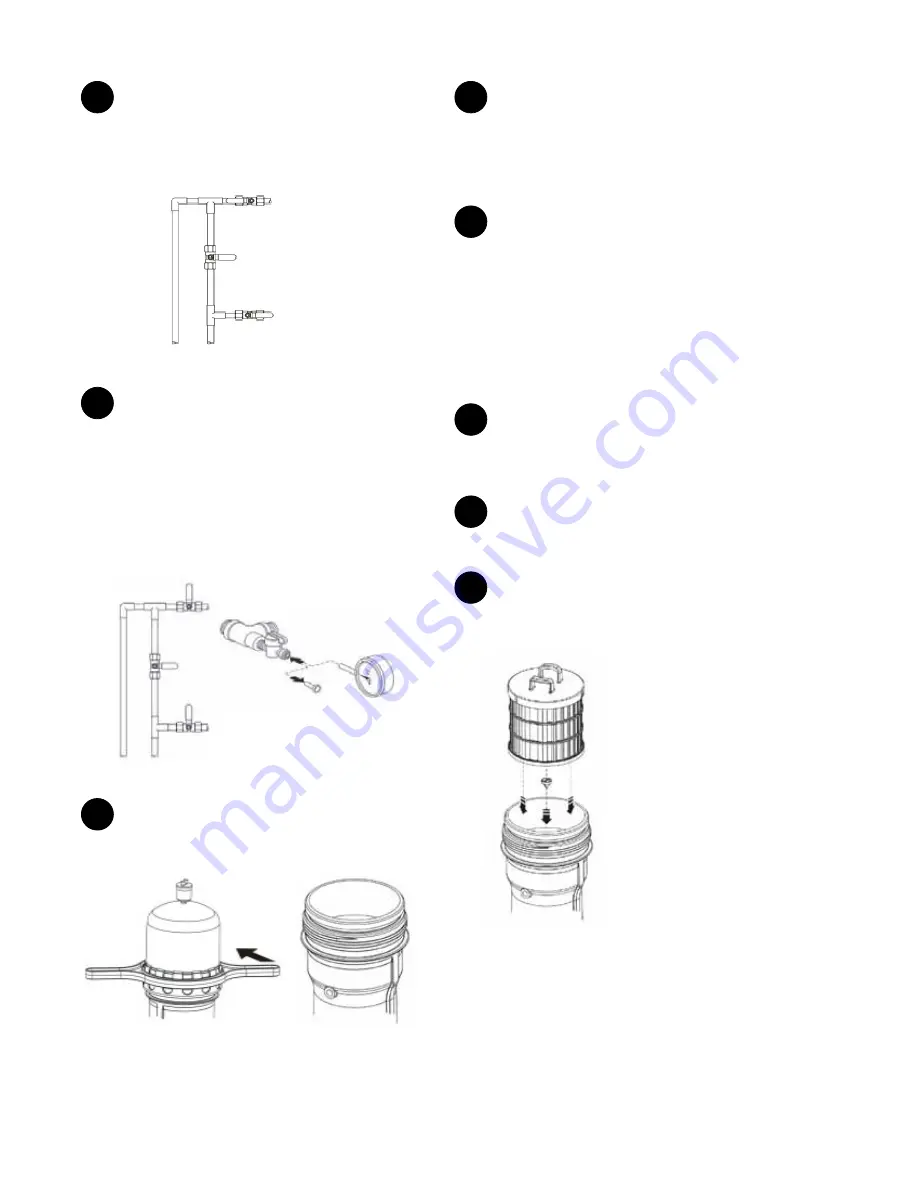
44
4
Open a nearby cold water high demand tap, then open
the outlet valve. This will prevent antifreeze from spreading
throughout the piping system. Run the tap for 30 minutes.
Open all other cold water taps in the home and flush
separately for 1 minute each.
Inlet Valve
Bypass Valve
Outlet Valve
Figure 79
5
Close the inlet valve and outlet valve. Partially drain the
system using the manual flush function for 1 minute to
depressurize the system. Refer to the Controller Functions
section on how to perform a manual flush sequence. Remove
the plug from the mini ball valve on the inlet fitting assembly
by depressing the lock ring and pulling on the plug. Slowly
open the mini ball valve to ensure there is no pressure in the
system. Water will flow out, but should not spray. Close the
mini ball valve immediately. If there is spray, repeat the
manual flush sequence. Replace the plug in the mini ball valve.
figure 80
6
Remove system cap. If a stainless steel prefilter was
stored in the prefilter cavity over the winter remove, wash and
set aside.
Open
figure 81
7
Be sure the water level in the system is 2" above the
bottom of the prefilter cavity. Add more water by slowly
opening the inlet valve if necessary. Add 2 cups (500 ml) of
unscented household chlorine bleach (Clorox) (5 - 6% chlorine)
or 1 cup (250 ml) chlorine bleach (12% chlorine), maximum 3
months old, to the system.
8
Allow the system to soak for 15 minutes. With the
system cap tightened, drain the system using the controller.
Open the inlet valve and allow system to pressurize.
NOTE:
If the winterization spring start up is combined with the
annual maintenance cleaning procedure, the System must soak
for 60 minutes. If the System is on ground or well water, the
chlorine must be substituted with Homespring MC1 cleaning
agent instead of chlorine bleach. Follow the directions on the
package for preparing the MC1 cleaning agent. Never mix
chlorine bleach with the MC1 cleaning agent.
9
Open the outlet valve and a nearby COLD water tap to
remove chlorine from the system. Run the tap fully open for 5
minutes. Further flushing must be performed by the
homeowner.
10
Close the inlet valve and outlet valve. Use the controller
to depressurize the system. Ensure that there is no pressure
inside the system as described in step 5.
11
Open the system cap and install a new carbon prefilter. If
using a stainless steel prefilter, insert a clean, undamaged
stainless steel prefilter and replace the system cap.
Inspect and clean thimble filter
as needed.
figure 82