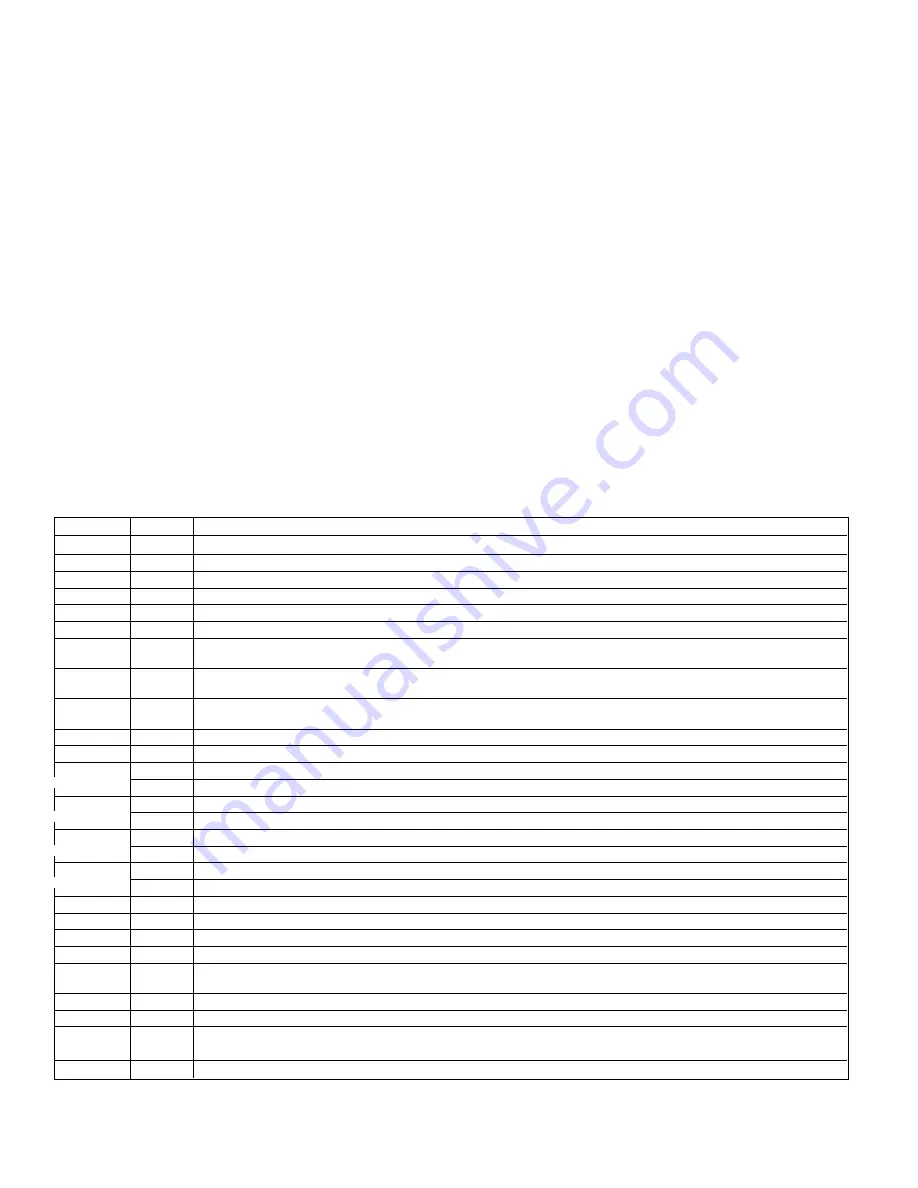
10
I/O Number
Device
Description
I0.0
LPS
Left tower pressure switch (N.O. contacts). The contacts close on rise at 40 psig (2.8 kgf/cm
2
) and open on fall at 10 psig (0.7 kgf/cm
2
)
I0.1
RPS
Right tower pressure switch (N.O. contacts). The contacts close on rise at 40 psig (2.8 kgf/cm
2
) and open on fall at 10 psig (0.7 kgf/cm
2
)
I0.2
BPS
Blower pressure switch (N.O. contacts). The contacts close at approximately 0.5 psig (0.035 kgf/cm
2
)
I0.3
HHC
Heater hi-limit controller output (N.C. contacts). The contacts close if the temperature exceeds 1400
°
F (760
°
C)
I0.4
LTS
Left purge temperature switch (N.O. contacts). The contacts close when the temperature exceeds 150
°
F (66
°
C)
I0.5
RTS
Right purge temperature switch (N.O. contacts). The contacts close when the temperature exceeds 150
°
F (66
°
C)
I0.6
DPM
Dew point montior output (N.O. contacts). The contacts close on rise at 0
°
F (-17.8
°
C) and open on fall at -40
°
F (-40
°
C)
(Optional)
I0.7
Jumper #1
This jumper is present on dryers equipped with the demand cycle option
(Optional)
I1.0
Jumper #2
This jumper is present on dryers equipped with two stage regeneration
(Optional)
I1.1 to I1.5
None
These inputs are not used
AIW0
(Optional)
Analog input module for optional dew point monitor.
Q0.0
1SOL
Left inlet pilot valve (solenoid #1). When the solenoid is energized, pilot air opens the left inlet valve
2LT
Left tower drying light
Q0.1
2SOL
Left inlet pilot valve (solenoid #2). When the solenoid is energized, pilot air closes the left inlet valve
3LT
Left tower regenerating light
Q0.2
3SOL
Right inlet pilot valve (solenoid #1). When the solenoid is energized, pilot air opens the right inlet valve
4LT
Right tower drying light
Q0.3
4SOL
Right inlet pilot valve (solenoid #2). When the solenoid is energized, pilot air closes the right inlet valve
5LT
Right tower regenerating light
Q0.4
5SOL
Left purge pilot valve. When the solenoid is energized, pilot air opens the left purge valve; when de-energized, pilot air closes the left purge valve
Q0.5
6SOL
Right purge pilot valve. When the solenoid is energized, pilot air opens the right purge valve; when de-energized, pilot air closes the right purge valve
Q0.6
7SOL
Left tower depressurization valve. The valve opens when energized and closes when de-energized
Q0.7
8SOL
Right tower depressurization valve. The valve opens when energized and closes when de-energized
Q1.0
9SOL
Repressurization pilot valve. When the solenoid is energized, pilot air opens the repressurization valve; when de-energized, pilot air closes the
repressurization valve
Q1.1
M
Blower motor starter
Q2.0
6LT, CR
Alarm light and remote alarm relay. Both devices are energized during any alarm condition (see Figure 4.10)
Q2.1
10SOL
Air sample switching valve. When the solenoid is energized, air is sampled from the right tower; when de-energized, air is sampled from the left tower
(Optional)
Q2.2 to Q2.7
None
These outputs are not used
Figure 4.6 - Programmable Controller Inputs and Outputs
4.8 Manual Advance
The manual advance feature is used to verify proper
operation of the dryer and to help identify the cause of
an alarm. The use of manual advance is described below.
Read Sections 4.1 through 4.4 before proceeding. Main-
tain the electrical power and compressed air supply to the
dryer while using manual advance.
A. Use the operator interface (see Section 4.4) to select
MANUAL advance (Menu #3). This holds the operating
cycle in its current step.
B. Access Menu #5 using the operator interface (see
Section 4.4) to view the selected cycle (fixed or
demand). Next, go to Menu #6 to view the current
step number. Then refer to Figure 4.7 (fixed cycle) or
Figure 4.8 (demand cycle). These figures show the
on/off status of the programmable controller (PLC)
inputs and outputs during each step of the cycle.
The input and output devices are described in
Figure 4.6. A brief description of each step is given in
Figure 4.9.
NOTE:
If the dryer has one stage regeneration
(standard), the program will skip steps 10 through 13.
C. Compare the LED indicator for each input and output
on the programmable controller with Figure 4.7 or 4.8
for the current step of the operating cycle. Any
differences indicate a potential problem with the
input or output device or the PLC.
D. With Menu #6 displayed, advance the operating cycle
one step by pressing the F2 key on the operator
interface. The step number on the display will update
to show that the cycle has advanced to the next step.
CAUTION:
When advancing the operating cycle
manually, be sure to allow time for depressurization
(steps L02, R02, L11, and R11) and repressurization
(steps L14 and R14) before advancing to the next step.
NOTE:
A false alarm for incomplete heating (Alarm L6
or R6) and/or early dew point breakthrough (Alarm L2
or R2) may occur while using the manual advance
feature.
E. Repeat the procedure in Sections 4.8.C and D until a
complete cycle has been examined.