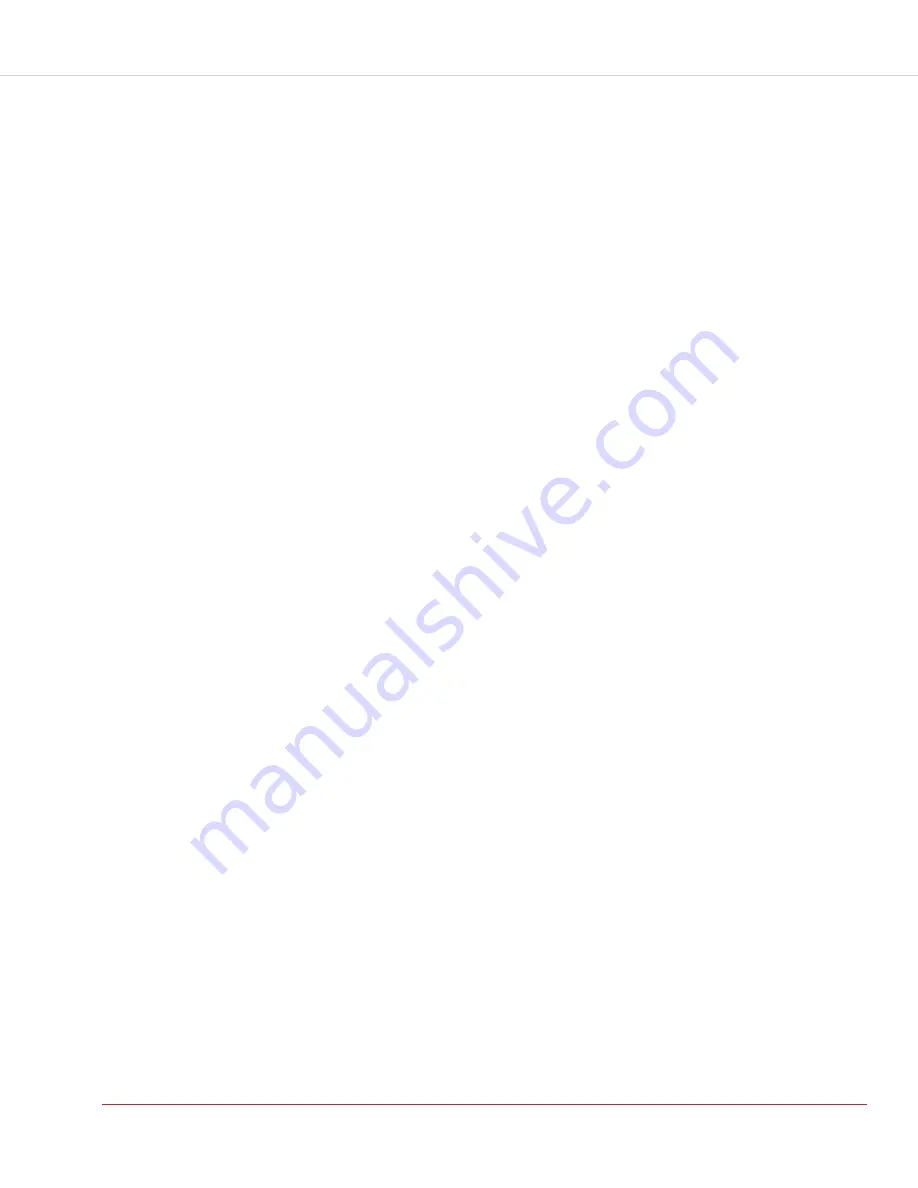
V-belt drive considerations
V-belt drives on GFS fans are purposely sized to handle considerably more load than would be necessary
for normal drive design. This is done to prolong the life of the drive and provide for minimum maintenance.
Belts should be replaced when they have obviously become worn, even though they are still operating. A
badly worn belt will also cause undue sheave wear.
Replace belts when they show definite signs of wear; otherwise the sheaves will become worn to the point
where they also must be replaced. Never put new belts on a badly worn sheave. This will reduce the
capacity of the drive and cause excessive belt wear.
Most GFS fans are provided with an adjusting screw as a part of the motor base for easy setting of belt
tension. However, small fans or fans using small horsepower motors may have only a slotted base plate.
When the belt tension is adjusted by moving a motor on a slotted base, be sure to block the motor tightly
and squarely before tightening the hold-down bolts, keeping the motor sheave in line with the belt. The
motor sheave must be parallel to and in line with the fan sheave.
When you replace belts on a multi-groove drive, be sure they are used in a matched set. If you are not sure
whether the belts are matched, observe them in operation. The tight side should be perfectly straight and
the belts should run smoothly and in line. The slack side should bow out and also be in line.
If one of the belts extends out considerably farther than another, it is an indication that the belts are not
matched and should be changed. If there is only a slight difference, the normal stretching in the first hours
of operation will equalize the belt lengths and the belts will be well matched.
Replace fan bearings (SpaceSaver)
Follow the assembly and alignment procedure when installing replacement bearings. Inspect the shaft for
wear at the bearing mounting positions. The shaft diameter should not be less than the commercial ground
and polished tolerances. Excessive undersizing results in rapid wear.
1.
Slide the bearing onto the shaft with the bearing collar pointed away from the wheel and toward the
end of the shaft. The head of the inverted socket-head capscrew fits in the short keyway. Make sure the
shaft can expand without the end of the keyway hitting the screw head.
2.
Confirm that the shaft is at the proper centerline height and the bearing is square with the shaft.
3.
Confirm that the shaft and bearings are in proper alignment.
4.
Bolt the bearing into position; then check the position of the shaft and bearing again.
Common causes of excessive vibration
• Damage in shipping and handling or poor installation may upset the unit's balance
• The support structure is not sufficiently rigid or level. Resonance in the ductwork or support structure
amplifies vibration.
• Belt tension is too tight or too loose.
• The bearing locking collar or mounting bolts are loose.
Service and maintenance
Global Finishing Solutions
41
239-062 rev 5