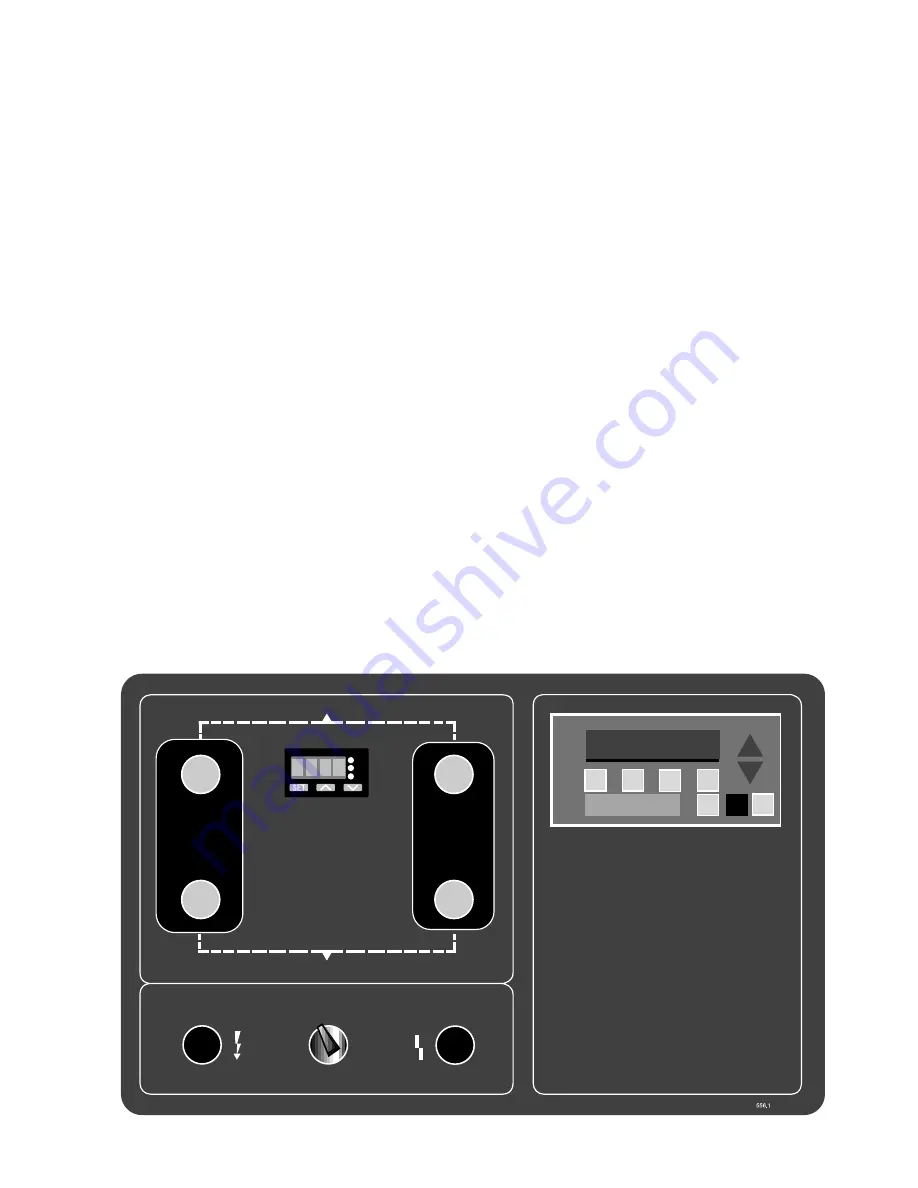
5
Figure 4.1 - Control Panel
4.0
Operation
4.1 Controls
A programmable logic controller (PLC) controls valve,
blower, and heater operation, monitors all critical
operating conditions, and indicates operating status and
fault conditions on an LCD display. The PLC receives
digital input data from pressure switches, temperature
switches and the operator interface. The operator
interface displays information about the dryer operat-
ing status and is used to change the dryer operating
mode.
4.2 Operating Modes - Description
A. Automatic and Manual Advance
The drying and regeneration cycles are divided into
discrete steps. The operator selects either auto-
matic or manual advance through the operator
interface. Selecting automatic advance enables a
timer in the PLC which advances the program step-
by-step according to the programmed schedule.
This is the normal operating mode to be used.
Selecting manual advance disables the PLC’s internal
timer and the operator can advance the program
one step at a time. This mode is used for diagnos-
tic purposes.
B. Auto-stop Mode
In this mode of operation the dryer program will
automatically stop when it reaches the beginning of
the next drying cycle. Auto-stop should be used
when the dryer is shut-down. This allows the
current regeneration cycle to be completed
without interruption and ensures that dry air will be
available when the dryer is restarted.
Auto-stop can only be enabled if automatic advance
is selected. Auto-stop can be used in either fixed
or demand cycle operation. When used with
demand cycle operation the dryer switches to a
fixed cycle; when the dryer is returned to normal
operation (auto-stop disabled) the dryer will return
to demand cycle operation.
Auto-stop is enabled or disabled through the opera-
tor interface. The dryer can be returned to normal
operation at any time by disabling auto-stop.
C. Fixed and Demand Cycle Operation
In fixed cycle operation, each tower is on-line
(drying) for a fixed time period regardless of the
operating conditions. In demand cycle operation, a
tower remains on-line until the desiccant bed has
been fully utilized. For lower than designed mois-
ture loads, this results in longer drying cycles,
longer time between regenerations and, therefore,
lower energy consumption. Demand cycle opera-
tion is an optional feature. The operator interface is
used to select the fixed or demand cycle.
D. Optional Dew Point Monitor
This option monitors and displays outlet pressure
dew points (-130
°
F to +50
°
F, -90
°
C to +10
°
C) and
provides an alarm signal if the dew point exceeds
user-specified set point. Field calibration may be
performed without taking it off-line or removing it
from the system. Recommended calibration
interval is 12 months. Contact the service depart-
ment for details.
Operation - The dew point is measured at the dryer
operating pressure and is displayed in Menu #1 on
the operator interface. If the dew point is outside
of the measurement range, display will indicate an
over-range (high dew point) or under-range (low
dew point) condition. A defective sensor assembly
or an electronics malfunction could also cause the
transmitter to indicate under-range.
OUTLET/Salida/Sortie
HEATER TEMPERATURE
Temperatura del Calentador
Température Du Réchauffeur
DRYING
Secando
Séchage
REGENERATING
Regenerando
Régénération
REGENERATING
Regenerando
Régénération
DRYING
Secando
Séchage
INLET/Entrada/Entrée
I
O
1
2
RDY
F1
F2
F3
F4
OPERATOR INTERFACE