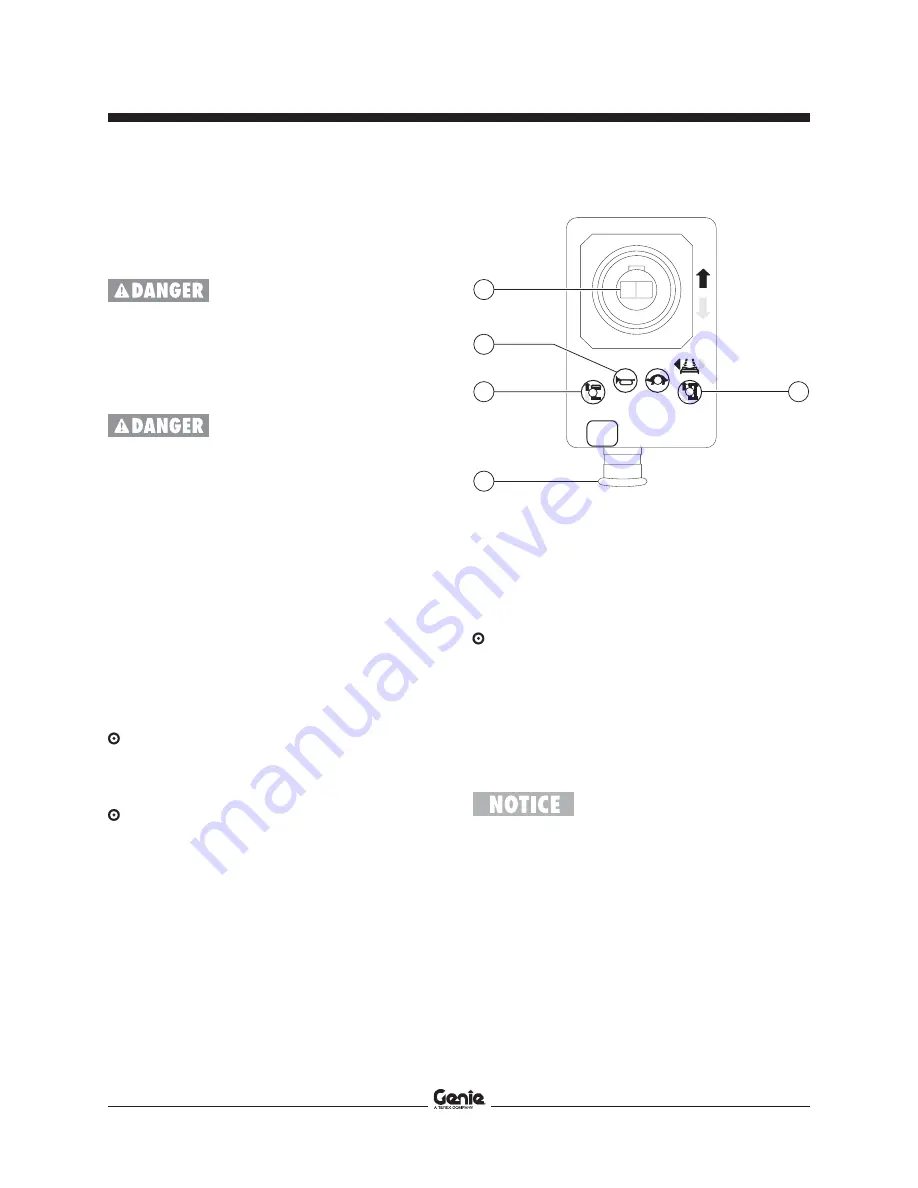
Section 4 • Repair Procedures
REV B
November 2005
Part No. 84700
GR-12 • GR-15 • GR-20
4 - 5
PLATFORM CONTROLS
How to Adjust the
Stowed Drive Speed
Tip-over hazard. Do not adjust the
lift and/or drive speed higher than
specified in this procedure. Setting
the function speeds greater than
specifications could cause the
machine to tip over resulting in
death or serious injury.
Tip-over hazard. This procedure
must only be performed by a
trained service professional.
Attempting this procedure without
the necessary skills will result in
death or serious injury.
1 Pull out the red Emergency Stop button to the
on position at the ground controls.
2 Push in the red Emergency Stop button to the
off position at the platform controls.
3 Turn the key switch to platform control.
4 At the platform controls, press and hold the lift
function select and horn buttons and pull out
the red Emergency Stop button to the on
position.
Result: The diagnostic display will show "PS."
5 Release the lift function select and horn
buttons.
Result: The diagnostic display will show the
maximum lift speed percentage.
a
joystick controller JC1 with thumb
steering rocker SW6
b
horn button BN5
c
lift function select button BN9
d
red Emergency Stop button P2
e
drive function select button BN8
6 Press the drive function select button.
Result: The diagnostic display will show the
stowed drive speed percentage.
7 Use the steering thumb rocker switch on the
joystick to increase or decrease the stowed
drive speed percentage. Refer to Section 2,
Specifications, for function speeds.
8 Turn the key switch to the off position.
Any change in software settings
will not take effect until the key
switch is turned to the off position.
a
b
e
c
d