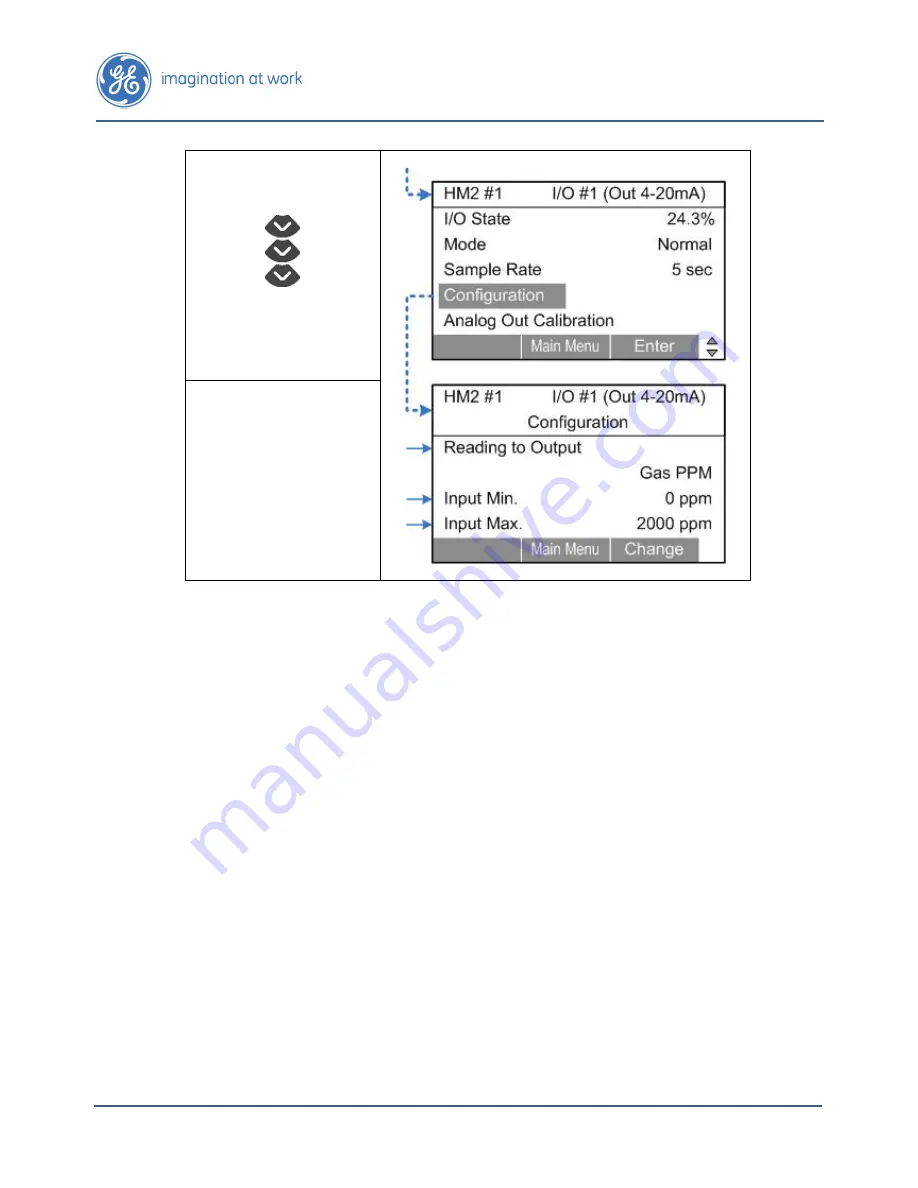
Hydran* M2 Installation Guide
Page 42
16375 v9.0 Oct 12
Select
Configuration
Press
Enter
Set up all the
Configuration
parameters as required.
Notes:
•
Input Min
is the lowest possible reading for this signal; this value will deliver
a current output corresponding to 4 mA.
•
Input Max
is the highest possible reading for this signal; this value will
deliver a current output corresponding to 20 mA.
•
Repeat the above procedure for each analog output.
Configuring the Models
If required, for configuration of the models, refer to Section C.3 of the
Multi-Host
Software Manual
.