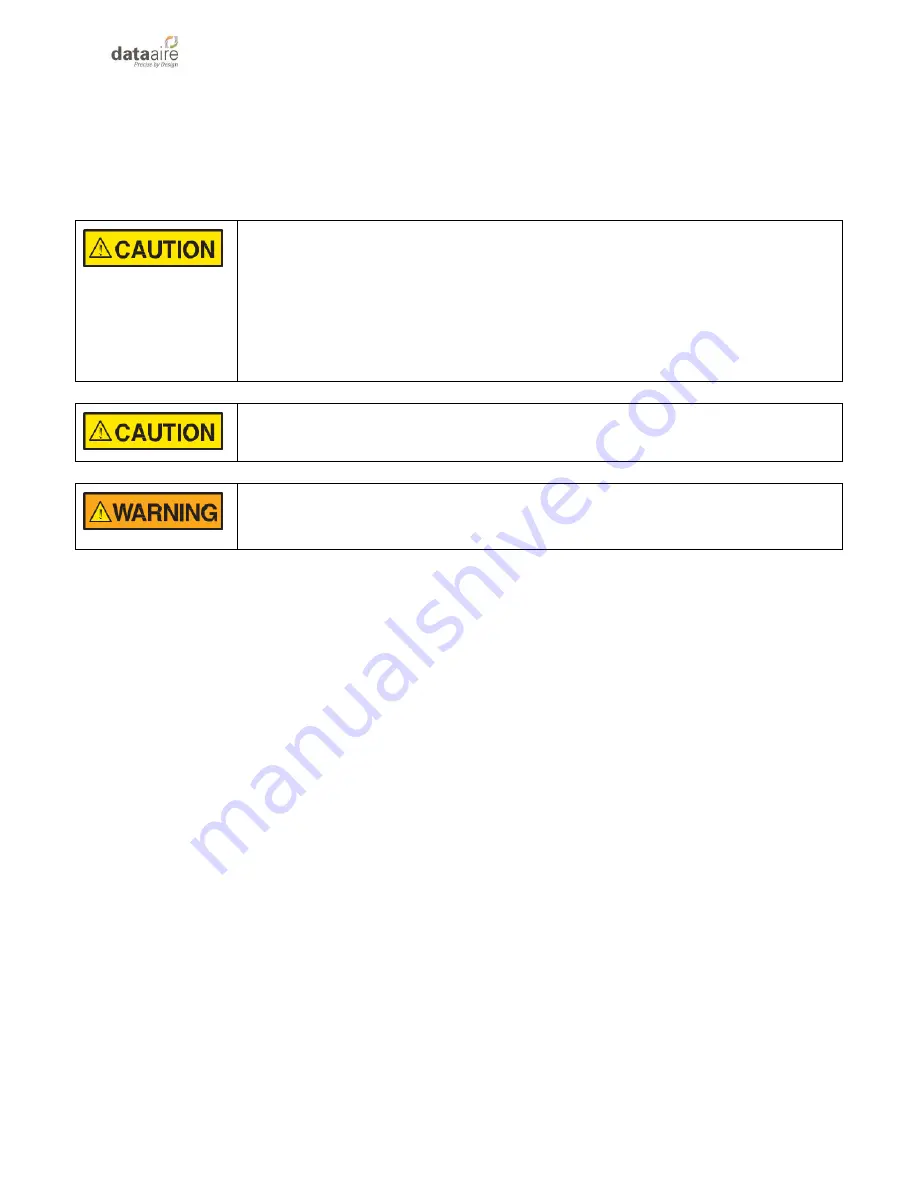
71
out on a regular basis by a suitably qualified Service Technician. It should be noted that the
interval necessary between each ‘minor’ and ‘major’ service can vary depending on, for instance,
application, site conditions
and expected operating schedule. Normally a ‘minor’ service should
be carried out ever
y three to six months and a ‘major’ service once a year. It is recommended
that Data Aire Service Department be contacted for recommendations for individual sites.
CAUTION:
Personal protective equipment is to be used for maintaining
and servicing equipment. Some operations when servicing or maintaining
the unit may require additional assistance regarding manual handling. This
requirement is down to the discretion of the Service Technician. All
maintenance and servicing must compliance with environmental and safety
regulatory requirements.
CAUTION:
Remember
do not
perform a lift that exceeds your ability.
WARNING:
Turn OFF the disconnect switch to all remote electric facility
power to the unit before servicing or maintenance.
9.5.
Air Filters
The air filter section is an integral part of the environmental control system, designed within the
unit for easy front and/or side accessibility. An initial set of filters are factory installed in the unit.
The filters are 4-inch (100 mm) deep unless otherwise specified, disposable, pleated design,
extended-surface, nonwoven, reinforced cotton fabric; supported and bonded to welded-wire
grid; enclosed in cardboard frame design rated not less than MERV 8 per ASHRAE Std. 52.2.
A filter differential switch for alarm activation is included on some units and optional on other
units. Air filters should be checked on a regular basis and changed when they become dirty.
This will ensure efficient operation of the unit. Air filters that that are not maintained and require
changing can restrict airflow and create problems such as coil icing or poor air distribution. Spare
air filters should be kept in stock as these tend to be a frequently replaced maintenance item.
Air filters may require changing as often as monthly dependent on room or space conditions.
New installations with construction dust will quickly clog filters requiring new filters.
On some units, the dap4 control panel monitors the air filters status. A dirty filter alarm will be
enunciated on the controls display screen and available as a Building Management System
(BMS) data port. Although the unit may display a dirty filter alarm, this should not be relied on
as the only determinant for replacing air filters. A misadjusted air filter differential pressure switch
may not give a proper indication of a clogged filter.
To check the air filter pressure differential pressure switch for proper adjustment, temporarily
cover approximately 75% of the return air opening using heavy cardboard or similar material.
The alarm should energize when 75% of the air is blocked, simulating dirty filters. If the alarm
energizes prematurely or does not energize at all, the pressure switch should be adjusted. All