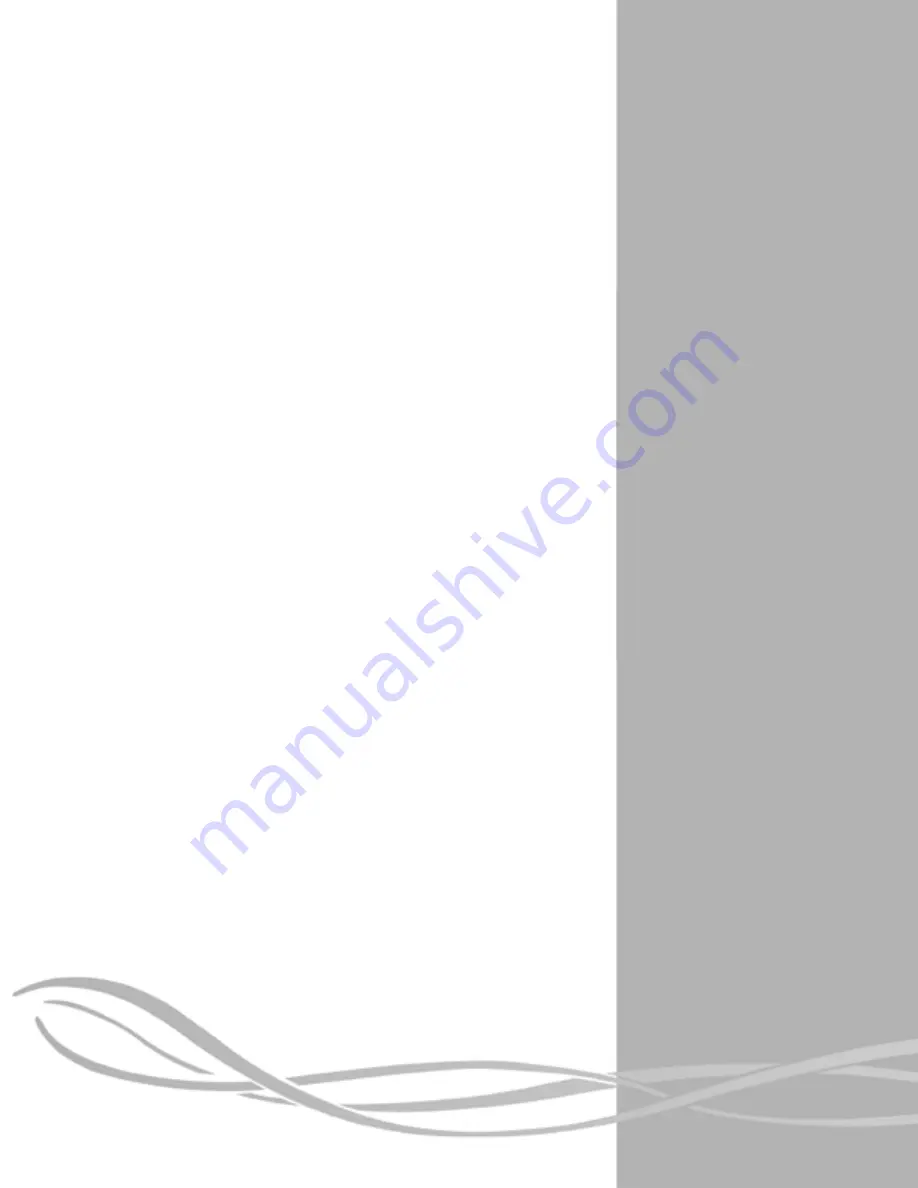
USA
GE Panametrics
221 Crescent Street, Suite 1
Waltham, MA 02453-3497
Telephone: (781) 899-2719
Toll-free: (800) 833-9438
Fax: (781) 894-8582
E-Mail: [email protected]
http://www.panametrics.com
Ireland
GE Panametrics
Shannon Industrial Estate
Shannon, County Clare
Ireland
Telephone: 353-61-470200
Fax: 353-61-471359
E-Mail: [email protected]
Summary of Contents for Moisture Image 1 Series
Page 2: ...Moisture Image Series 1 Service Manual ...
Page 8: ...Chapter 1 ...
Page 31: ...Chapter 2 ...
Page 61: ...Appendix A ...