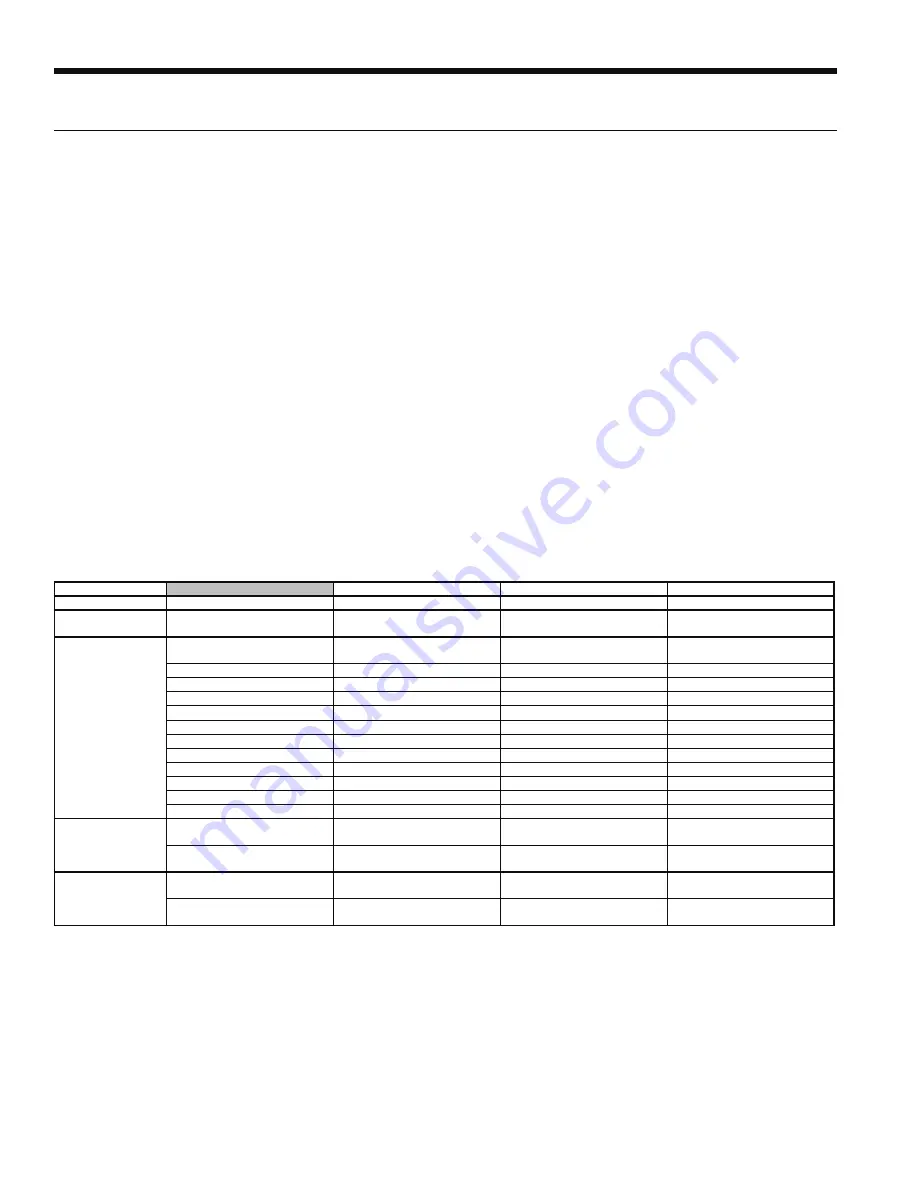
18
ASTON CONSOLE SERIES INSTALLATION MANUAL
Open Loop Ground Water Systems
Always maintain water pressure in the heat exchanger by placing water control valves at the outlet of the unit to prevent mineral
precipitation. Use a closed, bladder-type expansion tank to minimize mineral formation due to air exposure. Insure proper water flow
through the unit by checking pressure drop across the heat exchanger and comparing it to the figures in unit capacity data tables in the
specification catalog. 1.5-2 GPM of flow per ton of cooling capacity is recommended in open loop applications.
Discharge water from the unit is not contaminated in any manner and can be disposed of in various ways, depending on local codes,
i.e. recharge well, storm sewer, drain field, adjacent stream or pond, etc. Most local codes forbid the use of sanitary sewer for disposal.
Consult your local building and zoning departments to assure compliance in your area.
Note:
For open loop/groundwater systems or systems that do not contain an antifreeze solution, set SW1-Switch #2 to the “WELL”
position
(Refer to the Dip Switch Field Selection table). Slow opening/closing solenoid valves (type VM) are recommended to eliminate
water hammer.
Water Quality
In ground water situations where scaling could be heavy or where biological growth such as iron bacteria will be present, a closed loop
system is recommended. The heat exchanger coils in ground water systems may, over a period of time, lose heat exchange capabili-
ties due to a buildup of mineral deposits inside. These can be cleaned, but only by a qualified service mechanic, as special solutions and
pumping equipment are required. Desuperheater coils can likewise become scaled and possibly plugged. In areas with extremely hard
water, the owner should be informed that the heat exchanger may require occasional flushing.
Units with cupronickel heat exchangers are recommended for open loop applications due to the increased resistance to build-up and corro-
sion, along with reduced wear caused by acid cleaning.
Material
Copper
90/10 Cupronickel
316 Stainless Steel
pH
Acidity/Alkalinity
7 - 9
7 - 9
7 - 9
Scaling
Calcium and
Magnesium Carbonate
(Total Hardness)
less than 350 ppm
(Total Hardness)
less than 350 ppm
(Total Hardness)
less than 350 ppm
Corrosion
Hydrogen Sulfide
Less than 0.5 ppm (rotten egg
smell appears at 0.5 ppm)
10 - 50 ppm
Less than 1 ppm
Sulfates
Less than 125 ppm
Less than 125 ppm
Less than 200 ppm
Chlorine
Less than 0.5 ppm
Less than 0.5 ppm
Less than 0.5 ppm
Chlorides
Less than 20 ppm
Less than 125 ppm
Less than 300 ppm
Carbon Dioxide
Less than 50 ppm
10 - 50 ppm
10 - 50 ppm
Ammonia
Less than 2 ppm
Less than 2 ppm
Less than 20 ppm
Ammonia Chloride
Less than 0.5 ppm
Less than 0.5 ppm
Less than 0.5 ppm
Ammonia Nitrate
Less than 0.5 ppm
Less than 0.5 ppm
Less than 0.5 ppm
Ammonia Hydroxide
Less than 0.5 ppm
Less than 0.5 ppm
Less than 0.5 ppm
Ammonia Sulfate
Less than 0.5 ppm
Less than 0.5 ppm
Less than 0.5 ppm
Total Dissolved Solids (TDS)
Less than 1000 ppm
1000 - 1500 ppm
1000 - 1500 ppm
LSI Index
+0.5 to -0.5
+0.5 to -0.5
+0.5 to -0.5
Iron Fouling
(Biological Growth)
Iron, FE
2
+ (Ferrous)
Bacterial Iron Potential
< 0.2 ppm
< 0.2 ppm
< 0.2 ppm
Iron Oxide
Less than 1 ppm, above this level
deposition will occur
Less than 1 ppm, above this level
deposition will occur
Less than 1 ppm, above this level
deposition will occur
Erosion
Suspended Solids
Less than 10 ppm and filtered for
max. of 600 micron size
Less than 10 ppm and filtered for
max. of 600 micron size
Less than 10 ppm and filtered for
max. of 600 micron size
Threshold Velocity
(Fresh Water)
< 6 ft/sec
< 6 ft/sec
< 6 ft/sec
NOTES:
Grains = ppm divided by 17
mg/L is equivalent to ppm
2/22/12