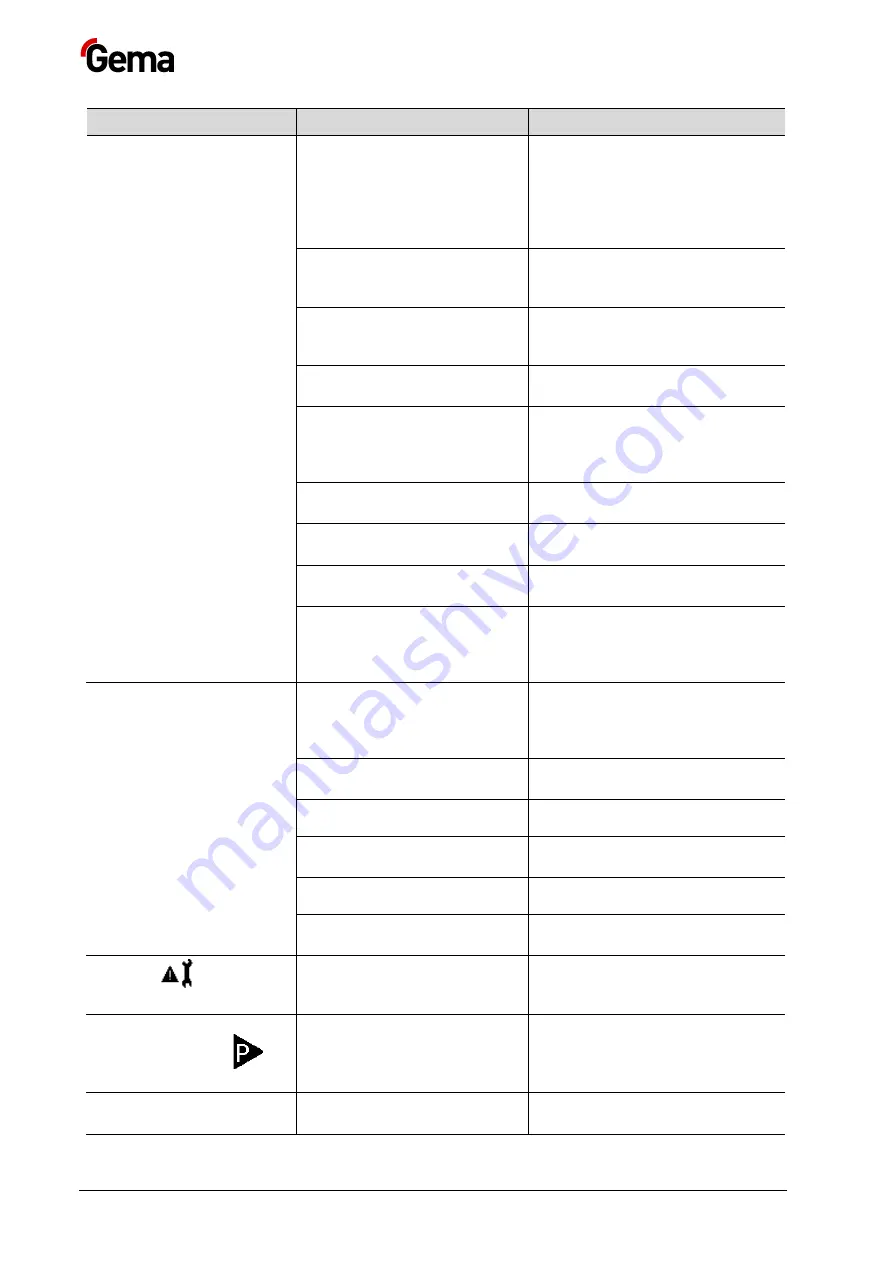
Rev. 00 03/22
50
•
Fault clearance
OptiFeed BigBag (FPS16)
Incident
Causes
Corrective action
Service life of the pinch valve
has expired (defective)
– Replace pinch valve and
associated protective filter
element
– Blow off or replace
contaminated hose
connection
Filter elements of the powder
chamber tend to become
clogged
Run the cleaning program, replace
the filter elements
Lifetime of the filter elements in
the powder chamber expired
(clogged)
Replace the filter elements
Powder hoses tend to clog due
to sintering
Clean or replace the powder hoses
The conveying hose or suction
hose is clogged
Empty the powder hose with
compressed air or manually
(
Warning
– powder will be
expelled!)
Conveying pressure desired
value C0 incorrectly set
Set correctly ()
Vacuum desired value C1
incorrectly set
Set correctly ()
Pinch valve pressure desired
value C2 incorrectly set
Set correctly ()
Oil or water in the system
Do not use the pump before
ensuring that oil or water will be
separated before entering into the
pump, otherwise contact Gema
Indicator on powder pump
does not light up
No operating voltage
The corresponding voltage must
be present at connection
2.1
: PP07
= +24 VDC; PP07-S = 110-240
VAC
Indicator defective or
incorrectly connected
Replace/connect correctly
Main board is defective
Replace/send in for repair
Power pack is defective (PP07-
S)
Replace
Fuse is defective (PP07-S)
Replace
Main switch is defective (PP07-
S)
Replace
Indicator
flashes
The parameter memory test
was erroneous
Reset to the default values:
Press for 5 seconds
Then set parameters, if necessary
Powder pump is not
conveying, indicator
is
not flashing
No
Pump on
control signal
A control signal must be applied at
connection
2.1
PIN 2
If the LEDs on the valve
connectors do not light up, the
Replace pump control or send it in
for repair
Summary of Contents for FPS16
Page 6: ......
Page 34: ...Rev 00 03 22 34 Start up OptiFeed BigBag FPS16 ...
Page 38: ...Rev 00 03 22 38 Operation OptiFeed BigBag FPS16 ...
Page 52: ...Rev 00 03 22 52 Fault clearance OptiFeed BigBag FPS16 ...
Page 54: ...Rev 00 03 22 54 Disposal OptiFeed BigBag FPS16 ...
Page 60: ......
Page 62: ...Rev 00 ...