children play or otherwise come into contact with discharges, a wire cage
or similar guard is positioned to prevent contact whilst maintaining visibility.
3. Discharges at a high level; e.g. into metal hopper and metal down pipe with the
end of the discharge pipe clearly visible (tundish visible or not) or onto a roof
capable of withstanding high temperature discharges of water and 3m from
any plastic guttering systems that would collect such discharges.
4. Where a single common discharge pipe serves more than one system, it should
be at least one pipe size larger than the largest individual discharge pipe (D2)
to be connected.
5. If unvented hot water storage systems are installed where discharges form
safety devices may not be apparent i.e. in dwellings occupied by blind, infirm
or disabled people, consideration should be given to the installation of an
electronically operated device to warn when discharge takes place.
Safety
The safety devices supplied or fitted on an StainlessLite Plus are selected for their
suitability for the temperatures and pressures involved. They must not be changed,
removed or by-passed and it is essential that only genuine replacement parts supplied
or approved by Gledhill Building Products Limited are used. All parts are available to
approved installers from Gledhill Building Products Limited, Sycamore Estate, Squires
Gate, Blackpool (Telephone 01253 474402).
Tundish
Hot Outlet
To Drain
PRV
NRV
Stop
Tap
Kitchen
Cold
Tap
Combination
Valve
Balanced
Cold
Outlets
P&T
Relief Valve
Immersion Heater
Expansion Vessel(s)
Boiler
Return
Boiler
Flow
2 Port Valve
Secondary
Return Circuit
Schematic Diagram
Non Return
Valve
Pump
ERV
Worked Example
The example below is for G1/2 temperature relief valve with a discharge pipe (D2)
having 4 elbows and length of 7m from the tundish to the point of discharge.
From the table below:
Maximum resistance allowed for a straight length of 22mm copper discharge
pipe (D2) from a G1/2 temperature relief valve is: 9m subtract the resistance for
4 x 22mm elbows at 0.8m each = 3.2m.
Therefore the maximum permitted length equates to: 5.8m.
5.8m is less than the actual length of 7m therefore calculate the next largest size.
Maximum resistance allowed for a straight length of 28mm pipe (D2) from a G1/2
temperature relief valve equates to: 14m.
As the actual length is 7m, a 28mm (D2) copper pipe will be satisfactory.
Sizing of copper discharge pipe ‘D2’ for a temperature relief valve
with a G1/2 outlet size (as supplied)
Size of discharge
pipework
Maximum length of
straight pipe
(no bends or elbows)
Deduct the figure
below from the
maximum length for
each bend or elbow in
the discharge pipe
22mm
Up to 9m
0.8m
28mm
Up to 18m
1m
35mm
Up to 27m
1.4m
INSTALLATION
INSTALLATION
INSTALLATION
INSTALLATION
Line Strainer
This is integral within the combination inlet
group to reduce the likelihood of contaminants
fouling the valve seat. Following installation this
line strainer must be cleaned and replaced. This
needs to be carried out on a regular basis. as part
of the annual maintenance/service check.
Tundish
This is to allow the discharge from any Relief
Valve to be seen. It must be fitted away from
any electrical devices. See page 14 for discharge
pipework details.
Expansion Vessels Installation
To prevent water stagnation and particulate
accumulation affecting water quality, it is
recommended that the expansion vessel be
installed in the vertical orientation so that the
fitting accommodating thermal expansion or a
pressure surge is:-
1. bottom fed and upright; and
2. that the connecting pipework to the fitting:-
- rises continuously; and
- is kept to a minimum;
2 expansion cylinders on 400 litre Models
All 400 litre models are supplied with two 24
litre expansion cylinders. These can be coupled
together and fitted to the expansion cylinder
tapping on the combination inlet valve, or by
some other means on the cold/hot water inlet
pipework. There must be no valve on the pipe
work between the expansion cylinders and the
unvented cylinder which could prevent the
expansion of the water contained in the unvented
cylinder reaching the expansion cylinders.
Combination Inlet Group
Combines elements 1, 2 and 3 below.
1.
Pressure Reducing Valve
- The cold water
supply to any mixer taps/showers must
be taken from the cold water tapping of
this valve to ensure balanced hot and cold
pressures. This valve is factory set to ensure
the correct operating pressure for the
StainlessLite Plus.
2.
Non Return Valve
- This is integral with the
pressure reducing valve to prevent backflow of
hot water towards cold water draw off points.
3.
Cold Water Expansion Relief Valve
- This safety
device is preset at the factory and will relieve
excess cold water pressure resulting from a
fault condition.