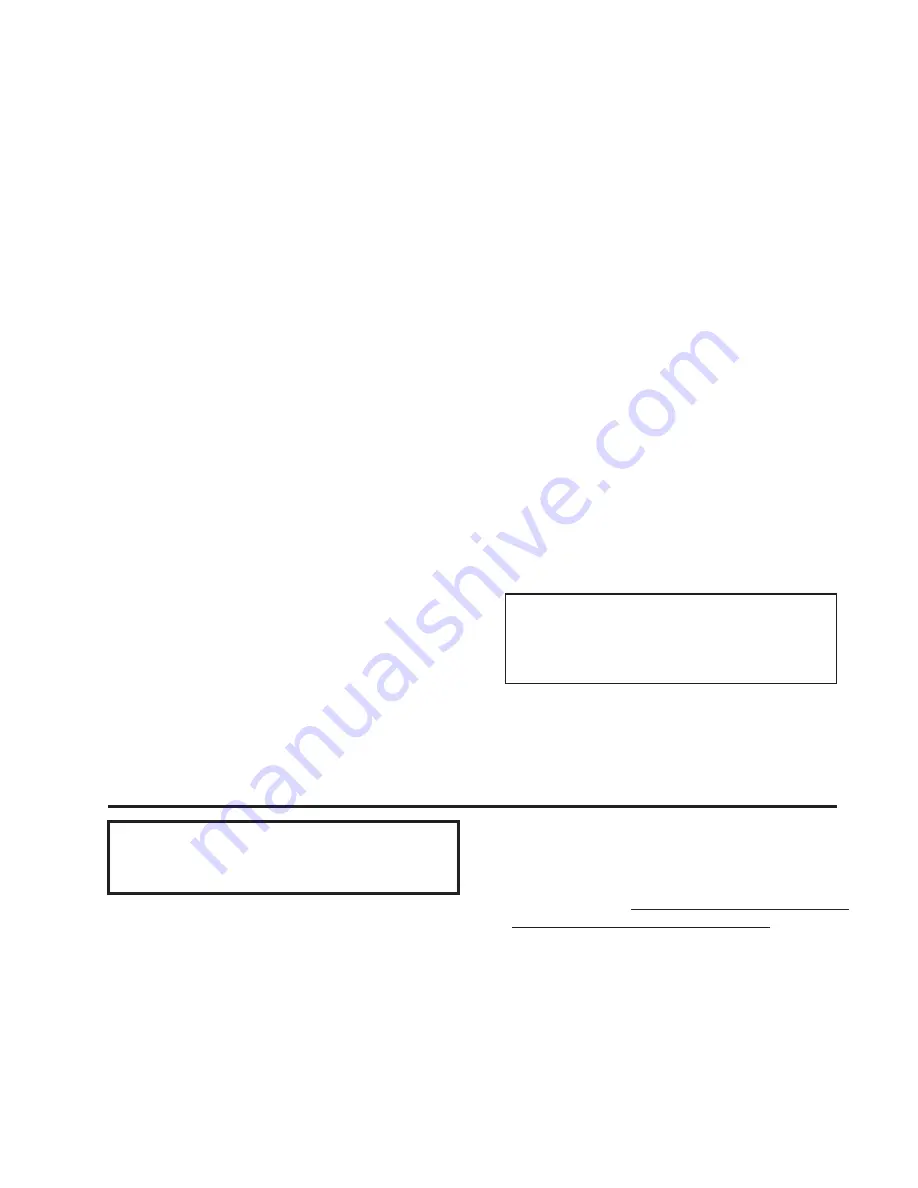
2
INSTALLATION INSTRUCTIONS
Installation of the Giant Industries, Inc., pump is
not a complicated procedure, but there are some
basic steps common to all pumps. The following
information is to be considered as a general out-
line for installation. If you have unique require-
ments, please contact Giant Industries, Inc. or
your local distributor for assistance.
1. The pump should be installed flat on a base to
a maximum of a 15 degree angle of inclination to
ensure optimum lubrication.
2. The inlet to the pump should be sized for the flow
rate of the pump with no unnecessary restrictions
that can cause cavitation. Teflon tape should be
used to seal all joints. If pumps are to be operated
at temperatures in excess of 140
0
F, it is important to
insure a positive head to the pump to prevent cavita-
tion.
3. The discharge plumbing from the pump should be
properly sized to the flow rate to prevent line pres
-
sure loss to the work area. It is essential to provide
a safety bypass valve between the pump and the
work area to protect the pump from pressure spikes
in the event of a blockage or the use of a shut-off gun.
4. Use of a dampener is necessary to minimize pul-
sation at drive elements, plumbing, connections, and
other system areas. The use of a dampener with
Giant Industries, Inc. pumps is optional, although
recommended by Giant Industries, Inc. to further
reduce system pulsation. Dampeners can also
reduce the severity of pressure spikes that occur in
systems using a shut-off gun. A dampener must be
positioned downstream from the unloader.
5. Crankshaft rotation on Giant Industries, Inc.
pumps should be made in the direction designated
by the arrows on the pump crankcase. Reverse ro-
changed immediately if condensate or frothing oil oc-
curs in the crankcase.
2. Pump operation must not exceed rated pressure,
volume, or RPM. A pressure relief device must be
installed in the discharge of the system.
3. Acids, alkalines, or abrasive fluids cannot be
pumped unless approval in writing is obtained before
operation from Giant Industries, Inc.
4.
Important!
If there is a
danger of frost,
the water
in the pump and in the pump fittings (particularly the
unloader valve) must be emptied. The second dis-
charge port can also be used and the pump run “dry”
for 1-2 mintues for thes purpose.
IMPORTANT OPERATING CONDITIONS
Failure to comply with any of these
conditions invalidates the warranty
1. Prior to initial operation, add oil to crankcase so
that the oil level is between the two lines on the oil
dipstick. DO NOT OVERFILL.
SAE 80W-90 In-
dustrial Gear Lube Oil may be used (Giant’s p/n
01154)
. Crankcase oil should be changed after the
first 50 hours of operation, then at regular intervals
of 500 hours or less depending on operating condi-
tions.
Note:
When operating in areas with high humidity
or large temperature fluctuations, the oil must be
tation may be safely achieved by following a few
guidelines available upon request from Giant
Industries, Inc. Required horsepower for system
operation can be obtained from the chart on
pages 3 & 6. When the pump is operating, the
exposed shaft side, the driven shaft side, and its
coupling must be covered by a protective guard.
The plunger area must also be covered by the
proctective plate (30) Do not step on the protec
-
tive plate (30) or put weight on it.
6. Crankshaft rotation on Giant Industries, Inc.
pumps should be made in the direction desig-
nated by the arrows on the pump crankcase.
Reverse rotation may be safely achieved by fol-
lowing a few guidelines available upon request
from Giant Industries, Inc. Required horsepower
for system operation can be obtained from the
charts on page 3.
7. Before beginning operation of your pumping
system, remember: Check that the crankcase
and seal areas have been properly lubricated
per recommended schedules. Do not run the
pump dry for extended periods of time. Cavi-
tation will result in severe damage. Always
remember to check that all plumbing valves are
open and that pumped media can flow freely to
the inlet of the pump.
Finally, remember that high pressure operation
in a pump system has many advantages. But,
if it is used carlessly and without regard to its
potential hazard, it can cause serious injury.
8. The service life of the seals is maximized
if there is a minimal amount of leakage. A few
drops of water can drip from each plunger every
minute. Leakage must be examined every day. If
the leakage becomes excessive (constant drip
-
ping), the plunger seals must be changed.