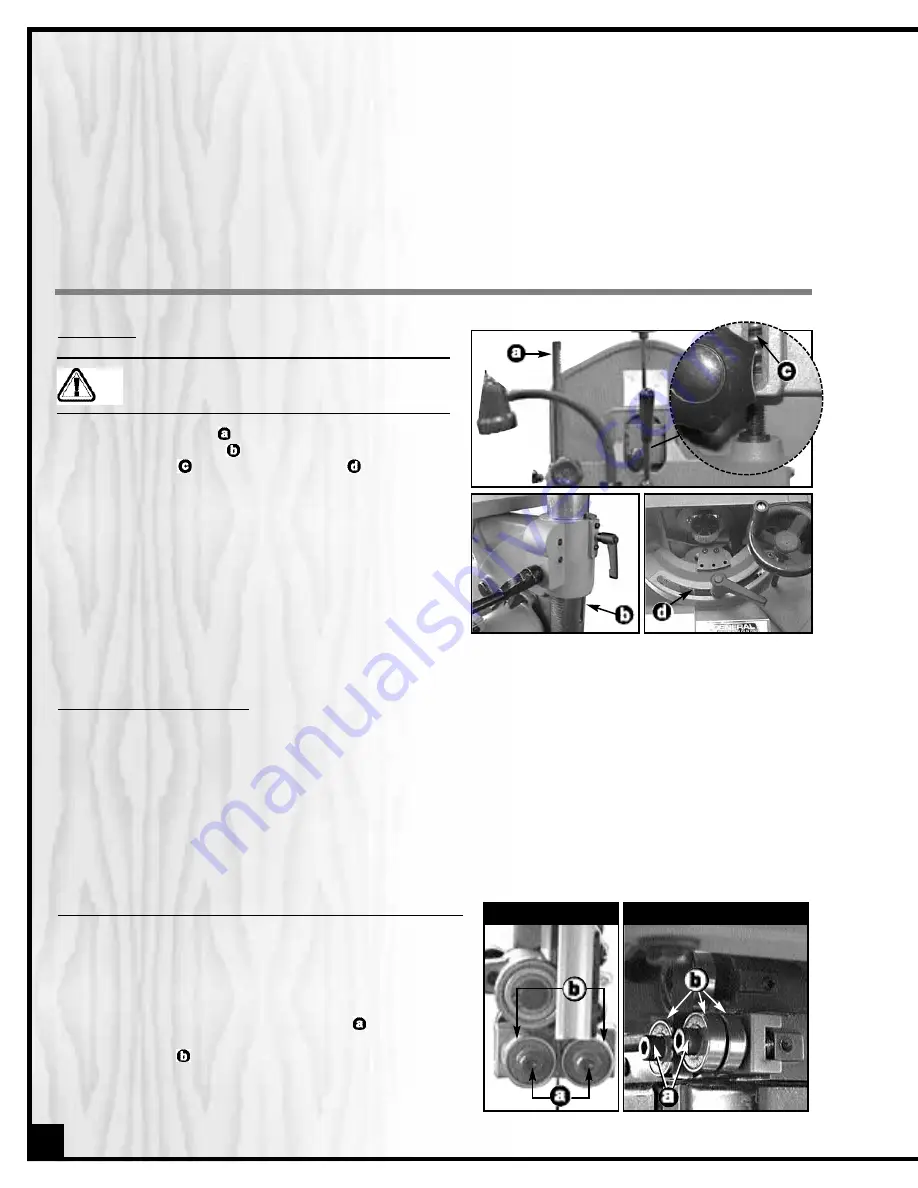
26
4.
Do not allow dirt, pitch or gum to build up on the table, blade, guide/thrust bearings. Clean as needed with
gum and pitch remover.
Note: Do not immerse the bearings in the gum and pitch remover.
5.
To prevent rust and from forming on the unpainted cast iron of the table, and so that the wood slides easily while
cutting, apply a light coating of paste wax or use regular applications of any after-market surface protectant or
rust inhibitor.
REPLACING THE BANDSAW BLADE
The blade should be replaced when worn out.
Refer to the following symptoms to determine whether or not it is time to replace the blade:
- It is not cutting as fast.
- It is not able to follow a cutting line as it used to.
REQUIRED MAINTENANCE
REPLACING THE UPPER / LOWER BLADE GUIDES AND THRUST BEARINGS
Bearings should be verified each time the blade is replaced.
Check if they turn well. If not, the blade will get stuck or jam-
med between them and will wear prematurely.
To replace the upper/lower blade guides, proceed as follows:
1.
Loosen and remove the two Allen bolts
, using the sup-
plied 5 mm Allen key. Removing the two bolts will free the
blade guides
.
2.
Replace the blade guides with new ones and tighten
with the two Allen bolts.
LOWER BLADE GUIDES
UPPER BLADE GUIDES
LUBRICATION
Disconnect machine from power source, before
performing any lubrication or maintenance.
Keep the blade guard
and upper frame height adjust-
ment rack and pinions
as well as the blade tension
adjustment screw
and the table trunnion
well greased
and free of dust or debris.
Clean and remove dust, debris, and old grease after every
10-15 hours of use. After cleaning, reapply grease as need-
ed. (Use any all purpose grease.)
The motor and all bearings are sealed and permanently
lubricated – no further lubrication is required. No other part
of this bandsaw needs lubrication.
Summary of Contents for 90-200 M1
Page 39: ...39 NOTES...