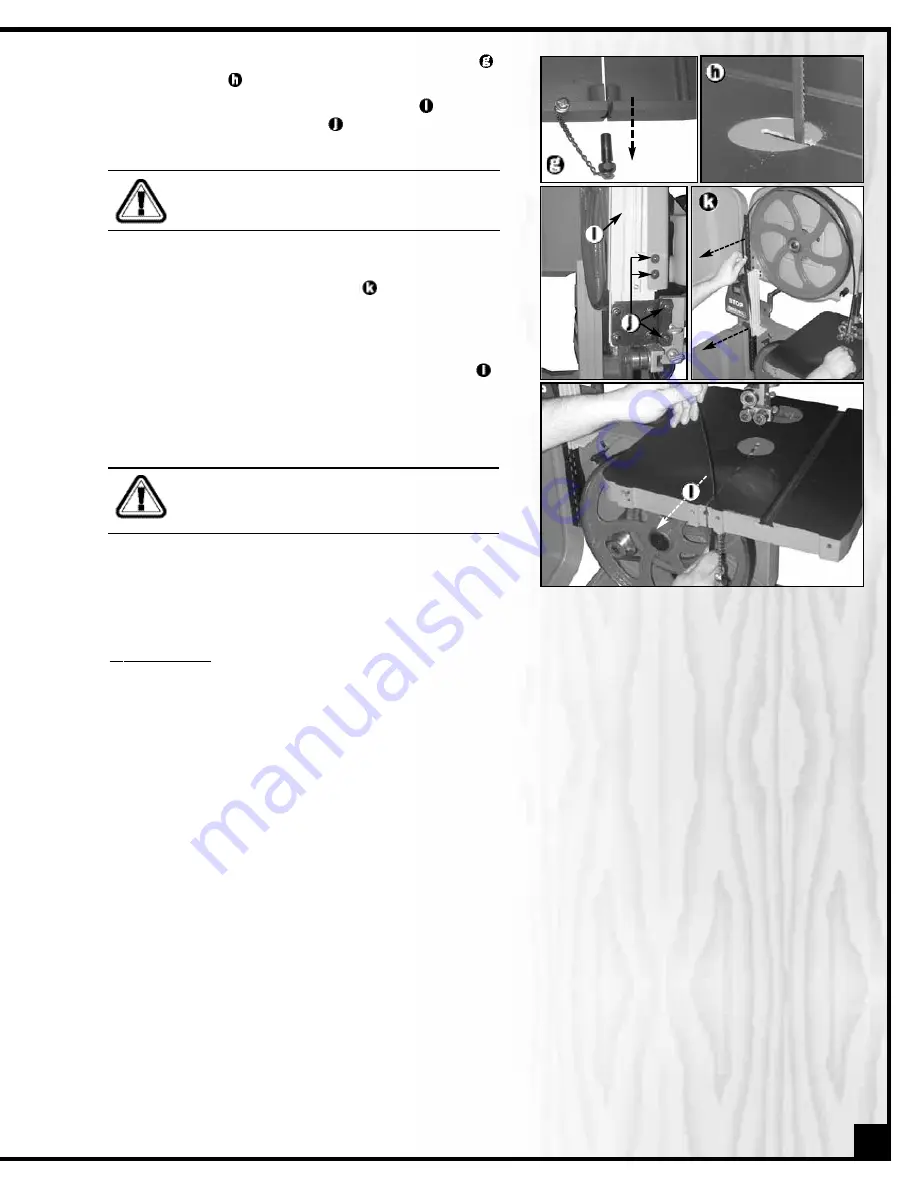
17
4.
Remove the table alignment pin from the table slot
and
the red insert
from the center of the table.
5.
Remove the right hand side blade guard
by removing
the four Phillips head screws
.
6.
Open the top and bottom wheel cover doors and bring
the left hand side of the loose blade toward you and out
of the left hand blade guard slot
.
Note: You may want to use a thick shop towel to handle the loose
blade or wear a pair of heavy duty work gloves
.
7.
With the blade perpendicular to the wheels, feed the
blade through the table slot to free it from the saw
.
8.
Carefully hang the blade on a hook in a safe, dry place in
your workshop if it will be re-used, or dispose of it safely if it
is worn or damaged.
Blade teeth are sharp. Use care when handling a
saw blade.
Do not attempt to coil up the blade as it was when
you first purchased it as it has a tendency to pop
open unexpectedly and could cause injury.
BLADE SELECTION
There are a variety of different types of bandsaw blades on the market to suit various cutting applications. Your results
may vary based on usage, experience and personal preference.
Replacement blades made from high carbon steel can be purchased in a variety of lengths and widths from your
General® International dealer (See “Recommended Optional Accessories” on page 29) or (depending on availabil-
ity) from your local tool dealer. There are many standard sizes that should be readily available in most areas. The use
of any size outside of the saw’s specified length or width range is not recommended and can lead to serious injury
and/or damage to the machine.
Some general guidelines to consider when choosing bandsaw blades:
• Wider blades with fewer teeth per inch are best suited to cutting straight lines, re-sawing and for sweeping curves,
but will not turn tight radius curves. They will cut quickly and aggressively but do have a tendency to bind (or get
stuck in the cut) if turned too sharply.
•Narrower, thinner blades with more teeth per inch will cut more slowly but can turn much tighter corners for cutting
more intricate work.
Common causes of blade breakage:
• Poor guide bearing alignment and adjustment.
• Forcing or twisting a wide blade around a short radius.
• Feeding the workpiece too quickly.
• Dull teeth.
• Too much blade tension.
• Setting blade guard assembly too high above the workpiece.
• Lumpy or improperly finished braze or weld on the blade.
•Continuous running of blade when not cutting.
Summary of Contents for 90-200 M1
Page 39: ...39 NOTES...