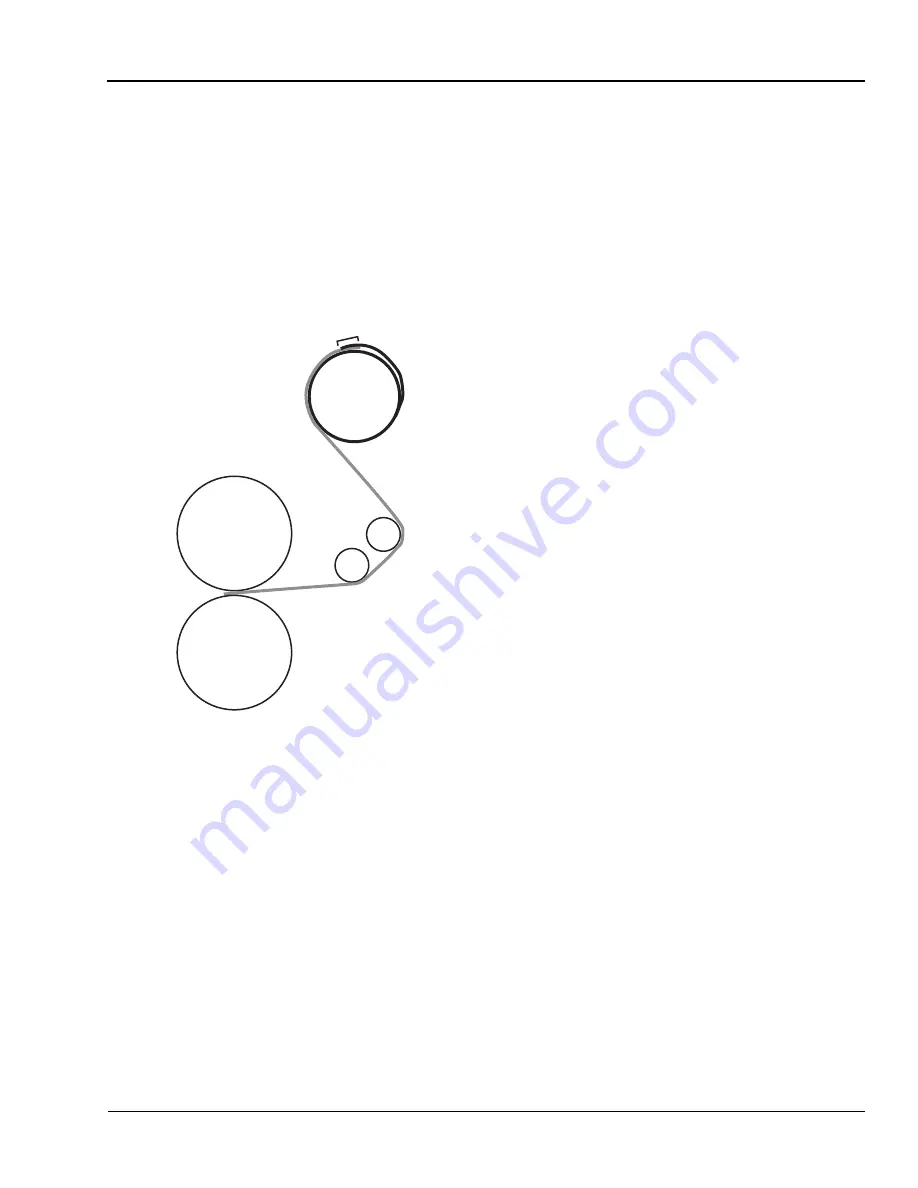
ORCA-IV Image Transfer Laminator Operation Manual
Operation
© GBC Pro-Tech 1998 October
3-15
4. Tape starting in the center and move to the sides.
The tighter and smoother the tape job, the less web
looseness that will have to be tensioned out later.
5. Decrease the brake tension until the splice passes
through the nip. If slitters are being used, be sure
that they have cut through the two layers of paper
and the tape at the splice. It is best to run slow as
the splice passes through the slitters and finish the
cut, if necessary.
Figure 3-10: Splicing Paper
3URFHVV&RQWURO&KDUWV
Process control charts allow you to record the way you
thread film through the machine's rolls and idlers
(called webbing) and the control settings for each prod-
uct and process. Process control charts are an excellent
tool for training new operators. They provide a "road
map" for correct machine setup and operation.
This section contains a completed chart for the basic
operation of the image transfer laminator.
GBC Pro-Tech image transfer laminators respond in a
very accurate and repeatable manner. The chart pro-
vides a way to set up each time, every time for repeat-
able performance by assuring that all controls are set to
optimum.
The process control chart should be kept in this manual
or in a book close to the image transfer laminator.
☞
NOTE
When trying new products and processes, remember
that GBC Pro-Tech's customer service representatives
are only a phone call away. In North America, call
1-608-246-8844 or fax 1-608-246-8645.
9LQ\O7UDQVIHU
6HWXS
1. See process chart 3-1 and diagram 3-1a on page
3-17.
2. Set the controls as follows:
•
Main Roll Air Pressure: 100 psi (689 kPa).
•
Pull Roll Clutch Air Pressure: 35 psi (241 kPa).
•
Pull Roll Up/Down: Down
•
Pull Roll Air Pressure: 80 psi (552 kPa).
•
Speed Adjust: 1-10 fpm (.3-3.0 m/min).
•
Upper Heater Controller: 290 °F (143 °C).
•
Cooling: Idlers on, cooling tubes as needed
New
Paper
Tape