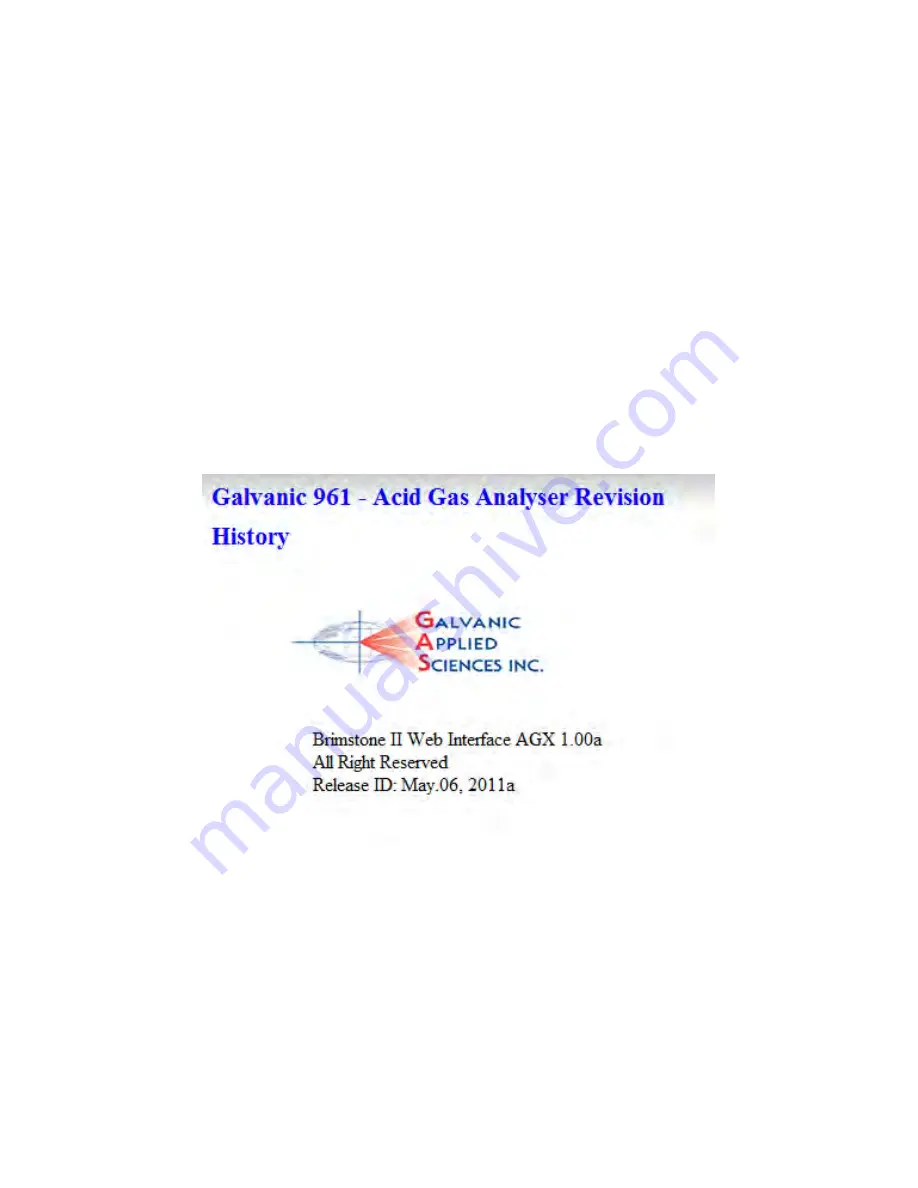
Revision 1
61
9/10/2019
5.5 Help Section
5.5.1 Drawings
A number of assembly drawings are included in the application program. These are
reproduced as Chapter 9 of this manual.
5.5.2 User Manual
This manual can be accessed via the
User Manual
page
5.5.3 Revision History
The
Revision History
page (Figure 5-15) presents the release ID number of the software.
Please refer to it when making inquiries about the system.
Figure 5-15: Revision History
Summary of Contents for 962-AGX
Page 43: ...Revision 1 43 9 10 2019 Figure 4 13 Network Sub Panel...
Page 86: ...Revision 1 86 9 10 2019 Figure 9 1 Customer Connections...
Page 87: ...Revision 1 87 9 10 2019 Figure 9 2 Analyzer Components...
Page 88: ...Revision 1 88 9 10 2019 Figure 9 3 Inputs and Outputs...
Page 89: ...Revision 1 89 9 10 2019 Figure 9 4 AC Wiring Overview...
Page 90: ...Revision 1 90 9 10 2019 Figure 9 5 DC Wiring Overview...