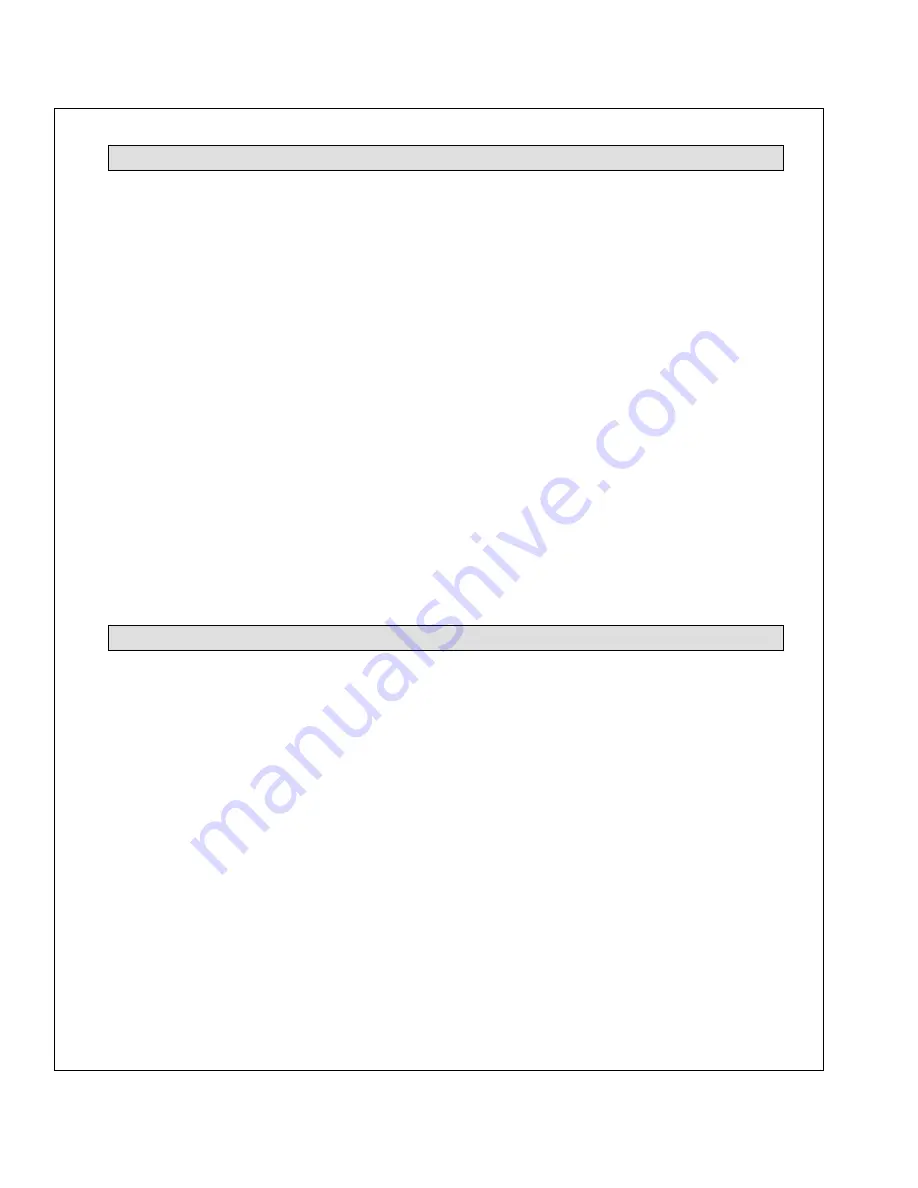
14
12.3.1 Double Acting PID CONTROL (#
5,6,7,8
):
All the parameters referring to PID control are listed in the group “rEg”. The double
action PID control is used to control processes where there is an element which causes a
positive increase in temperature (ex. Heating) and an element which causes a decrease
in temperature (cooling). This type of control is selected by setting “cont” as Pid setting.
At least two outputs as “coP” with oPcF parameter representing which output acts on
heater and which acts on cooler. The effective set Point “sP” and the instruments
algorithm decides the controller output of Double Action PID control. The cycle times
“hct” (Heat cycle time: for output acting on heater) and “cct” (Cool cycle time: for
output acting on cooler) should have low value with frequent intervention of control
outputs so that good stability of process variable can be achieved, in case of fast
processes. It is recommended to use solid state relays to drive actuators. The Double
Action PID control algorithm needs the programming of following parameters:
"Pb” - Proportional Band
"hct" – Heat cycle time
"cct” – Cool cycle time
"Int" - Integral Time
"dEr" - derivative time
"rs" - Manual Reset (if "Int=0 only)
"coEF" – Coefficient Relation between power heating and cooling element. Range
between 0.1 to 10.
"coEf" < 1: represents that the cooling element is stronger than heating element.
“coEf” = 1: represents that the heating and cooling element are equally strong.
“coEf” > 1: represents that the heating element is stronger than cooling element.
13.0 AUTO TUNING:
Auto tuning is a process by which the controller automatically calculates the values of
dp, Int and dEr, suitable for the process. In this process, the controller carries out
several opertions on the process plant to determine these values.
Steps for Auto-tuning are as follows:
1. Program and select desired Set Point.
2. Program Par. “cont” =pid.
3. For single action PID control, program par. “Func” as “heat” if using heater or “COOL”
if using cooler.
4. Also program the output to which the final control element is connected as “coP”.
5. In case of Double action PID control, set “coP” on the two outputs selected using par.
“oPcF” to act on heater and cooler.
6. Progarm par. “Auto” as:
“1” - Tune at Every power ON. If auto-tuning is desired, each time the instrument is
switched ON.
“2” - Tune at first power ON. If auto-tuning is desired, the next time the instrument is
switched ON. Once the tuning is finished, the par. “Auto” is swapped automatically to
“OFF”.
“3” – Tune manually. If auto-tunning is to be started manually by pressing the config
key programmed as “stAt”
4”- Tune at every set point change or at the end of soft start. This activates auto-
tuning at every change of set point or at the end of soft-start cycle.
Summary of Contents for 151A12B
Page 1: ...1 SERIES PR 69 TEMPERATURE CONTROLLER...
Page 5: ...5 5 0 DIMENSIONS in mm...
Page 43: ...43 22 CONNECTION DIAGRAMS...
Page 46: ...46...
Page 47: ...47...