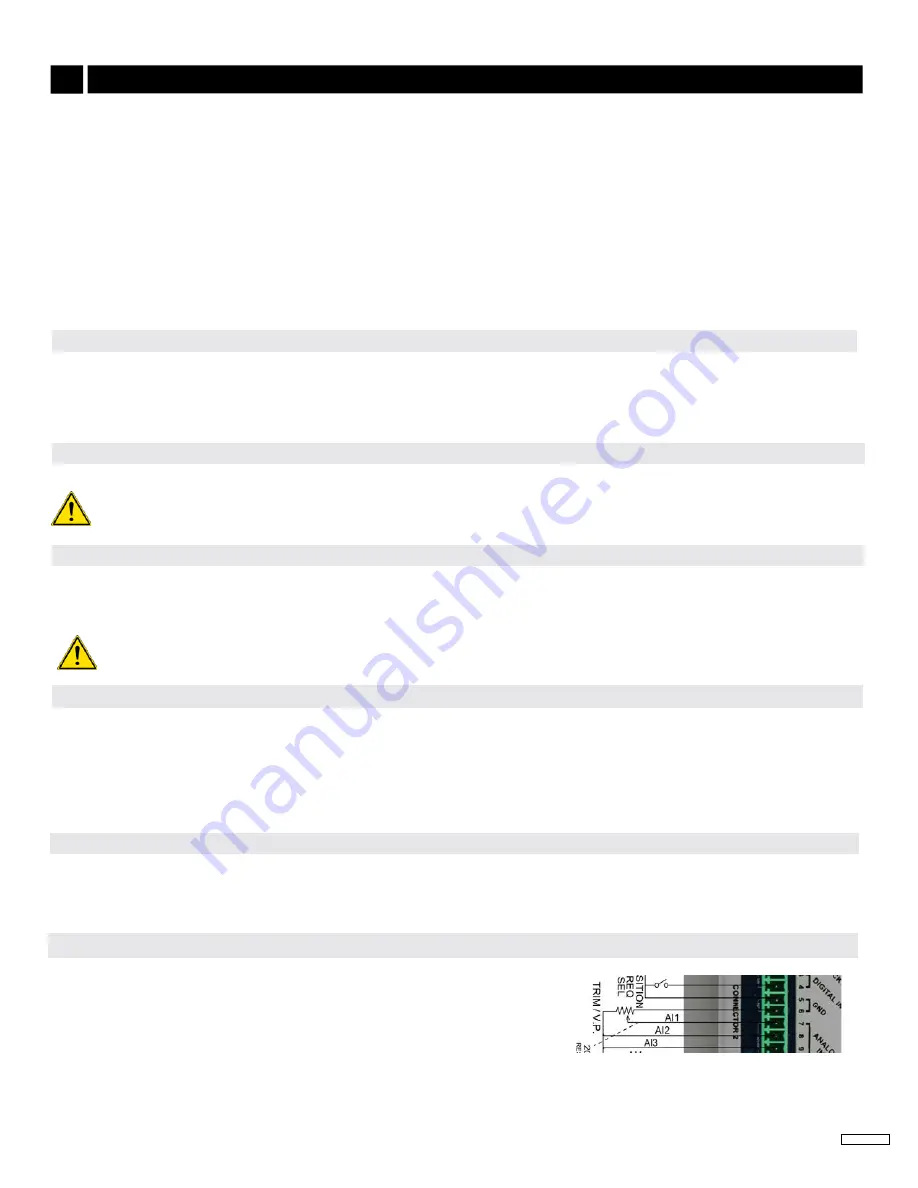
6
Governors America Corp. © 2021 Copyright All Rights Reserved
EEG7500 Enhanced Electric Governor 8-2021-A8 PIB5115
•
Wires must be twisted and/or shielded for their entire length (14 turns per foot).
•
Gap between speed sensor and gear teeth should be > 0.02 in [0.51 mm].
•
Speed sensor voltage should be at least 1 V AC RMS during crank.
If the EEG7500 detects no input from the magnetic (mag) pickup, the EEG will set the actuator to 0 V DC and set the speed
to 0 rpm.
Terminals A and B are dedicated to actuator usage. They provide input for bidirectional devices such as torque motors which require
specific polarity settings.
Proportional actuators are not polarity sensitive. See your specific actuator manual for details.
Connect the engine battery to the Terminals C and D.
Terminals 3 and 4 are digital inputs used to support incoming digital, analog, or virtual (J1939) signals. An external switch can also be
used between Terminals 3 and 4 (Ground to Terminal 5) to select assigned fixed speed settings.
From the GAConfig Tool set I/O Configuration
Physical Input Mapping
Run/Stop Input - set to Digital Input 1 or 2 to match the
external switch wiring.
6
EEG7500
WIRING DETAIlS
A 15 A fuse and power switch must be installed on the positive battery lead going to Terminal D.
actuator connection: connector 1 - Terminals a and B
Digital Input 1 and 2 - Speed Input routing: connector 2 - Terminals 3 and 4
magnetic Speed Pickup Signal: connector 2 - Terminals 1 and 2: Speed In / Speed ref
Battery connection: connector 1 - Terminals c and D
The EEG7500 provides broad configuration capabilities. The wiring provides a dedicated actuator and mag pickup input as well as
configurable analog and digital inputs to support direct communications like CAN (J1939) using the GAConfig Tool software.
The EEG7500 supports analog and digital input connections and electrical connections to the EEG terminals. These connections
are then mapped to specific locations in the GAConfig Tool software where you add expected settings including speed and all related
engine tuning setups in various speed modes (configurations).
The output mapping is done for both input connections and for specific output results, for example meeting a specific speed might
output a warning or shut down or engage a particular piece of hardware.
For example, with an actuator installed, create a variable speed setup with GAConfig Tool. Setting the output of the actuator and the
Speed Switch 1 output to a J1939 source such as the engine Electronic Control Unit (ECU) enables speed settings or vehicle miles to
be monitored, sends warnings for things like past due oil changes, or shuts down the engine.
Terminal 5 provides a digital ground. Terminal 6 provides the internal ground for use with external trim or variable speed potentiometers.
An external switch can be added between Terminals 3 and 4 with ground to Terminal 5 to select assigned fixed speed settings using the
GAConfig Tool
Digital and analog Ground reference: connector 2 - Terminals 5 and 6:
Terminal 7 is the analog input from external trim or variable speed potentiometer.
Speed trim uses a
to vary the engine speed remotely.
The GAConfig Tool
parameter lets you adjust speed trim ±10 % based
on the minimum and maximum voltage configured for the variable speed input. Trim
speed logic is used with fixed speed settings.
analog Input: connector 2 - Terminal 7