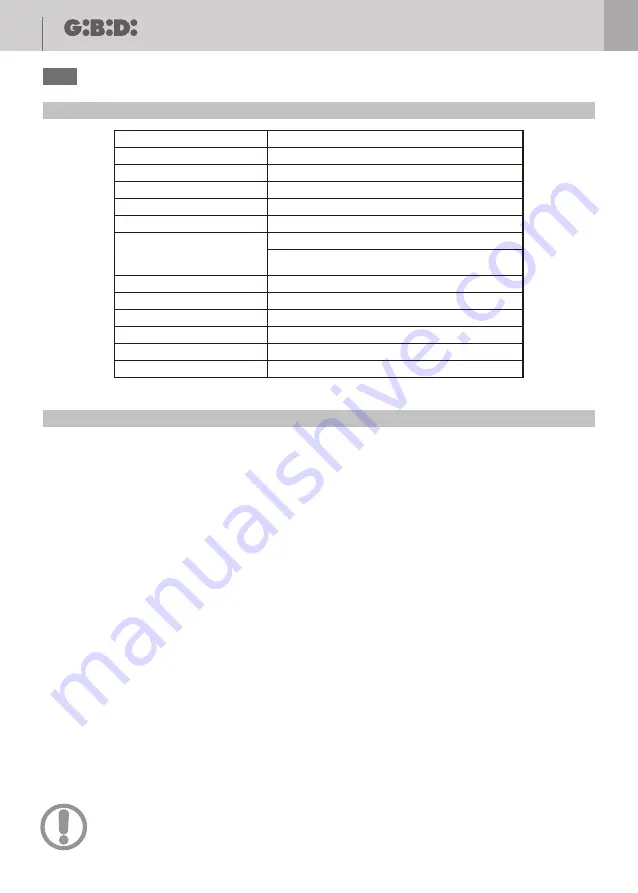
20
21
SNAPPER
SNAPPER
UK
UK
Encoder
SNAPPER 250
100 W (~1000 N)
24 Vdc
250Nm
-20°C + 60°C
IP 44
If fitted on blind/flush panel doors
it is mandatory to use an electric lock
Integrated into the motor
Intensive
10 °/s
2.5 m
250 Kg
Electric system setup
Set up the electric system as shown in
fig.1
referring to the electric system regulations and other national regulations
in force. Keep the mains power connections clearly separated from the service connections (photocells, sensitive
frames, control devices, etc.).
The main components are:
1- Antenna; screened coaxial cable
2- Electronic control unit container
3- Electric lock; 1 mm² 2-core (2x1) cable
4- Key selector; 0,5 mm² 3-core (3x0,5) cable
5- 24Vdc operators:
- 1,5 mm² 2-core (2x1,5) cable power supply WHITE = + YELLOW = -
for a cable length of 6 m max., over it’s necessary increase the cable section.
-0,5mm² 3-core (3x0,5) encoder cable.
6- Omnipolar magnetothermal and differential switch with minimum contact opening of 3 mm
220-230V/50-60Hz control unit power line: min. 1,5 mm² 3-core cable (3x1,5)
(adhere to the regulations in force)
7- 24V flashing light; 0,75 mm² 2-core (2x0,75) cable
8- Connector blocks
9- Photocell transmitter; 0,5 mm² 2-core (2x0,5) cable
10- Photocell receiver; 0,5 mm² 4-core (4x0,5) cable
A- Opening mechanical end-stop.
B- Closing mechanical end-stop.
ELECTRICAL EQUIPMENT
Supply voltage
Power absorbed
Electric motor
Max torque
Operating temperature
Frequency of use (%)
Degree of protection
Maximum leaf length
Angular velocity
Operator
Type
Irreversible electromechanical with worm screw
TECHNICAL DATA
Maximum leaf weight
CAUTION: It is important that an omnipolar magnetothermal and differential switch with a
minimum contact opening of 3 mm be fitted upstream of the control unit.
230Vac
Check that the gate structure is in conformity with the regulations in force and that the gate movement is linear
without friction.
Preliminary checks:
• Check that the gate structure is sufficiently robust.
• In any event, the actuator must push the leaf at a reinforced point.
• Manually check that the leafs move without force along their entire travel.
• If the gate is not a new installation, check the state of wear of all the components, and repair or replace the
defective or worn parts.
The reliability and safety of the automated device is directly dependent on the condition of the gate structure.
Refer to
5
for possible installation dimensions.
fig.
PRELIMINARY WARNINGS
INSTALLATION DIMENSIONS
Preliminary checks:
For proper functioning of the automated device, the existing or new gate structure must meet the following
requirements:
Ÿ
The individual leafs must have a maximum length of 2.5m
Ÿ
The leaf structure must be robust and rigid
Ÿ
The leafs must move smoothly and uniformly without irregular friction along their entire travel
Ÿ
The existing hinges must be in a good condition
fig.
fig.
Fasten the rear bracket to the pillar
fig.6a-6b
.
Fit the operator on the rear bracket using the screws provided
fig.6c
.
Fasten the arms and the front bracket on the operator
fig.6d
.
Unlock the operator (see unlocking device).
Move the leaf to closed position.
Fix the front bracket to the leaf .
Ÿ
Use a spirit level to check that the arm is perfectly level.
Ÿ
Manually open and close the gate to its full opening and closing travel. The gate must move smoothly without
friction.
Ÿ
Fix the mechanical stoppers
fig.6e-6f
.
Installing the operators
Find the most suitable point where to fasten the front bracket of the operator and mark it.
Using a spirit level mark the point on the pillar where to fasten the rear bracket .
Identify the point where to fasten the rear bracket in relation to the dimensions
A-B
5
and in relation to
2
.
Ÿ
Ÿ
Ÿ
Ÿ
Ÿ
Ÿ
Ÿ
Ÿ
Ÿ
OPERATOR INSTALLATION