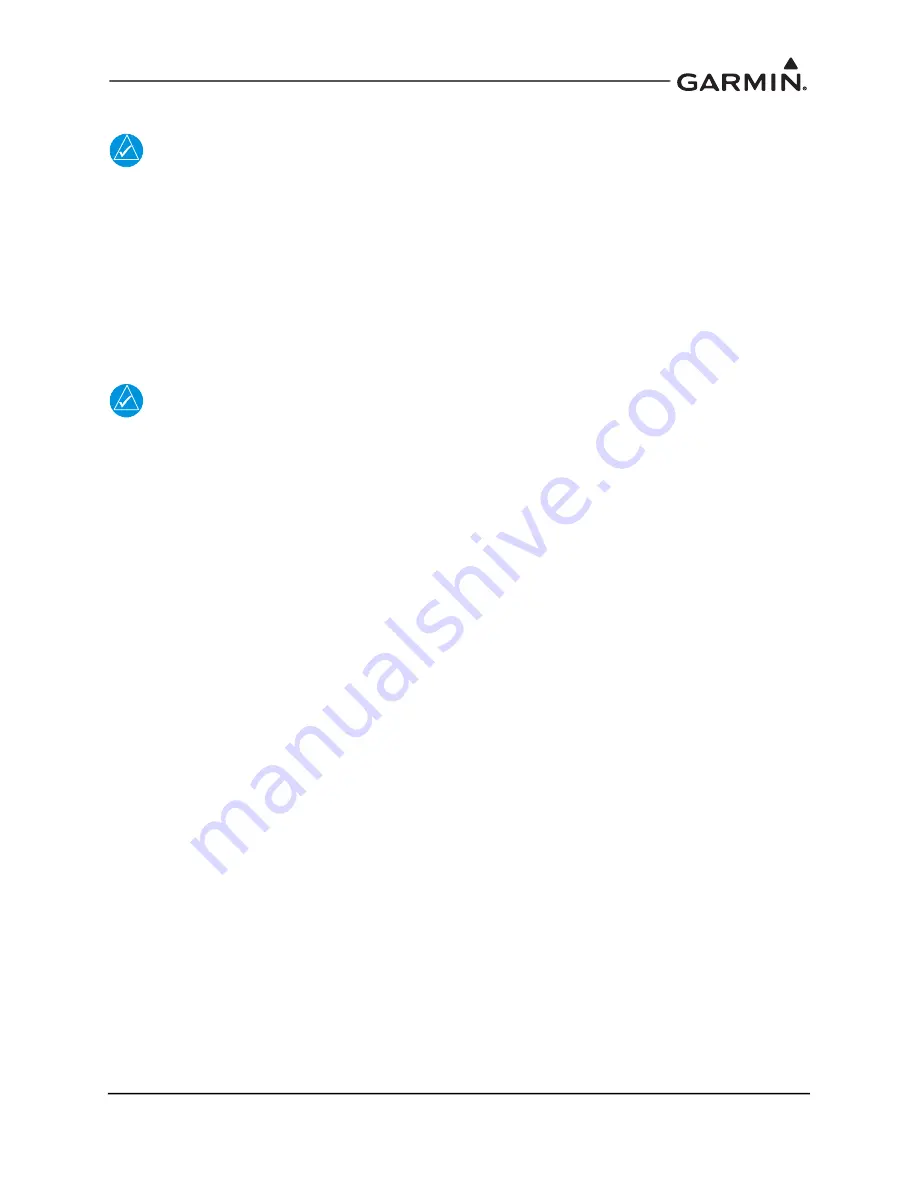
190-02081-03
GFC 600H HFCS Part 27 STC Maintenance Manual
Rev. 3
Page 6-14
6.2.2 Servo
NOTE
Ensure that the steps of Section 6.2.1 for the control rod linkage removal have been
completed prior to beginning removal of the servo.
Removal
1. If necessary, remove power from the GFC 600H FCS by pulling the FCS circuit breaker and gain
access to the roll, pitch, or yaw servo.
2. Disconnect the servo connectors J831-P, J831-R, or J831-Y from the servo.
3. Remove the safety wire and the four bolts holding the servo to the bracket.
Re-installation
NOTE
If necessary, it may be beneficial to accomplish the re-installation steps of Section 6.2.4
for the servo output arm and Section 6.2.3 for the shear fuse while the servo is attached to
the bracket in the rotorcraft.
1. Check the connector(s) and verify pins are not damaged. Repair if required.
2. Inspect servo bracket(s) to ensure secure attachment to the airframe. Refer to Figure 6-3 and
Figure 6-4 for details.
3. Check the unit electrical bond to the airframe meets the requirements of Section 4.5.
4. Attach the servo to the servo bracket. Refer to Figure 6-3 and Figure 6-4 for details.
5. Connect the servo connector J831-P, J831-R, or J831-Y to the servo.
6. Connect the control push-rod linkage in accordance with Section 6.2.1.