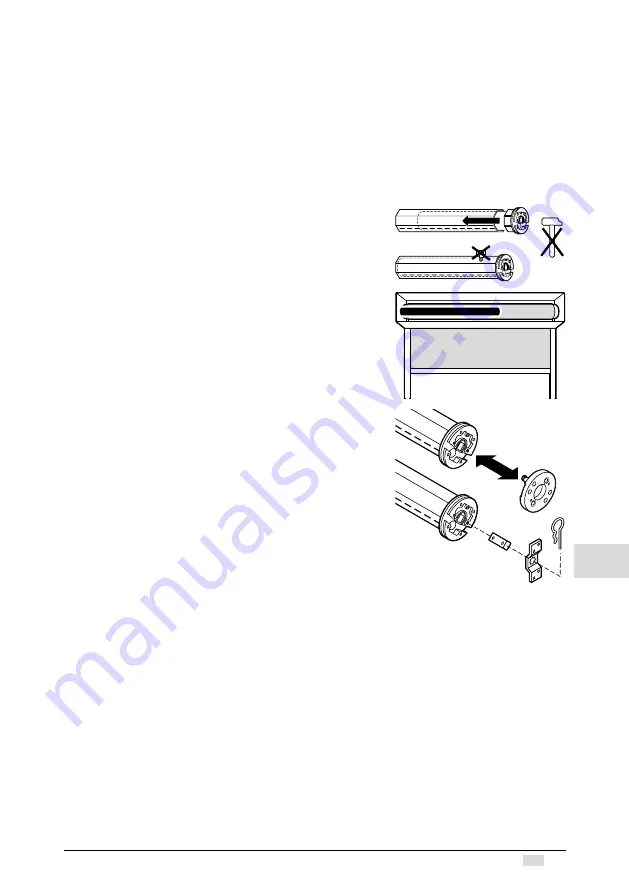
5
www.geiger.de
EN
EN
6. Installation instructions
I
Before fixing, the strength of the masonry or of the subsurface is to be
checked.
I
Prior to installation please check to ensure there is no visible damage
to the motor like cracks or open cables.
I
Caution: If the tube is screwed/riveted to the drive, the measure must
be taken from the tube end to the center of the drive and marked on
the tube.
When drilling the winding shaft
never
drill into the
area of the tubular motor!
When inserting into the shaft, the tubular motor must
not
be struck and must
not
be allowed to fall into the shaft.
Installation into the screen:
Insert motor with a suitable adapter and drive into the shaft
up to the stop of the shaft adapter.
Fix the motor support on the side piece.
Fix the motor together with the shaft on the motor support.
Depending on the selected motor head,
different fixation systems can be used:
– Place the motor with square insert in the star-shaped
bearer and lock with pin
– Place the motor into the existing engine bearer and
lock
– Place the motor in a compatible engine bearer with clip
system and lock with spring or rotating lever
I
The Geiger-SOLIDline motor is suitable
for shaft diameters from 50 mm!