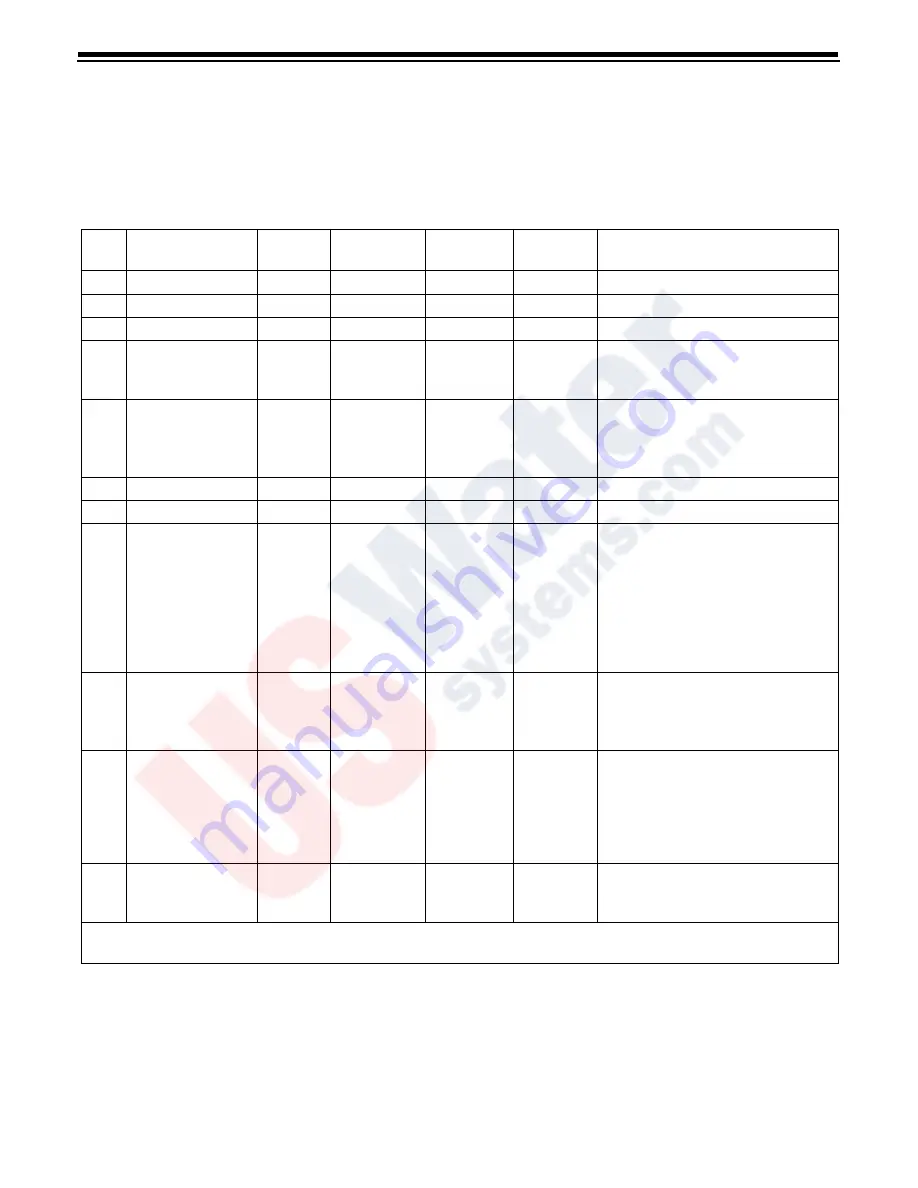
33
Level II Programming – P Values
Level II program parameters can be adjusted to fine-tune
the conditioner’s operation. The parameters are
accessible by pressing and holding the UP and DOWN
buttons until the control displays a “P” value. Note: The
control must be in the home position to change settings.
See Table below for Level ll parameters. Typically the Level
ll parameters will not need to be adjusted as the default
settings accommodate most applications. Contact your
Water Treatment Professional before attempting any
programming.
*Not used for Magnum valves.
Description
Range
Minimum
Increments
Default
Units
Notes
P9
Units of Measure
0-1
1
(2)
0 = US 1 = Metric
P10 Clock Mode
0-1
1
(2)
0 = 12 Hr 1 = 24 Hr
P11 Service Interval
0-250
1
0
Months
Uses 30 days for each month; 0 = off
P12
Remote
regeneration
switch delay
3-250
1
60
seconds
Time remote switch must be active
to start regeneration.
P13*
Chlorine Generator
Options
(not used on
Magnum systems)
0-2
1
0
0 = No chlorine generator
1 = salt check only
2 = generate chlorine
P14* Refill Rate
1-700
1
(1)
gpm x 100
P15* Draw Rate
1-700
1
(1)
gpm x 100
P16
Reserve Type
(not used for
alternating mode)
0-3
1
0
0 = variable reserve delayed
regeneration
1 = fixed reserve delayed
regeneration
2 = variable reserve immediate
regeneration
3 = fixed reserve immediate
regeneration
P17
Initial average or
fixed reserve
(not used for
alternating mode)
0-70
1
30
% of
Capacity
Depends on value entered in P16
P18 Flow sensor select
0-5
1
(1)
0 = internal magnum NHWB,
1=1" turbine
2 = 2" turbine
3 = User defined K-factor
4 = User defined pulse equivalent
5 = Internal Magnum HWB
P19
K-factor or Pulse
equivalent
1.00-
99.99
0-9999
0.01
1
0.01
1
K-factor P18=3;
Pulse Equivalent P18 = 4
Notes: (1) Default selected with valve type and resin volume.
(2) Factory Default is "0” for North America units and "1” for World units.