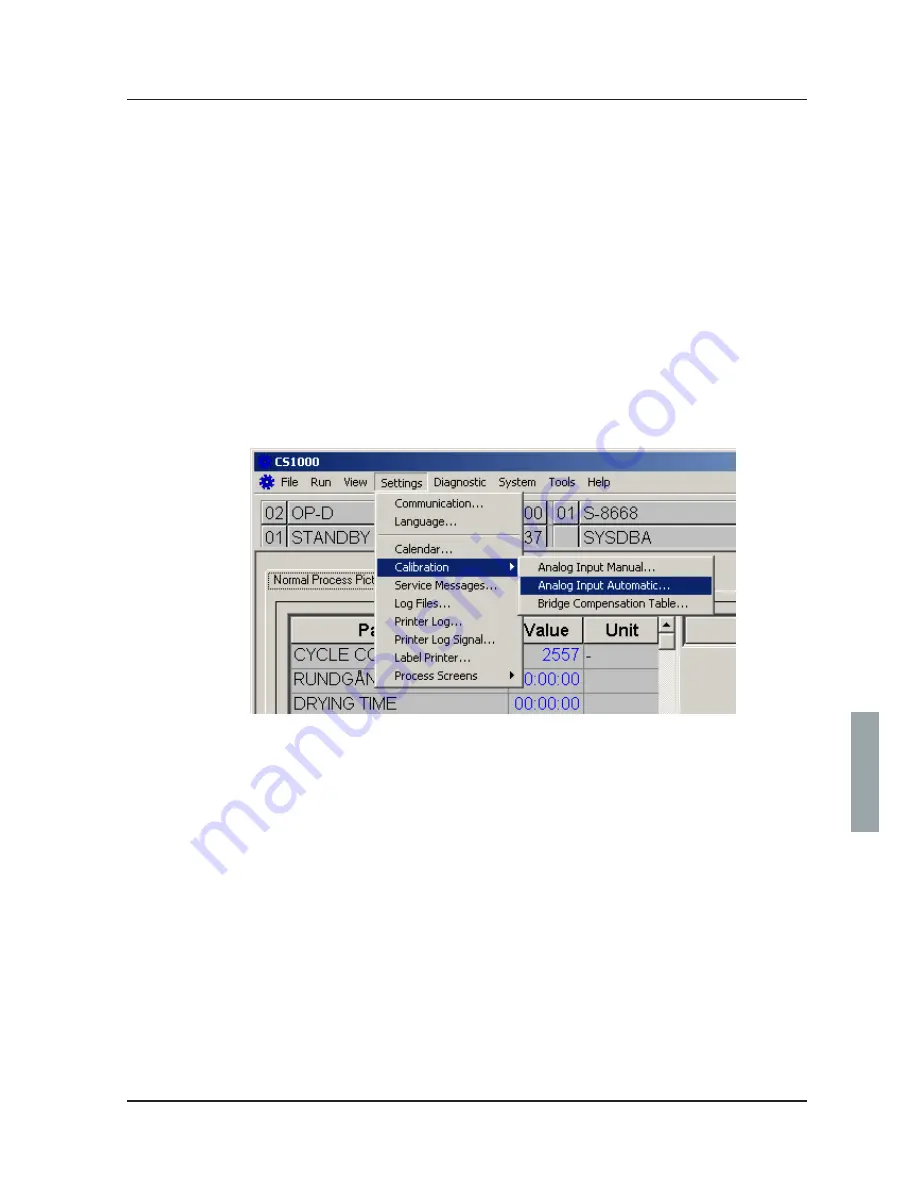
Repair and adjustment
13
Service instructions
5015108-00
Edition 0403
Calibration
To calibrate the conductivity meter, proceed as follows.
1. Connect a PC with the CS 1000 program installed to the disinfector.
2. Press
[
on the conductivity meter.
3. Enter code 22 with
Y
and
Z
.
4. Press
[
. Setup 1 appears.
5. Choose Output with
Y
and
Z
.
6. Press
[
. Sel. Type appears.
7. Choose SIM with
Y
and
Z
.
8. Press
[
.
9. Choose to 0 …22 mA with
Y
och
Z
.
10. Set 4 mA.
11. Press
[
.
12. Start CS 1000 and choose Settings/Calibration/Analog Input Automatic...
V1563
Summary of Contents for 8666
Page 1: ...SERVICE INSTRUCTIONS Washer disinfector Getinge 8666 8668 Mfg no SEV0320078 5015108 00 ...
Page 2: ......
Page 4: ......
Page 6: ...Safetyregulations 2 Serviceinstructions 5015108 00 Edition 0403 ...
Page 8: ......
Page 10: ...Technicaldata 2 Serviceinstructions 5015108 00 Edition 0403 ...
Page 12: ...Technicaldata 4 Serviceinstructions 5015108 00 Edition 0403 Alternativeconnectionarrangements ...
Page 14: ......
Page 24: ......
Page 26: ......
Page 33: ......
Page 37: ......
Page 39: ......
Page 47: ......
Page 49: ...Repairandadjustment 2 Serviceinstructions 5015108 00 Edition 0403 ...
Page 95: ......
Page 96: ......
Page 97: ......
Page 98: ......
Page 99: ......
Page 100: ......
Page 101: ......
Page 102: ......
Page 103: ......
Page 104: ......
Page 105: ......
Page 106: ......
Page 107: ......
Page 108: ......
Page 109: ......
Page 110: ......
Page 111: ......
Page 112: ......
Page 113: ......
Page 114: ......
Page 115: ......
Page 116: ......
Page 117: ......
Page 118: ......
Page 119: ......
Page 120: ......
Page 121: ......
Page 122: ......
Page 123: ......
Page 124: ......
Page 125: ......
Page 126: ......
Page 127: ......
Page 128: ......
Page 129: ......
Page 130: ......
Page 131: ......
Page 132: ......
Page 133: ......
Page 134: ......