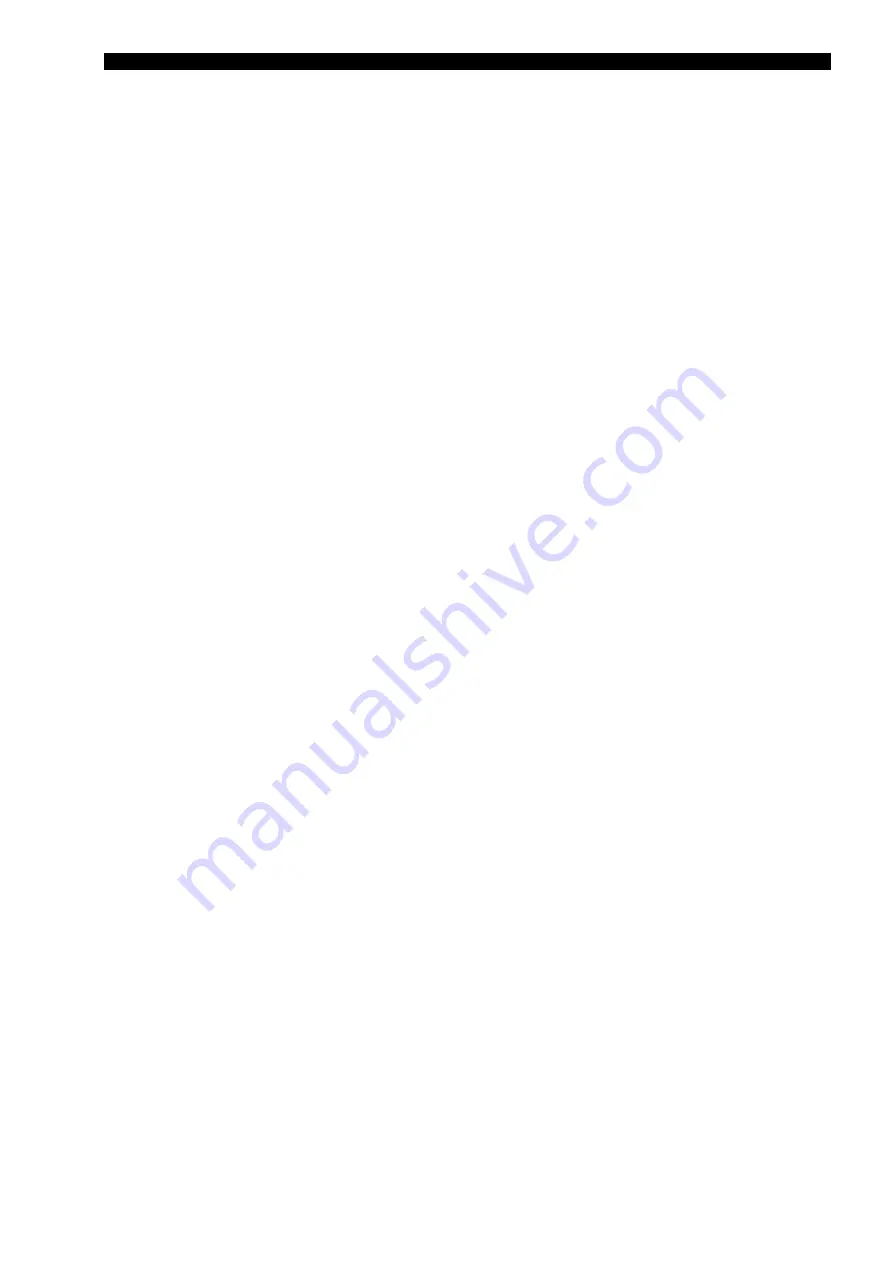
7. ACCEPTANCE TESTS
GEK-98514B
BUS1000 Busbar Protection
7-9
7.10. SWITCHING DEVICE TEST
Check that the stabilization resistors are shortened.
Set up the following adjustments to all the differential boards:
Slope: 0.8
Supervision: 0.5
Connect position 7 to bus B apP to terminals (see table 2: Bar connection & disconnection). The rest
of the line latching relays must be in STANDBY position (0). If not so, apply positive to terminals (see table 2:
Bar connection & disconnection), corresponding to the positions where there is a latching relay connected
(1).
Apply 1 A through terminals (see table 1: Input current, phase A). Trip phase 1 of differential B.
Apply Vdc between X11 (positive) and X12 (negative). In that moment, the three latching relays BUS/AB will
operate (they go to 1); differential A trips, while differential B stops tripping.
Connect bus B pushing the green button on the test rack, and reset the DAL module and the DDF module of
the phase under test.
In such conditions, check by measuring in the leads of the differential module corresponding to bus A (phase
1) that the restraint is 0.9 Vdc and the differential is 0.9 Vdc. Bus B (phase 1) restraint and differential
corresponding measures will be 0.
Disconnect direct current in terminals X11 (+) and X12 (-). In that moment, the three latching relays BUS/AB
will operate (they go to O); differential B trips while differential A stops tripping.
In such conditions, check by measuring in the leads of the differential module corresponding to bus B (phase
A) That the restraint is 0.9 Vdc and the differential is 0.9 Vdc. Bus A (phase A) restraint and differential
corresponding measures will be 0.
Connect bus A pushing the green button on the test rack, and reset the DAL module and the DDF module of
the phase under test.
Remove the current applied to terminals (see table 1: Input current, phase A), applying it now, through
terminals (see table 1: Input current, phase B). Repeat the same steps, taking into account that the one
under test is phase B now.
Remove the current applied to terminals (see table 1: Input current, phase B), applying it now through
terminals (see table 1: Input current, phase C). Repeat the same steps, taking into account that the one
under test is phase C now.
Remove current and DC from X11 (+), X12 (-), when these terminals had it applied.
Connect the corresponding latching relay of bus A to the position 7, applying positive to terminal (see table 2:
Bar connection & disconnection) (1). In that moment, having the bus B latching relay connected (1), the three
BUS/AB latching relays will operate (they go to 1).
Disconnect bus A latching relay of position 7, applying positive to terminal (see table 2: Bar connection &
disconnection). In that moment, the BUS/AB latching relays will operate again (they go to 0).
Remove the jumpers from the stabilization resistors.
Summary of Contents for BUS1000
Page 6: ......
Page 8: ......
Page 34: ...5 HARDWARE DESCRIPTION 5 10 BUS1000 Busbar Protection GEK 98514B ...
Page 36: ...6 RECEIVING HANDLING AND STORAGE 6 2 BUS1000 Busbar Protection GEK 98514B ...
Page 54: ...8 FINAL INSTALLATION AND COMMISSIONING 8 4 BUS1000 Busbar Protection GEK 98514B ...
Page 56: ...9 TESTS AND PERIODICAL MAINTENANCE 9 2 BUS1000 Busbar Protection GEK 98514B ...
Page 66: ...10 FIGURES 10 10 BUS1000 Busbar Protection GEK 98514B ...
Page 74: ...11 DIMENSIONS 11 8 BUS1000 Busbar Protection GEK 98514B FIGURE 23 CABINET 226B2211F21 ...
Page 104: ...13 SCHEMATICS DOUBLE BUSBAR 13 16 BUS1000 Busbar Protection GEK 98514B ...