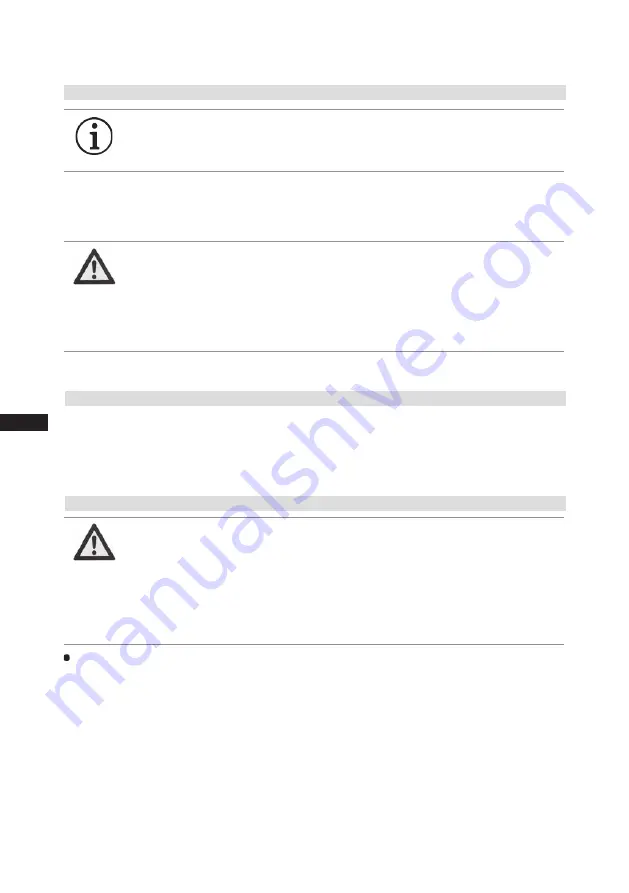
18
D
GB
F
E
96422-07.2018-DGbFEI
6
|
Commissioning
WARNING
When the compressor is not running, depending on ambient
temperature and amount of refrigerant charge, it is possible
that the pressure may rise and exceed permitted levels for the
compressor. Adequate precautions must be taken to prevent this
happening (e.g. using a cold storage medium, a receiver tank, a
secondary refrigerant system, or pressure relief devices)
.
6.1 Preparations for start-up
The compressor has undergone trials in the factory and all functions have been tested. There are
therefore no special running-in instructions.
Check the compressor for transport damage!
INFO
To protect the compressor against inadmissible operating conditions,
high pressure and low pressure pressostats are mandatory on the
installation side.
6.3 Leak test
Carry out the leak test on the refrigerating plant in accordance with EN 378-2 or a corresponding
safety standard, while always observing the maximum permissible overpressure for the compressor.
DANGER
Risk of bursting!
The compressor must only be pressurised using nitrogen (N
2
).
Never
pressurise with oxygen or other gases!
The maximum permissible overpressure of the compressor must
not be exceeded at any time during the testing process (see name
plate data)!
Do not mix any refrigerant with the nitrogen as this
could cause the ignition limit to shift into the critical range.
6.2 Pressure strength test
The compressor has been tested in the factory for pressure integrity. If however the entire system is
to be subjected to a pressure integrity test, this should be carried out in accordance with EN 378-2
or a corresponding safety standard
without the inclusion of the compressor.