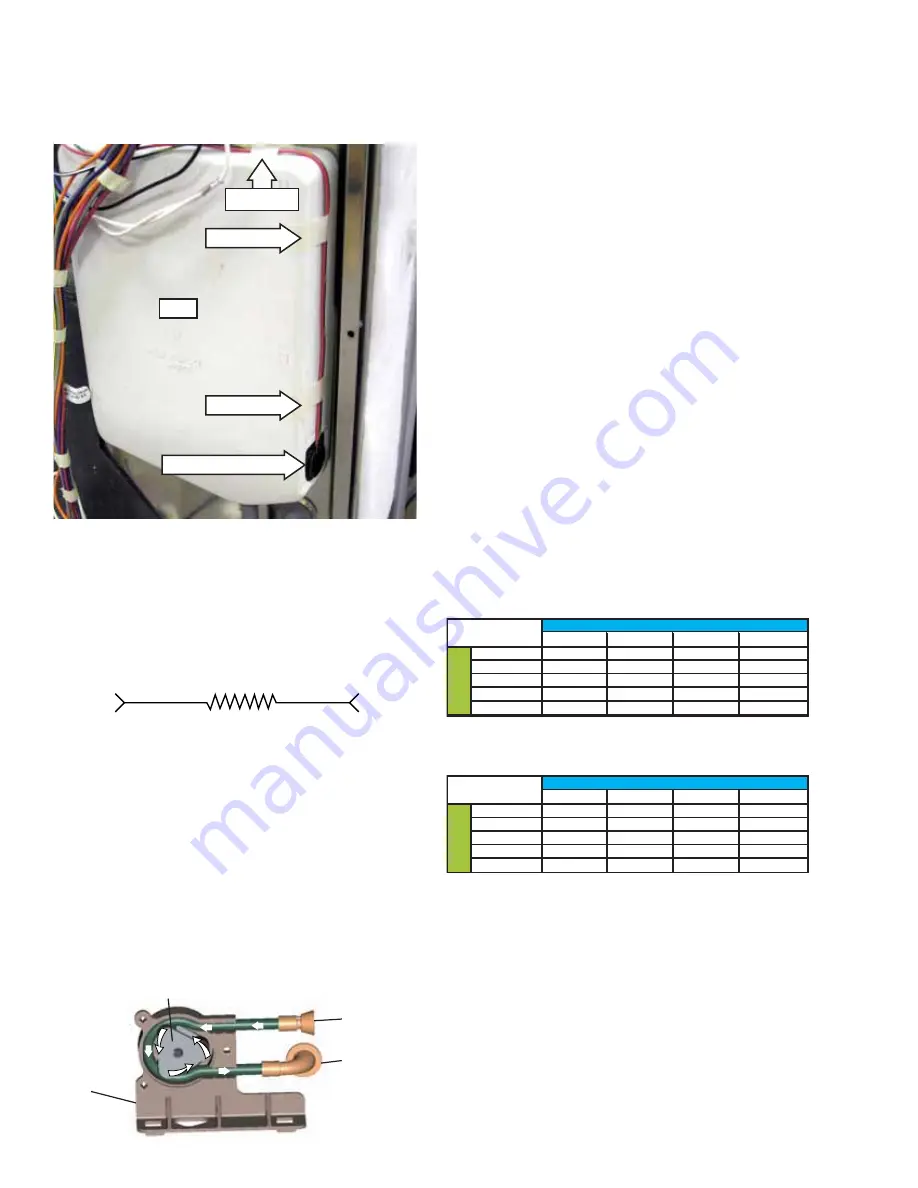
– 20 –
The routing of the DC wiring from the tank is very
important. The 3 tape points on the tank keep the
DC wiring perpendicular to the AC harness wiring
running down across the front of the tank.
Tank
Sensor and Gasket
Tape Point
Tape Point
Tape Point
Note: The dispenser tank, sensor with wire harness,
and gasket are only available as a complete
assembly (Part # WD35X10058). They are shipped
with a new dispenser tank retaining collar.
Detergent Level Sensor Strip Circuit
BRN/YELLOW
RED
DETERGENT
SENSOR
J4-3
J4-1
The dispenser pump operates on 120 VAC. During
each prewash cycle, the pump is energized for 5
seconds, dispensing 4 ml of detergent.
The electronic control uses two inputs to determine
the total amount of detergent dispensed during the
main wash cycle:
• Soil level determined by the turbidity sensor
• Water hardness as calibrated for the location
A water hardness selection mode permits the
calibration of the water hardness for the location
at installation. (See
Water Hardness Test and
Calibration
.)
To determine the amount of detergent to dispense
during the main wash, the electronic control uses
the following formula:
4 ml x Number of Prewashes
+ 25 ml + Additional Quantity for Hardness
The additional quantity is a predefi ned quantity
of detergent based on the water hardness level
programmed into the control.
Positive Displacement Pump
The SmartDispense positive displacement pump
consists of a continuous fl exible tube running from
the detergent reservoir to the inner door detergent
outlet. The tube runs around the inside edge of the
pump housing. A 3-roller impeller fi ts tightly into
the center of the pump housing, with each of the
3 rollers squeezing the sidewall of the tube. As the
impeller is driven counterclockwise by the motor, it
squeezes out a predetermined amount of detergent
for each 1/3 revolution of the impeller.
Approximate Detergent Use
From
Detergent
Reservoir
To Detergent
Outlet
Pump
Housing
Impeller
(Continued next page)
1
2
3
4
1
33
41
49
57
2
35.4
43.4
51.4
59.4
3
37.8
45.8
53.8
61.8
4
40.2
48.2
56.2
64.2
5
42.6
50.6
58.6
66.6
Smart Dispense Bottle Duration
1
2
3
4
1
10.3
8.3
6.9
5.9
2
9.6
7.8
6.6
5.7
3
9.0
7.4
6.3
5.5
4
8.4
7.0
6.0
5.3
5
8.0
6.7
5.8
5.1
Dosage (ml)
Har
d
ness
Soil Level
Hard
n
ess
Bottle Duration (wks)
Soil Level
Smart Dispense Dosage Amount
SmartDispense Dosage Amount
SmartDispense Bottle Duration