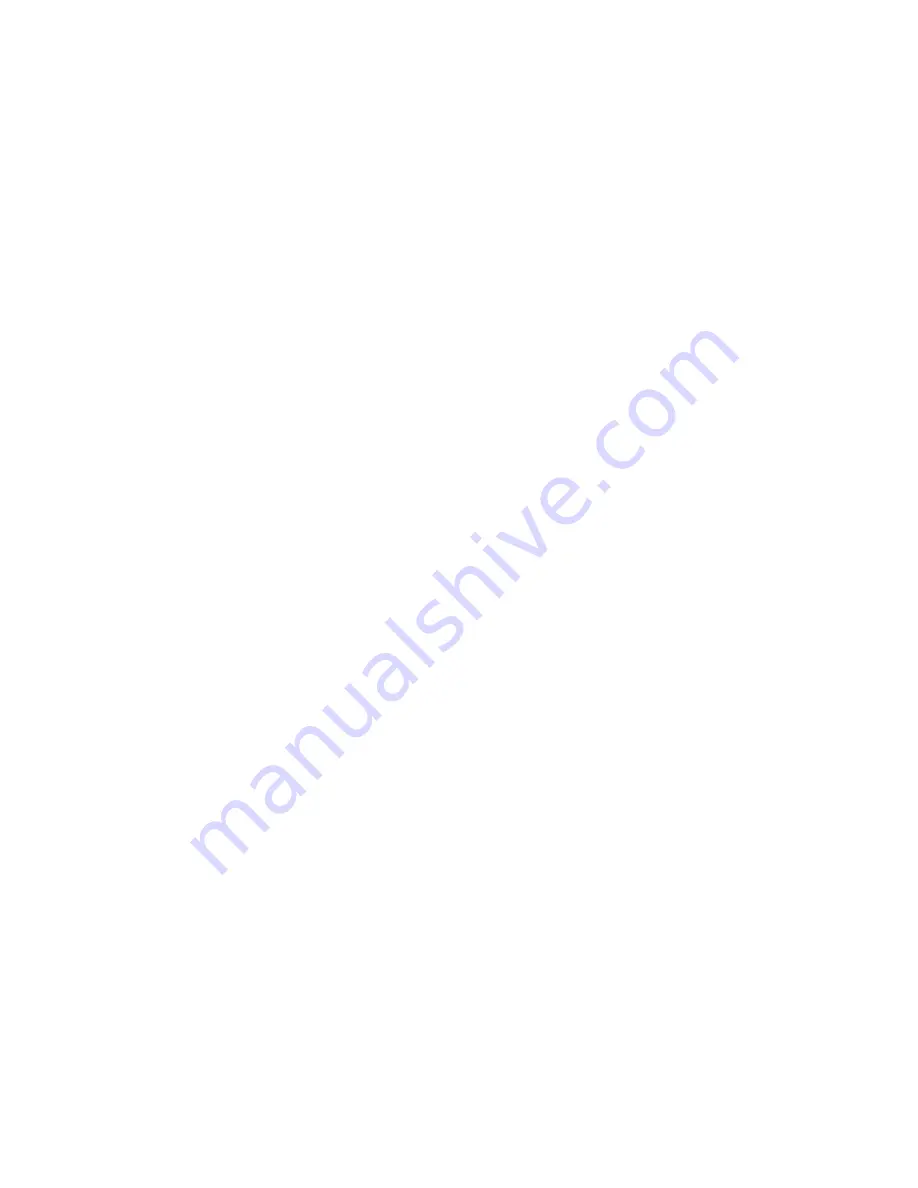
Revision 1
24
9/10/2019
The purpose of this indicator is to signify the analyzer is approaching the extremes of
optimum levels. When this indicator is in the
Warning
state, the analyzer will continue to
function normally, producing useable outputs. The analyzer will self-clear the ‘Warning’
condition and automatically return to
Normal
status once the offending parameter is
found to be within range.
c) Mode (Calibrate / Run) Indicator
The
Mode (Calibrate / Run)
output indicates when a zero calibration or a manually
requested forced zero purge is in progress. This indicator will be in the ‘Run’ state
unless
one
of the following is true:
•
A clock triggered (auto) zero calibration sequence is in progress.
•
A manually requested zero calibration sequence is in progress.
•
The analyzer has been placed in the ‘Force Zero’ mode (manually).
•
The analyzer is not receiving mains power.
When this indicator is in the
Calibrate
state, the analyzer is not measuring the process
acid gas. When, during a calibration sequence, the zero calibration adjustment is
complete, this indicator is held in the
Calibrate
state for a period of time specified by the
Zero Hold Interval configuration parameter. This buffer period allows the analyzer to draw
process gas and commence measurement before clearing the
Calibrate i
ndicator. At the
expiration of the Zero Hold Interval, this indicator returns to the
Run
state.
d) Control (Manual / Auto) Indicator
The
Control (Manual / Auto)
output indicates the validity of the analog output signals.
When this indication is in the
Auto
state, the analyzer believes that output data are real
and current measurements of the tail gas process stream. Under conditions where the
validity of the output data is suspect, the analyzer places the
Control
flag in the
Manua
l
state. This indicator will be in the
Auto
state
only when ALL
of the following are true:
•
The Status indicator is in the
Normal
state (
i.e.
no instrument fault).
•
The Mode indicator is in the
Run
state (
i.e.
not in calibration).
•
The computer’s front panel
On Line / Off Line
switch in is the
On Line
position (
i.e.
not
being serviced).
•
The analyzer is receiving mains power.
The purpose of this indicator is to signify when the analyzer outputs are suitable for use
as closed loop control inputs. When this indicator is in the ‘Manual’ state, no control
action should be taken on the basis of the analyzer output signals. This indicator is
generated on the basis of the other analyzer indicators, as well as the condition of the
manual
On Line / Off Line
selection on the display. The
Control
flag state is automatically
returned to
Auto
once the offending condition (s) has cleared. When in
Manual
, the Track
and Hold outputs are held.
e) Typical Usage of the Digital Indicators
For most applications, connection of the
Control
indicator to the plant control room is all
that is required. From an operations perspective, it is only important to know that analyzer
data are valid or not. It is insignificant to an operator what the actual cause of invalid data
is, but it is important that the data be known to be invalid. It is desirable to enunciate the
state change of this indicator from
Auto
to
Manual
. Although the 962-AGX software
Summary of Contents for 962-AGX
Page 43: ...Revision 1 43 9 10 2019 Figure 4 13 Network Sub Panel...
Page 86: ...Revision 1 86 9 10 2019 Figure 9 1 Customer Connections...
Page 87: ...Revision 1 87 9 10 2019 Figure 9 2 Analyzer Components...
Page 88: ...Revision 1 88 9 10 2019 Figure 9 3 Inputs and Outputs...
Page 89: ...Revision 1 89 9 10 2019 Figure 9 4 AC Wiring Overview...
Page 90: ...Revision 1 90 9 10 2019 Figure 9 5 DC Wiring Overview...