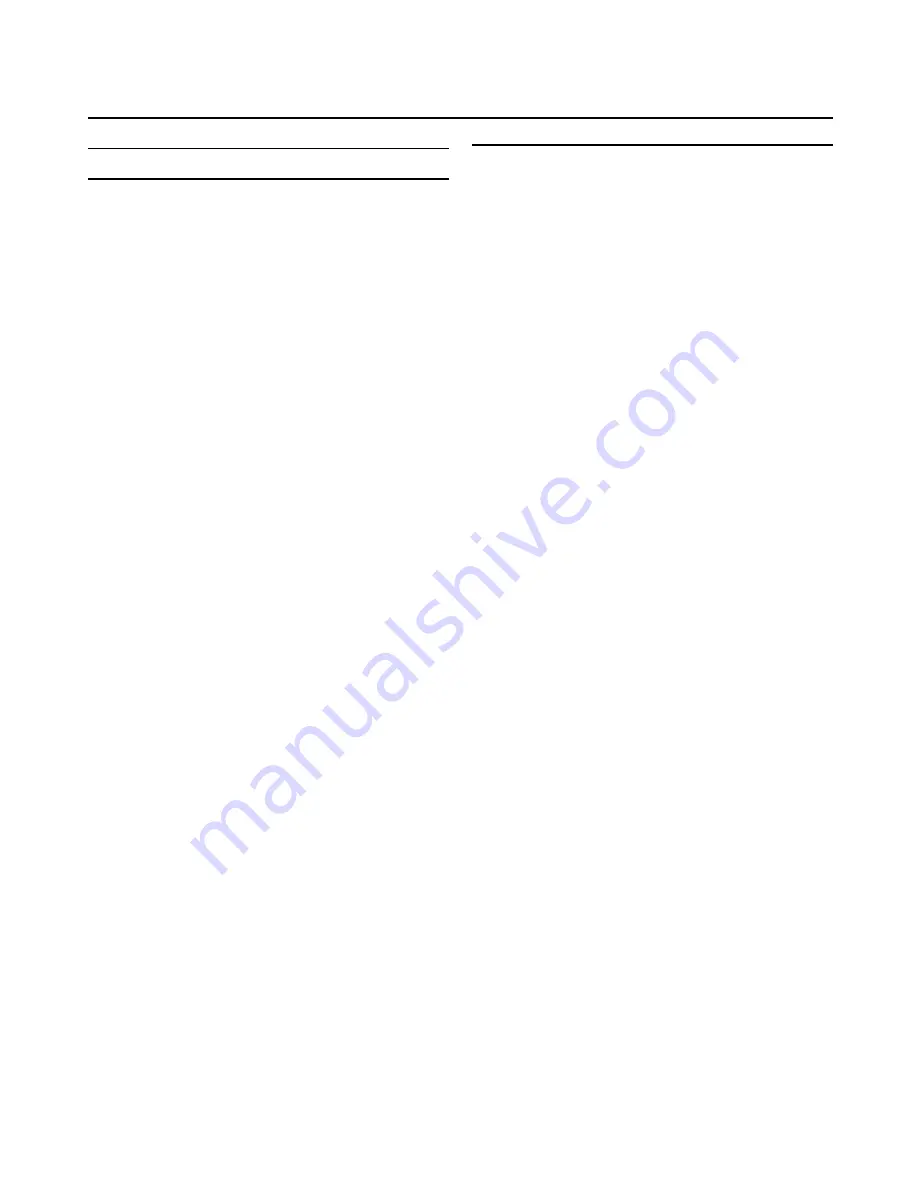
8
3.1 GENERAL SPECIFICATIONS
3.1.1 Control System
3.1 1.1 Electronic Controller - 8 buttons
Used on 5700 & 5900 models. The controller has eight
surface mounted switches.
The control switches are:
Rinse & Hold Fast Wash
Normal Wash
Super Wash
Heated Dry
Water Temp Delay Start
Clear
Ten surface mounted green LED’s illuminate and display the
actual wash, water temperature and delay mode.
Five surface mounted green LED progress indicators illumi-
nate and display the actual wash mode as follows:
Pre-Wash
Wash
Rinse
Dry
Clean
Each of the five green LED’s is also utilized within the fill time
mode to display the fill time in seconds. All off board
components are triac controlled, except the wash motor
relay and the heating element for heating & drying which are
also relay controlled.
3.1.1.2 Switch- Power Select- Rotary 5 position
Used on the 5600 model.
5 position switch with 45° indexing.
240/125VAC, 16A.
Double pole, double throw.
Silver contact studs.
Electrical connection - 1/4" Quick Connect male terminals.
The “
Off” position is vertical with “Normal” on the left and
“
Boost” on the right.
3.1.1.3 Timer - Electromechanical
Used on the 5600 model.
120VAC, 60Hz, 16A.
Type - Soft-set rotary self-indexing control not “push/pull” on/
off.
Hollow shaft - 3/32" diameter bore.
A push rod is required for manual advance operation.
Electrical connection - 1/4" Quick Connect male terminals
located on PCB.
Type timer drive motor - synchronous.
Resistance of windings 1.9K @ 68°F.
Rated input - 15mA.
3.1.2 Water Circulating System
3.1.2.1 Wash Motor Capacitor
370VAC, 60Hz, 15µF.
Type - metallized Polypropylene.
Electrical connection - 2 x 1/4" x 1/32" Quick Connect
terminals.
For usage 120V, 60Hz @ 185°F
3.1.2.2 Water Capacities
The water solenoid inlet valve is rated at a nominal 1.25 US
gallons per minute. There are five possible fill time settings
for electronic models: 75, 80, 90,100, 110. There are two
settings for electromechanical models: 80 & 100 seconds.
The factory default setting of 80 seconds results in a nominal
fill of 1.17 to 1.95 US gallons subject to supply water
pressure.
Water consumption: 6.0 US gallons (electronic models on
fast wash)
Water consumption: 5.0 US gallons (rotary models on fast
wash)
Actual program selected will vary water consumption.
Stainless Steel Tub capacity: 2.91 US gallons (sump capac-
ity overfill level)
3.1.2.3 Solenoid Water Inlet 60Hz
Operating Supply Pressure Range:
- Static Hot: 20 psi minimum – 120 psi maximum
Maximum inlet supply water temperature - 160°F
Nominal delivery flow rate from valve - 1.25 US gallons per
minute.
120VAC, 60Hz.
Solenoid resistance 750/950 ohms
Electrical connection - 2 x 1/4" x 1/32" Quick Connect
terminals.
3.1.2.4 Drain Pump
Rated Input - 30W, 0.25A, 120VAC, 60Hz.
Resistance of Field Winding @ 68°F - 35 ohms ±10%.
Insulation - Class F.
Nominal RPM - 3000, 2 pole motor.
Motor temperature protector field winding - 338°F trips open.
Outlet nozzle equipped with non-return flap valve.
Nominal Discharge Rate - 3.96 - 5.28 US gallons/minute @
3.25 Ft/head.
3.0 SPECIFICATIONS