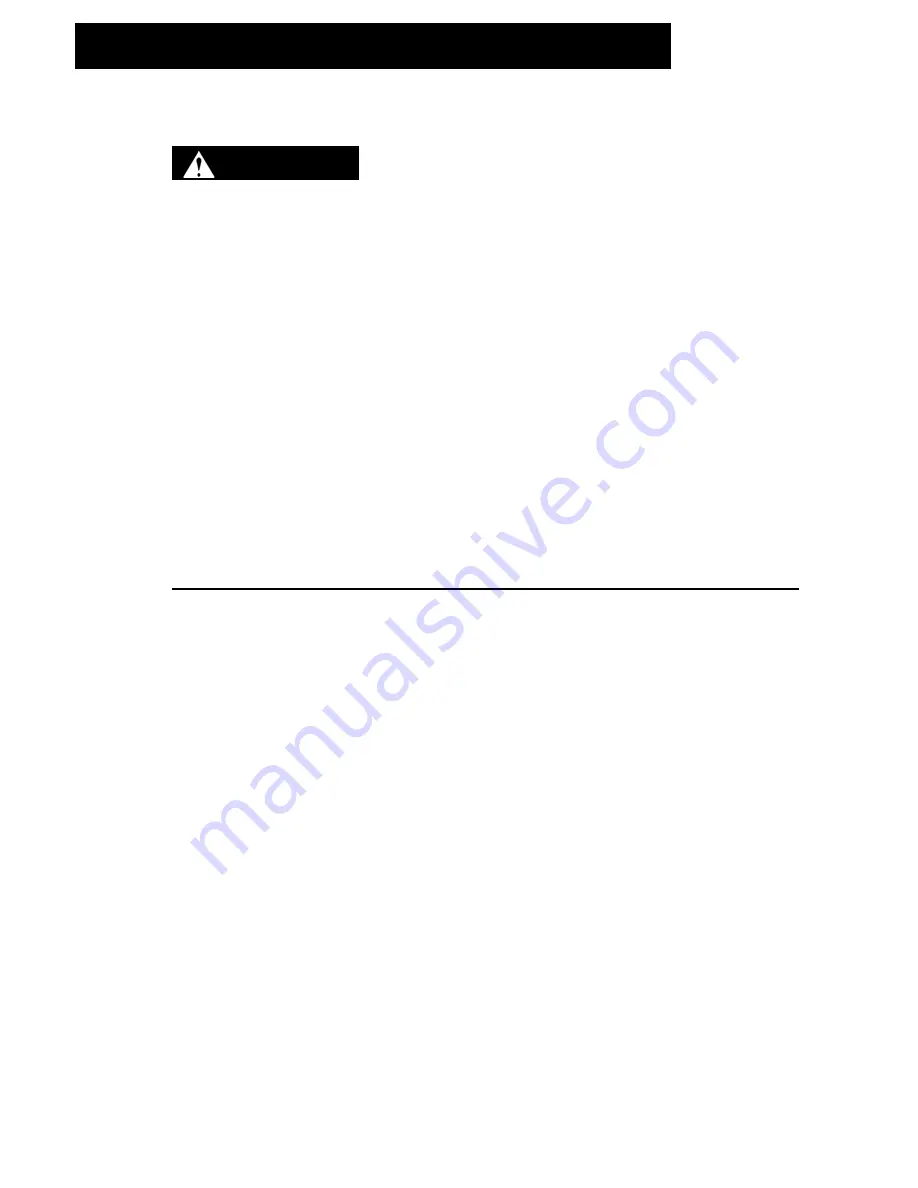
917387/BP0310
51
CHAPTER 5
SERVICE
Before servicing the machine, unless
expressly instructed to the contrary, exercise
the MANDATORY SAFETY SHUTDOWN PROCEDURE (page 6).
After service has been performed, be sure to restore all guards,
shields and covers to their original positions before resuming
operation.
This
Service
chapter details procedures for performing routine maintenance
checks, adjustments and replacements. Most procedures are referred to in the
Troubleshooting
and
Maintenance
chapters of this manual. Refer to the
Mainte-
nance Interval Chart
(page 81) for service intervals. Refer to the separate engine
manual for engine-related adjustments, lubrication and service procedures.
Note: All service procedures, except those described under the Dealer Services
topic are owner-operator responsibilities.
Important: Always dispose of waste lubricating oils and hydraulic fluids
according to local regulations or take to a recycling center for disposal. Do not
pour onto the ground or down the drain.
Dealer Services
The following areas of component service, replacement and adjustments require
special tools and knowledge for proper servicing and should be performed only
by your authorized Gehl skid-steer loader dealer: hydrostatic drive components,
hydraulic system pumps, valves, hydraulic cylinders, electrical components
(other than battery, fuses or relays).
WARNING
Summary of Contents for V270
Page 1: ...Skid Steer Loader Operator s Manual Form No 917387 BP0310 English V270 V270 EU ...
Page 8: ...4 917387 BP0310 Notes ...
Page 22: ...18 917387 BP0310 Notes ...
Page 54: ...50 917387 BP0310 Notes ...
Page 76: ...72 917387 BP0310 Notes ...
Page 84: ...80 917387 BP0310 Notes ...
Page 86: ...82 917387 BP0310 Maintenance Log Date Hours Service Procedure ...
Page 87: ...917387 BP0310 83 Maintenance Log Date Hours Service Procedure ...
Page 88: ...84 917387 BP0310 Maintenance Log Date Hours Service Procedure ...
Page 100: ...96 917345 AP0608 ...