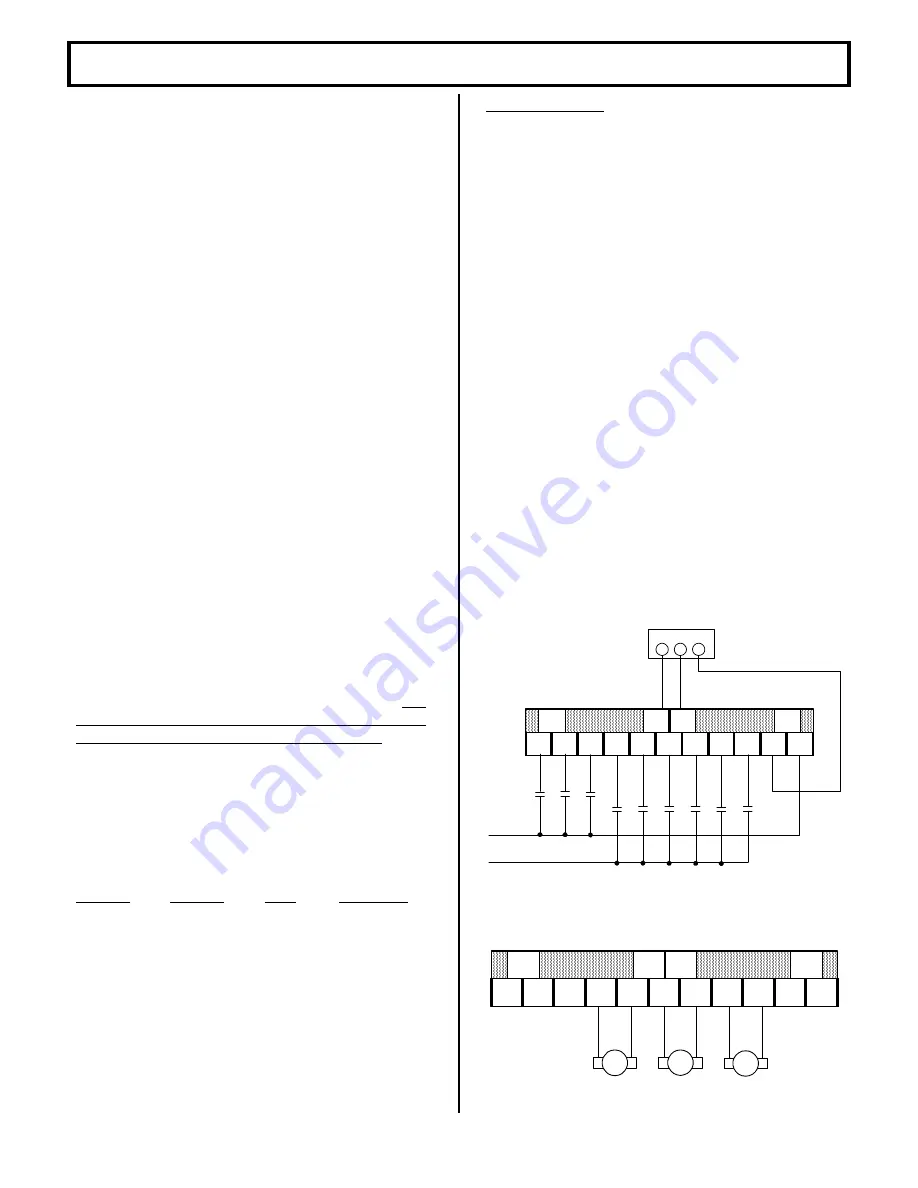
INSTALLATION AND OPERATION MANUAL
SX TRANSISTOR CONTROL
Page
51
IMPORTANT NOTE: Status Codes 93, 94 and 95 are only
checked when a neutral signal is present (i.e., open start
switch or open F/R switch). The status code is displayed
and the speed limit enabled when the control is returned
to the run mode. Do not use status code 93 speed limit for
applications requiring immediate speed limit on switch
closure.
Section 5. TRUCK MANAGEMENT MODULE (TMM)
Section 5.1 General Features
The Truck Management Module is a multi-functional
accessory card (IC3645TMM7A), or an integral function of
the SR Pump control when used with the SX Family of
Traction controls. The Module provides the OEM with the
ability to initiate status codes or operator warning codes to
be displayed on the Dash Display whenever a normally
open switch or sensor wire provides a signal to the
Module.
Typical wiring diagrams and outline drawings for the
TMM7A accessory card and SR family of Pump TMM
functions are shown in Sections 5.4 and 5.5.
Section 5.3 Installation
The TMM Module can be used to display a separate status
code indicating an over temperature of traction motors,
hydraulic motors, or any other device or system that can
activate a switch that closes.
WARNING: Before any adjustments, servicing or act
requiring physical contact with working components,
jack drive wheels off the floor, disconnect the battery and
discharge the capacitors in the traction and pump
controls, as explained in Section 4.4.
It can also be used as a Brush Wear Indicator (BWI). The
Brush Wear Indicator is designed to detect a “worn-out
brush” and display a fault code on the Dash Display to
warn maintenance personnel that the motor brushes need
to be replaced before they wear to the point of causing
destructive damage to the motor commutator surface. The
BWI function is compatible with any sensor that short
circuits to the motor armature to signal limits of brush
wear.
The TMM7A accessory card should be mounted to a flat
surface (in any plane) in an area protected from water, oil
and battery acid. Mounting dimensions are shown in
Section 5.5. Two (0.187 inch, 4.75mm) mounting holes are
provided.
Section 5.4 Connection Diagrams
Note: Motor armature must be in the positive side of the
battery circuit.
Section 5.4.1 TMM7A Card Connections
1
3
4
5
2
7
9
6
8
10
11
12
13
14
15
BATTERY
NEGATIVE
3
4
5
6
8
11
10
12
10
8
9
PLUG Y
BATTERY
POSITIVE
TMM7A CARD CONNECTIONS
9
1
A1-1
A1-2
A2-1
A3-1
A2-2
A3-2
Section 5.2 Operation
The Module utilizes 9 OEM input points and 3 output points
that connect to the "Y" plug on the traction logic card.
Due
to the low level signal value of this output, shielded wire
should always be used to insure proper operation.
The
input to the Module is either a switch or sensor wire
closure to battery negative or positive. The following table
outlines the status code displayed for each input, when
that point is closed to battery negative or positive, as
indicated.
TMM7A Pump
Card Control
Status
Terminal
Terminal Code Connect
To
Section 5.4.2 Typical Brush Wear Sensor Connections
TB1
P16 90
*
Neg
TB3
P11 91 Neg
1
3
4
5
2
7
9
6
8
10
11
12
13
14
15
BRUSH WEAR SENSOR CONNECTIONS (TYPICAL)
ARM
1
2
1
TRACTION
PUMP
PWR STEER
ARM
2
2
1
ARM
3
2
1
TB4 P15
92
Neg
TB5 P3
93
*
Pos
TB6
P4
93 *
Pos
TB8 P5
94
Pos
TB10 P6
94
Pos
TB11 P8
95
Pos
TB12 P9 95 Pos
* Status codes 90 and 93 can also be programmed with the
Handset to reduce the speed of the truck from 100 to 0
percent-on-time.
October 2002