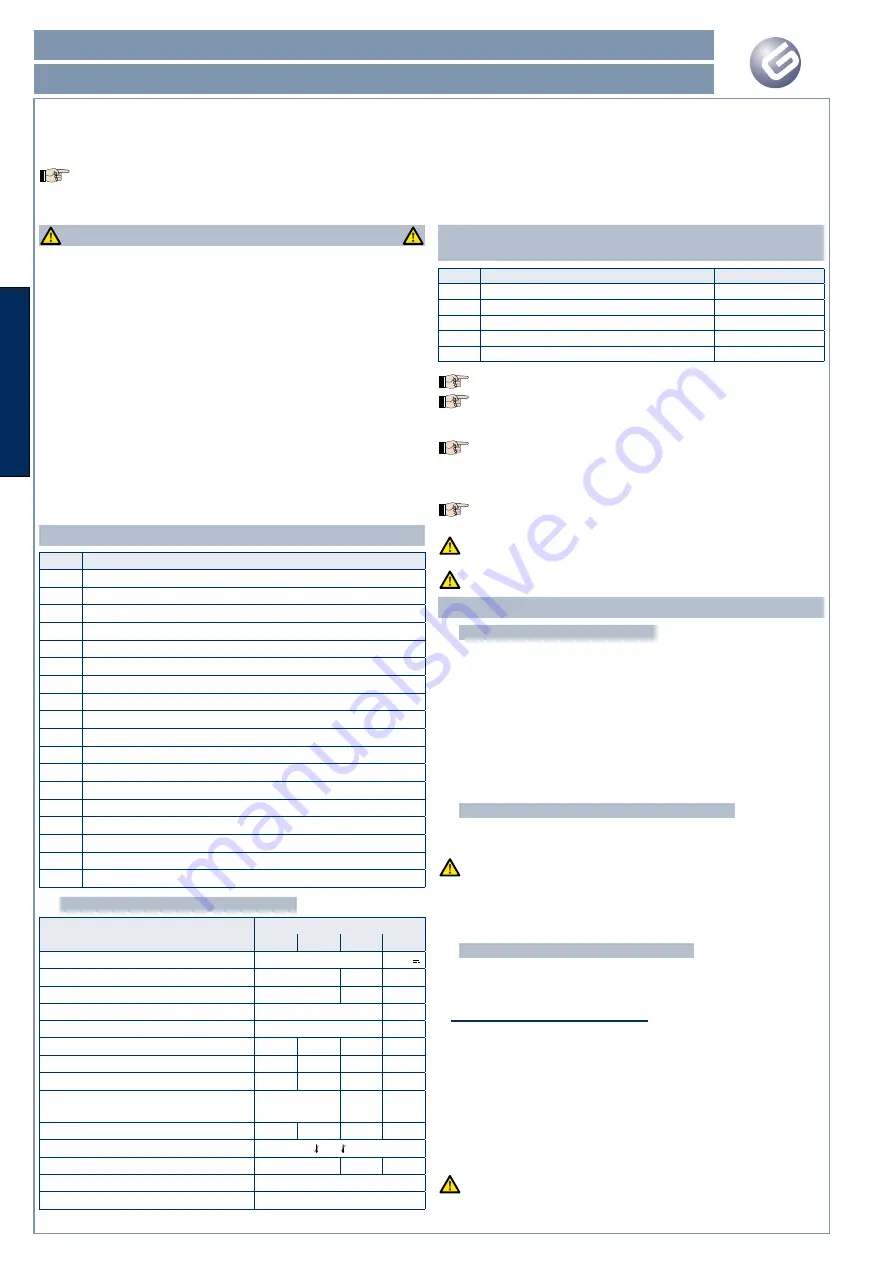
SPIN 3 - SPIN 4 - SPIN 424 - SPIN 6
ENGLISH
Guide for the installer
Page 6
We thank you for having chosen one of our products. GENIUS is certain
that from it you will obtain all the performance you require. All our products
are the result of years of experience in the field of automated systems, with
the added advantage of being part of one of the sector’s leading groups.
The manual contains two removable booklets: one with all the
images pertaining to installation and the other titled “Instructions
for use” to give to the end user, which also contains the system
maintenance record.
IMPORTANT NOTES FOR THE INSTALLER
•
Before beginning installation of the operator, carefully read the entire
manual.
•
Keep this manual for future reference.
• Correct operation and the declared technical specifications are obtained
only by complying with the instructions contained in this manual and
using GENIUS accessories and safety devices.
•
If a mechanical clutch device is not available, to guarantee a suitable
level of automated system safety use a control unit featuring an
adjustable electronic clutch.
•
Do not use the automated system to lift people or things.
•
This automated system has been designed and built for controlling
vehicle access. Avoid any different use.
•
The operator must not be used to control emergency exits or gates
installed on emergency lanes (escape routes).
•
Do not pass while the automated system is moving
•
Whatever is not explicitly provided for in these instructions is to be
considered strictly forbidden.
•
All automated system installation, maintenance and adjustment
operations must be carried out by qualified personnel.
1. DESCRIPTION (Fig.1)
Pos
Description
a
Bar
b
Mechanical stops
c
Spring carrying rod
d
Limit switch
e
Adjustable cams
f
Release device
g
Gearmotor unit
h
Spring plate
i
Balance spring
j
Electronic control unit
k
Spring adjustment tie-rod
l
Earth wire fixing screw
m
Foundation plate
n
Tie-rods
o
Door
p
Upright
q
Release key
r
Encoder
1.1. TECHNICAL SPECIFICATIONS
Model
Spin
3
4
6
424
Power Supply
230 V~ 50 Hz
24 V
Absorbed power (W)
250
380
100
Absorbed current (A)
1,1
1,7
3,5
Thermoprotection (°C)
140
/
Capacitor (µF)
12,5
/
Max Torque (Nm)
60
100
150
100
Opening Time (s)
a
2,5
4
8
4
Max bar length (m)
3
b
5
b
7
b
5
b
Type and frequency of use at 20°C
S3 - 50%
S3 -
60% 100%
Indicative minimum hrs/cycle at 20°C
a
>360 >225 >130 >450
Operating ambient temperature (°C)
-20 +55
Operator weight (Kg)
63
69
63
Protection class
IP X4
Dimensions
See fig. 3 & 4
a
Opening time and number of cycles calculated at a temperature of 20°C
and for installations carried out correctly and without decelerations.
b
No accessories can be applied to SPIN 3 model bars. Articulation
kits cannot be used with bars longer than 4 metres applied to SPIN 4
models.
Accessories cannot be used with bars longer than 6 metres applied to
SPIN 6 models.
2. ELECTRICAL PREPARATIONS
(standard system) Fig. 2
Pos
Description
Cable diameters
a
Operator (electrical power supply)
3x1.5mm
2
b
TX photocells
2x0.5mm
2
c
RX photocells
4x0.5mm
2
d
Key switch
2x0.5mm
2
e
Flashing lamp
2x1.5mm
2
For cable installation, use adequate rigid and/or flexible tubes.
Always separate the low-voltage accessories connection cables
from the power supply cables. To avoid possible interference, use
separate sheathing.
Provide the power supply line with an omnipolar switch featuring
a contact opening distance equal to or greater than 3 mm. We
recommend using a 6 A magnetothermic switch with omnipolar
switching.
Always install a differential switch with a 0.03 A threshold upstream
from the system.
When preparing the power supply line, always follow national
system regulations and use a double-insulation cable.
Securely connect the power supply cable and the accessories
connection cables in the board terminals area.
3. INSTALLING THE AUTOMATED SYSTEM
3.1. PRELIMINARY CHECKS
To ensure automated system safety as well as its correct operation, before
proceeding with installation, check that the following conditions are met:
• When in motion, the bar must not encounter obstacles or flying power
cables.
• The characteristics of the terrain must guarantee sufficient solidity of
the foundation plinth.
•
No tubes or electrical cables should be present in the plinth digging area.
•
If the barrier body is exposed to vehicle transit, provide for adequate
protection against accidental impact, when possible.
• Ensure that there is an efficient earth plate for connecting the upright
profile.
3.2. WALLING THE FOUNDATION PLATE
1.
Assemble the foundation plate as shown in Fig. 5.
2.
Set the foundation plinth as shown in Fig. 6.
The plinth dimensions must be suitable for the terrain type and
model installed.
3.
Wall the foundation plate as shown in Fig. 6 and provide for one or
more sheaths for cable running.
4.
Use a level to ensure that the plate is perfectly horizontal.
5.
Wait for the cement to set.
3.3. MECHANICAL INSTALLATION
1.
Remove the 4 upper nuts from the foundation plate.
2.
Position the upright on the foundation plate, see Fig. 7, and secure it.
3.
Prepare the operator for manual operation, as described in paragraph 4.
3.3.1. r
Ight
or
left
InstallatIon
Depending on installation needs, the automated system can be installed
on the right or left:
Left-hand installation :
Left-hand installation is when, with the barrier
closed, the bar is on the
right side
of the upright,
looking at the automated system from inside the
property (door side).
Right-hand installation :
Right-hand installation is when, with the barrier
closed, the bar is on the
left side
of the upright,
looking at the automated system from inside the
property (door side).
The automated system is supplied ready for left-hand closing,
fig. 8 ref. “A”. If the bar closing direction is the desired one,
go directly to 3.3.2. “Installing the bar”.