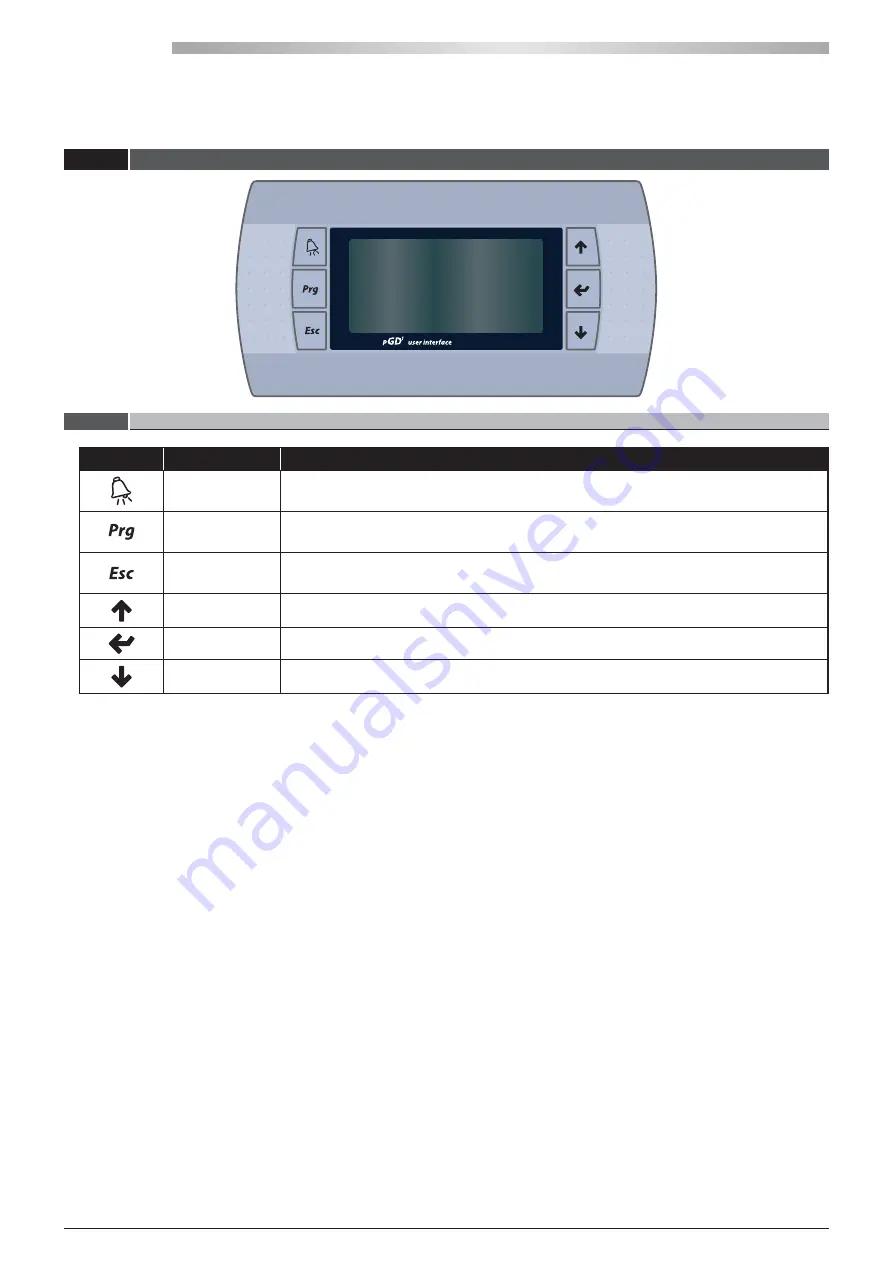
HIWARM
42
All copying, even partial, of this manual is strictly forbidden
RG66007967 - Rev 02
Key
Description
ALARM
Press the ALARM key to reset the alarms. The button lights up when an alarm is triggered.
PROGRAM
Press the PRG key to enter the main menu.
ESC
Press the ESC key to move up one level in the menu.
UP
Press the UP key to go to the next screen or increase the value of a parameter.
ENTER
Press the ENTER key to go to the parameter field to be edited and to confirm any change.
DOWN
Press the DOWN key to go to the previous screen or decrease the value of a parameter.
6.3
USER INTERFACE
6.3.1
DESCRIPTION OF THE KEYPAD