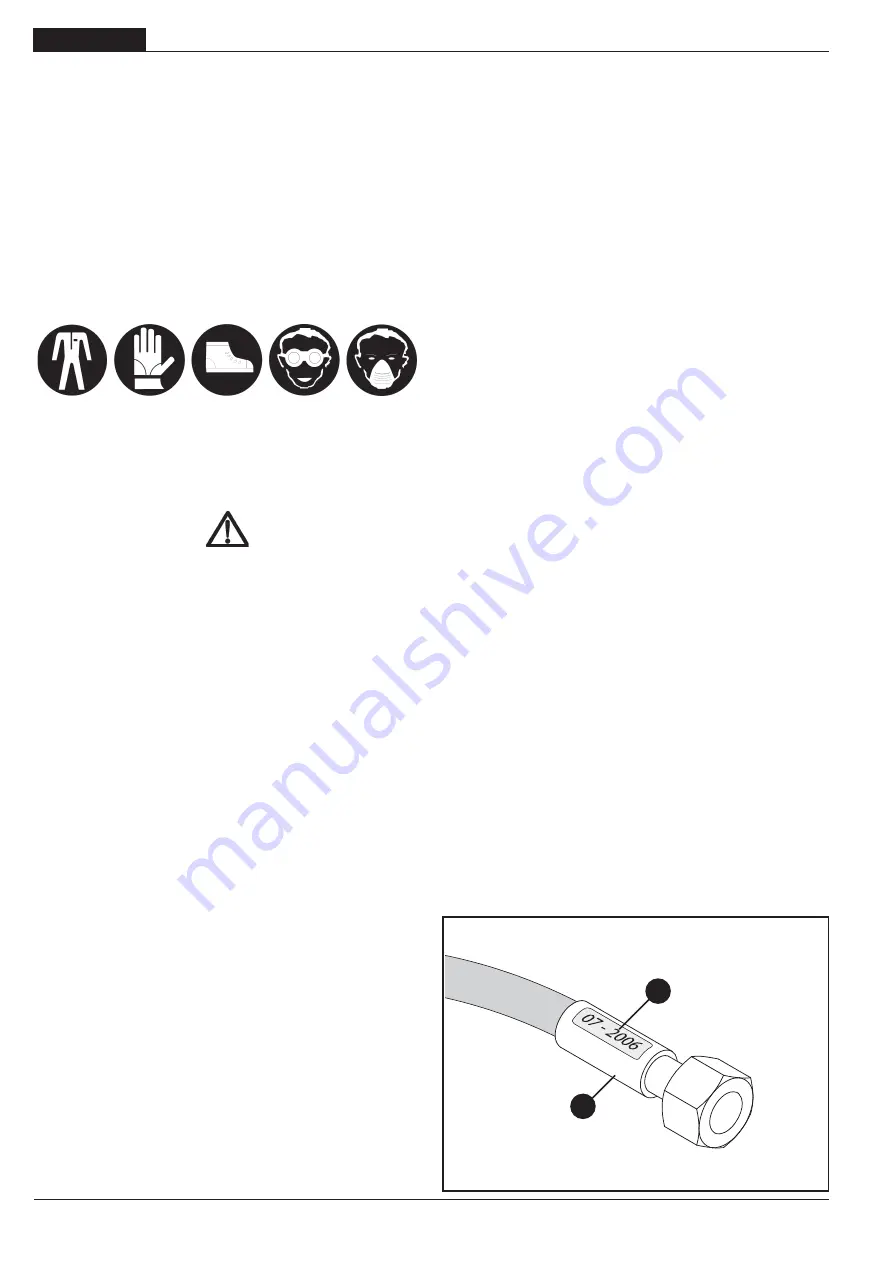
USE AND MAINTENANCE
56
-
cod. G19503220
ENGLISH
4.0 MAINTENANCE
Here follows a list of various maintenance operations to be carri-
ed out periodically. Lowered operating costs and a longer lasting
seeding machine depend, among others, on the methodical and
constant observation of mese rules.
The maintenance periods listed in this booklet are only indi-
cative and are for on normal conditions on use, therefore be
varied depending the kind of service, the more or less dusty
surroundings, seasonal factors, etc. For more serious condi-
tions of service, maintenance will logically be done more often.
All operations must be carried out by expert personnel,
equipped with protective gloves, in a clean and dust-free
environment.
Overalls
Gloves
Shoes
Goggles
Mask
All maintenance operations must be carried out with the ma-
chine hooked up to the tractor, the parking brake engaged,
the engine off, the ignition key removed and the equipment
sitting on suitable supports on the ground.
ATTENTION
USING OILS AND GREASES
- Before injecting grease, the nipples must be cleaned to avoid
mud, dustand foreign bodies from mixing with the grease,
otherwise they will reduce or even annul the effect of the
lubrication.
- Always keep oils and grease out of reach of children.
- Always read warnings and precautions indicated on the
containers carefully.
- Avoid skin-contact.
- After use wash the equipment thoroughly.
- Treat the used oils and polluting liquids in conformity with
the laws in force.
CLEANING
- The products used for cleaning must be disposed of accor-
ding to the laws in force.
- Clean and maintain the machine after putting any removed
guards back in position. Replace them with new ones, if they are
damaged.
USING PRESSURISED CLEANING SYSTEMS (Air/Water)
-
Do not pressure clean electrical components.
-
Do not pressure clean chromium-plated components.
-
Do not place the nozzle in contact with the parts of the
equipment, especially the bearings. Keep it at a min. distance
of 30 cm from the surface to be cleaned.
-
Always keep in mind the rules that regulate use of these
systems.
- Thoroughly lubricate the equipment, especially after cleaning it
with pressurised systems.
HYDRAULIC SYSTEMS
- Hydraulic systems must be maintained exclusively by skilled
operators.
- The hydraulic system is under high pressure; because of
the accident risk, when searching for leakage points special
auxiliary instruments should be used.
- In case of participation on the hydraulic system, to unload
the hydraulic pressure carrying all the hydraulic commandos
in all the positions some times after to have extinguished
the motor.
- Oil escaping at high pressure can cause skin injury with the
risk of serious wounds and infection. Call a doctor immedia-
tely if such an incident occurs. If the oil with surgical means
is not removed quickly, can take place serious allergies and/
or infections. Therefore, the installation of hydraulic compo-
nents in the tractor driver’s cab is strictly forbidden. All the
components of the system should be positioned carefully
to avoid parts being damage during use of the equipment.
At least once a year have the hydraulic pipes checked for
wear by an expert.
- Replace the hydraulic pipes if they are damaged or worn by
aging.
- Replace the hydraulic pipes every 5 years even if they have
not been used (natural aging).
Figure 39 (A) shows hydraulic pipes bearing the year of
manufacture as an example.
After the fi rst 10 hours of operation and then after every 50
hours, check that:
- all the elements of the hydraulic system are water-tight;
- all the joints are tight;
Before starting the machine up, check that:
- the hydraulic pipes are connected correctly;
- the pipes are positioned correctly, and they are free to move
during standard manoeuvres;
- any damaged or worn part is replaced, if necessary.
Replace the hydraulic pipes in the following cases:
- when external damage is identifi ed such as cutting, tearing
and wear due to friction, etc.;
- when they are deteriorated on the outer surface;
- when they are deformed beyond their natural shape due to
crushing, formation of bubbles, etc.;
- when leaks are identifi ed near the pipe sheath (B, Fig. 39);
- when the sheath is corroded (B, Fig. 39);
- 5 years after their manufacture (A, Fig. 39).
fi g. 39
A
B
Summary of Contents for S MARIA Series
Page 31: ...31 Notes cod G19503220...
Page 59: ...59 Notes cod G19503220...
Page 87: ...87 Notes cod G19503220...
Page 115: ...115 Notes cod G19503220...
Page 143: ...143 Notes cod G19503220...