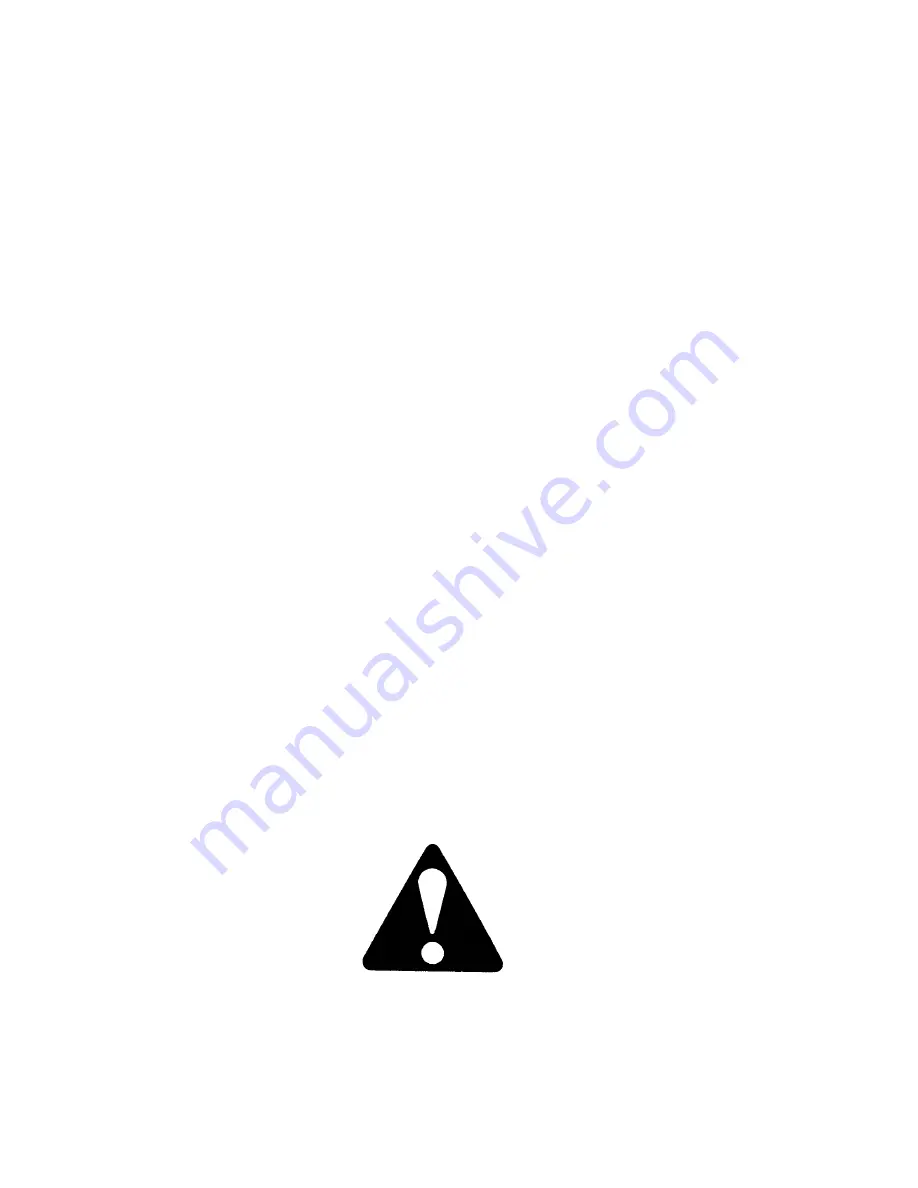
Chapter 1
INTRODUCTION
The information in this Operator’s Manual was written to give the owner/operator assistance in preparing, adjust-
ing, maintaining and servicing of the Paver. More importantly, this manual provides an operating plan for safe and
proper use of the machine. Major points of safe operation are detailed in the
SAFETY
chapter of this manual. A
chart of standard hardware torques is located in the back of this manual.
The GEHL Company asks that you read and understand the contents of this manual COMPLETELY and
become familiar with your new machine, BEFORE attempting to operate it.
Throughout this manual, information is provided which is set in
italic
type and introduced by the word
NOTE.
Be
sure to read carefully and comply with the message or directive given. Following this information will improve
your operating or maintenance efficiency, help you to avoid breakdowns or damage and extend your machine’s
life.
A plastic container is provided on the unit for storing the Operator’s Manual. After using the Manual, please return
it to the container and keep it with the unit at all times! If this machine is resold,
GEHL
Company recommends
that this Manual be given to the new owner.
“Right” and “left” are determined from a position standing on the Screed Platform and facing forward.
Our wide Dealership network stands by to provide you with any assistance you may require, including genuine
GEHL
service parts. All parts should be obtained from or ordered through your
GEHL
Dealer. Give complete
information about the part and include the model and serial numbers of your machine. Record the serial number
in the space provided on the previous page, as a handy record for quick reference.
GEHL
Company reserves the right to make changes or improvements in the design or construction of any part
without incurring the obligation to install such changes on any unit previously delivered.
The GEHL Company, in cooperation with the
American Society of Agricultural Engineers and the
Society of Automotive Engineers, has adopted this
SAFETY ALERT SYMBOL
to pin point characteristics which, if NOT properly fol-
lowed, can create a safety hazard. When you see
this symbol in this manual or on the machine itself,
you are reminded to BE ALERT! Your personal safey
is involved!
907389/AP297
2
Printed In U.S.A.
Discount-Equipment.com