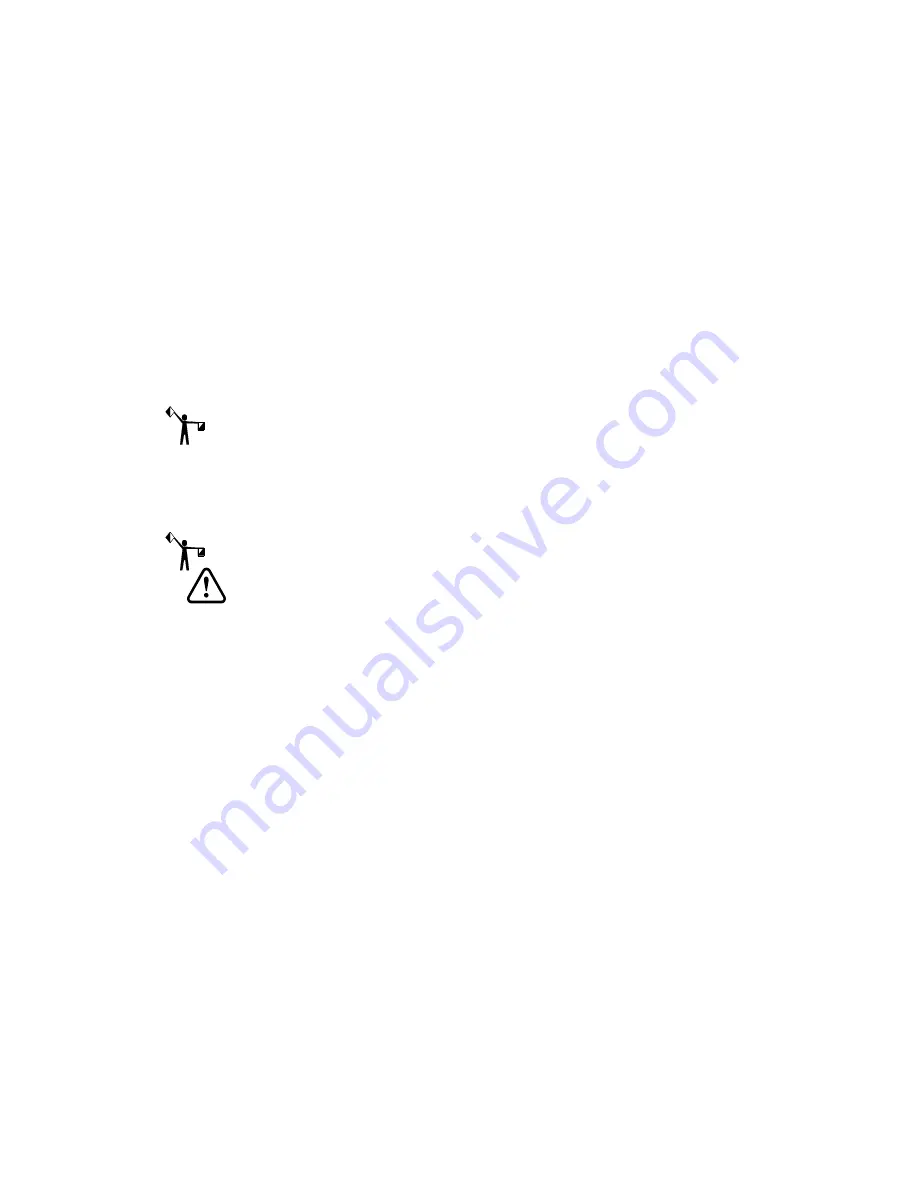
36
Chapter 9:
Maintenance
This section includes instructions for routine cleaning and lubrication, fuse
replacement, and adjustments to keep the GSx
plus
plotter in good working order.
Cleaning and Lubrication
Routine cleaning and lubrication should be done monthly or after every 160
hours of use, whichever occurs first. Isopropyl alcohol should be used to clean
dirty
parts
.
Note: When alcohol is used, lubricate the parts immediately to prevent
corrosion.
Use light oil such as 3-in-1
®
Oil for all lubrication, except as noted.
Tool Holders AND Carriage Spindle BORE
Note: The spindle bore should be cleaned daily.
CAUTION: Do not use oil to lubricate tool holders or spindle bore.
There is a very close fit between the pen, knife and pounce wheel holders and the
carriage spindle bore. Any dirt or build-up in the bore or on the tool holder
restricts motion and can produce inconsistent results.
1
Once a day clean the spindle bore and tool holders with isopropyl
alcohol using a clean, dry, lint-free cloth on the tool holders and a clean,
dry cotton swab in the bore.
2
Wipe the tool spindle with a soft, lint-free, dry cloth. Dust, hair, silicon,
and other debris can greatly affect tool performance and letter quality.
Summary of Contents for GSx Plus
Page 1: ...GSxplus USER S MANUAL...
Page 55: ......
Page 58: ...Z Z axis tool height adjustment 42...
Page 60: ......