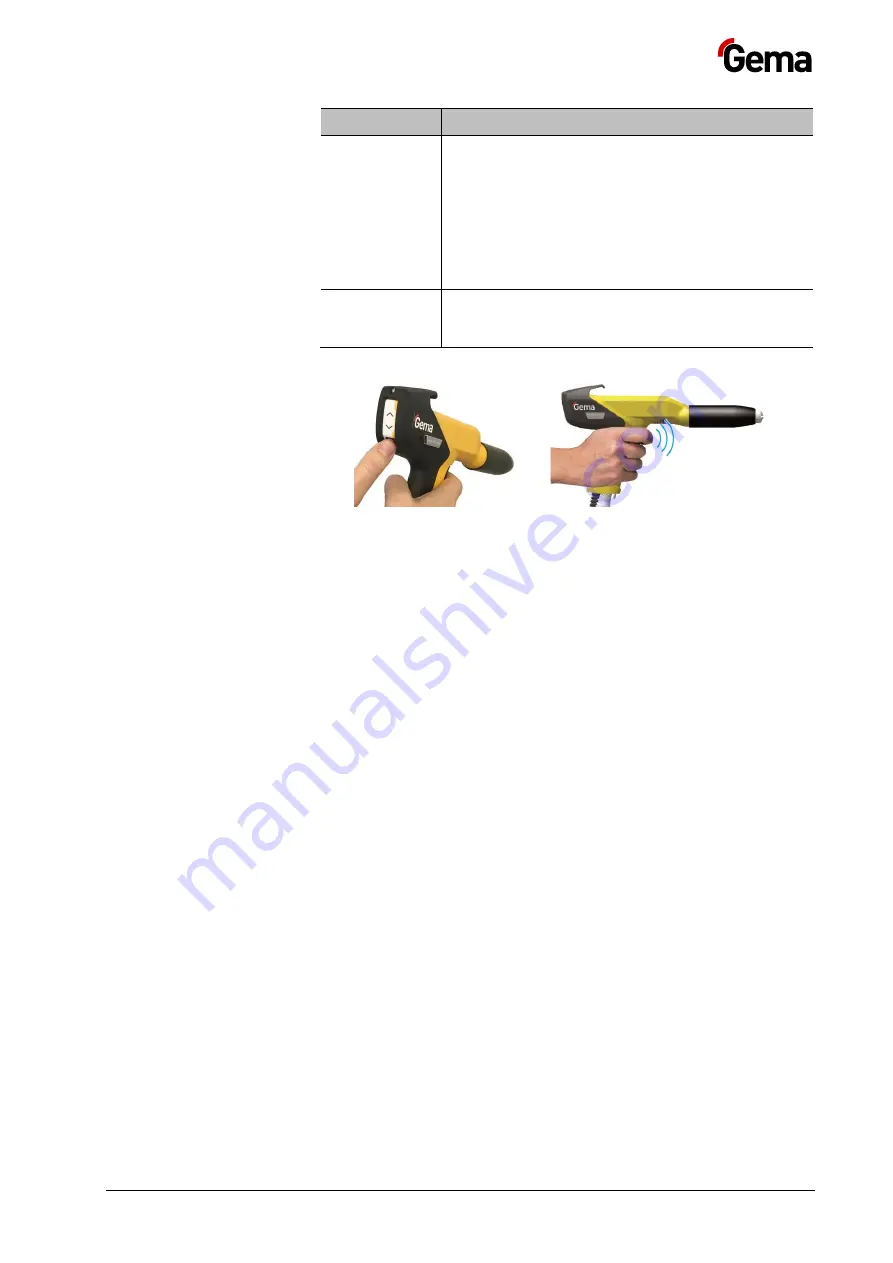
Rev. 01 08/20
OptiFlex Pro BN
Operation
33
Procedure
Effect
Automatic
(automatic)
– The rinsing process is started
– Injector, powder hose, gun and spray nozzle
are purged using compressed air
– The PowerClean function enables parallel
cleaning of other components, such as the
fluid intake unit, powder container, etc.
– The rinsing mode is exited if the automatic
rinsing sequence has finished.
Manual
(manual)
The operator controls the number and length of the
PowerClean impulse by pressing the gun trigger a
second time
3.
STOP =
OR
OR the cleaning mode is terminated automatically.
After completion of the PowerClean procedure, the controller switches
back to coating mode.
Summary of Contents for OptiFlex Pro BN
Page 12: ...Rev 01 08 20 12 Safety OptiFlex Pro BN ...
Page 19: ...Rev 01 08 20 OptiFlex Pro BN Product description 19 Rating plate fig 4 ...
Page 20: ...Rev 01 08 20 20 Product description OptiFlex Pro BN ...
Page 24: ...Rev 01 08 20 24 Assembly Connection OptiFlex Pro BN ...
Page 36: ...Rev 01 08 20 36 Operation OptiFlex Pro BN ...
Page 44: ...Rev 01 08 20 44 Maintenance Repairs OptiFlex Pro BN ...
Page 48: ...Rev 01 08 20 48 Disposal OptiFlex Pro BN ...
Page 51: ...Rev 01 08 20 OptiFlex Pro BN Spare parts list 51 OptiFlex Pro BN Spare parts fig 11 ...
Page 57: ...Rev 01 08 20 OptiFlex Pro BN Spare parts list 57 ...
Page 58: ......
Page 60: ...Rev 01 ...